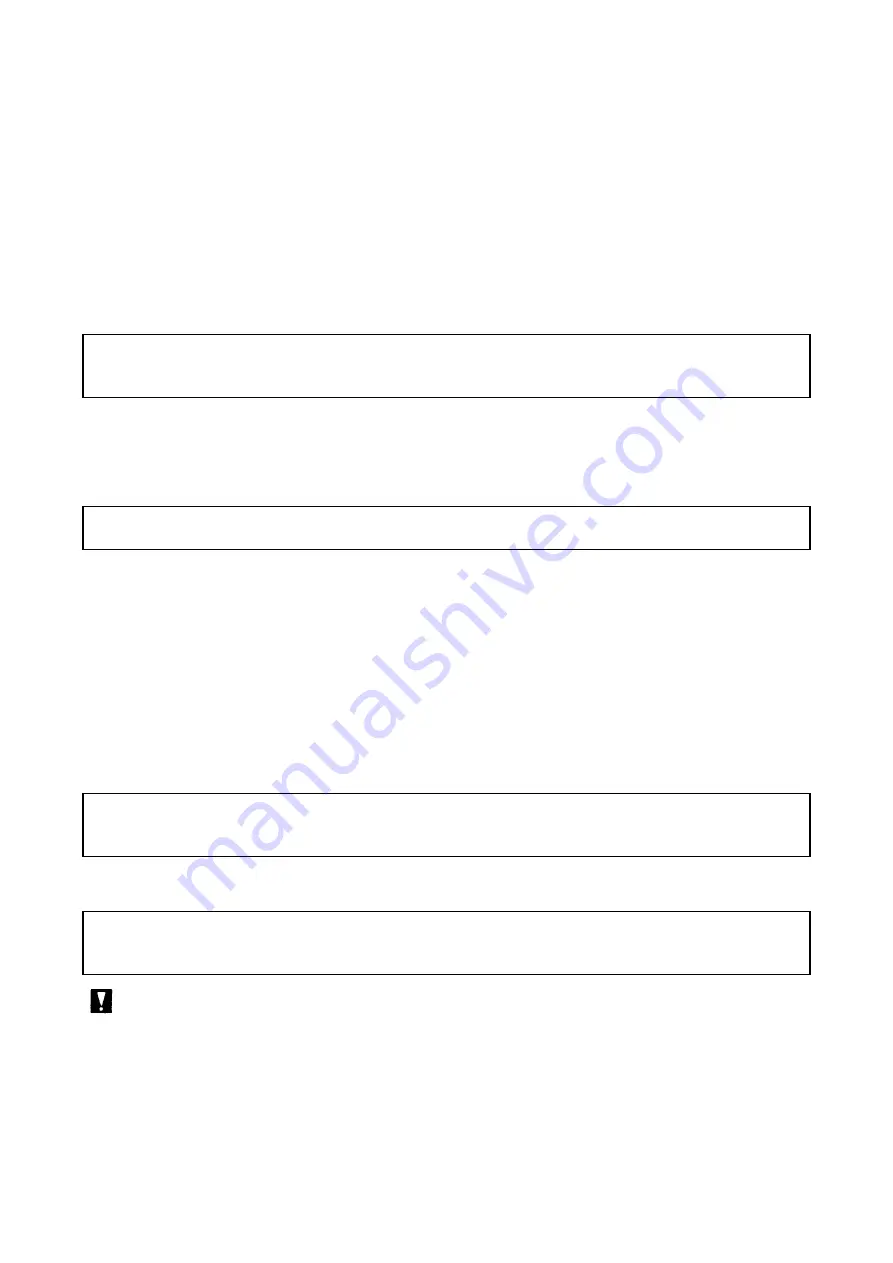
4-33
2. The allowable power loss time differs with the models. The range is from 1second to 2 second.
3. 04-03=0: as power lost, the inverter will not start.
4. 04-03=1: if the loss time is less than the value of 04-04, the inverter will Spin Start in 0.5 second
as the power is resumed and restart times are infinite.
5. 04-03=2:the power lost for long time, before the inverter lost the control power for the CPU, the
inverter will restart according to the 00-03 and 04-05 setting and status of external switch as the
resumed.
Note:
00-03=1 04-05=0 04-03=1or 2 after a power loss for a long time, please turn OFF the power
and power switches to avoid any possible injury to operators and machines when the power is
resumed unexpectedly.
04-05 : Auto Restart Method:
=0 : Enable Speed Search
=1 : Normal Start
1. 04-05=0: When auto-restarting the inverter will detect the rotating speed of the motor. The Motor
will be controlled to accelerate from the present speed to the target speed.
2. 04-05=1: The inverter restart from 0 speed to set frequency in acceleration time when
auto-restart.
04-06 : Auto Restart Delay Time (Seconds) : 0 ~ 800.0 second
04-07 : Number of Auto Restart Attempts : 0 ~ 10 times
1. 04-07=0: The inverter will not auto restart after trips due to fault.
2. 04-07>0, 04-06= 0:
The inverter will conduct SPIN START in 0.5 second after trips due to fault. The motor will
Coast to stop while the output is switched off, once the rotating speed is determined then it
will
accelerate or decelerate from this speed to the running speed before the fault.
3. 04-07>0, 04-06>0:
The output will be stopped for a period which is determined by the 04-06 after a fault trip. Then,
spin start to set target frequency.
4.
Auto restart after a fault will not function while DC injection braking or decelerating to stop.
04-08 : Reset Mode Setting
0 : Enable Reset Only when Run Command is Off
1 : Enable Reset when Run Command is On or Off
04-08=0 Once the inverter is detected a fault, please turn Run switch Off and then On again to
perform reset, otherwise restarting will not be possible.
04-09 : Direct Running After Power Up
0 : Enable Direct running after power up
1 : Disable Direct running after power up
Danger:
1. 04-09=0 and the inverter is set external terminal controlled (00-03/00-04=1), if the run switch is
ON as power is supplied, the inverter will auto start. It is recommend that the power is turned off
and the run switch is also off to avoid possibility of injury to operators and machines as the
power is reapplied.
Note: IF this mode is required all safety measures must be considered including warning labels.