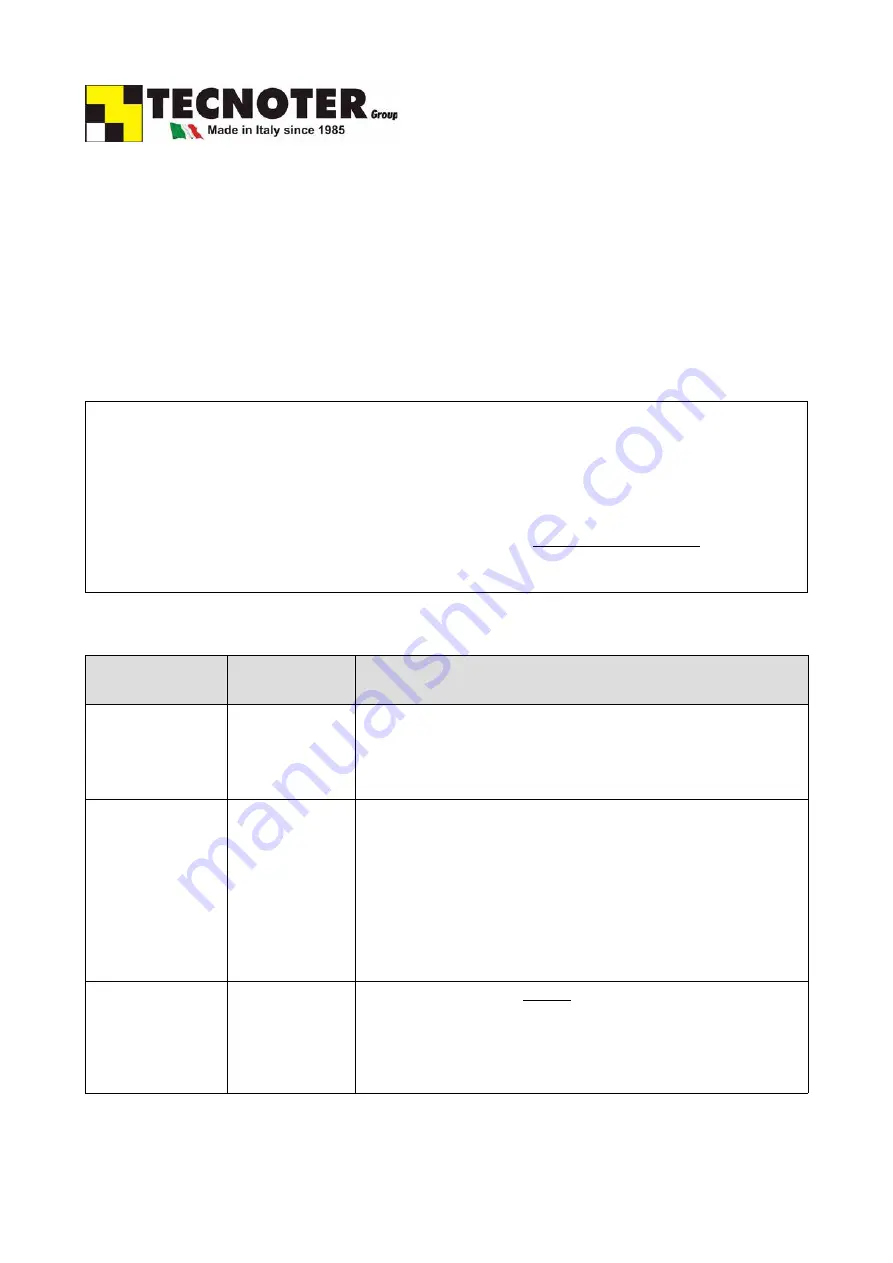
5 Standard maintenance
The following operations have to be executed in the indicated times.
In case instructions will not be followed, the Manufacturer will be relieved from any
responsibility for the effects of Warranty.
Some of such operations, although easy, have to be done by Qualified Operators only.
IMPORTANT:
Operations indicated with the symbol (*) must be executed ONLY by Tecnoter's official
network.
Operations indicated with the symbol (!) are absolutely mandatory
Programmed Maintenance Table:
Frequency
State of the
system
Inspection, maintenance
Every starting
In use
Visual and acoustic check of the correct functioning of each part of the
machine
Visual check of the cleaning of the washing lines
Visual check of the state of the washing fluid
Visual check of the structural integrity of the system
Daily
In use
Check the safety systems
Check the status of the oil absorbent and replace it when exhaust
Check level and quality of fluids
Clean the photoelectric sensor
Check system integrity
Removal of visible debris larger than 30 mm on their longer side
Visual check of leakages
Start a manual cycle pushing and holding the “manual cycle” button for
30 seconds and verify the correct function of each part with particular
attention to the correct functionality of the mud extractor
Every week
Isolated for
maintenance
Cleaning and lubrication with oil of extraction chain (!!)
Check condensation in the electric panel
Check the state of blades on the extraction chain, and replace them when
necessary
Tecnoter srl unipersonale
Wheel washing
system
RC4.32
E16CL4
S/N
Page 34/39
Rev: 1.42 –
22/02/2017