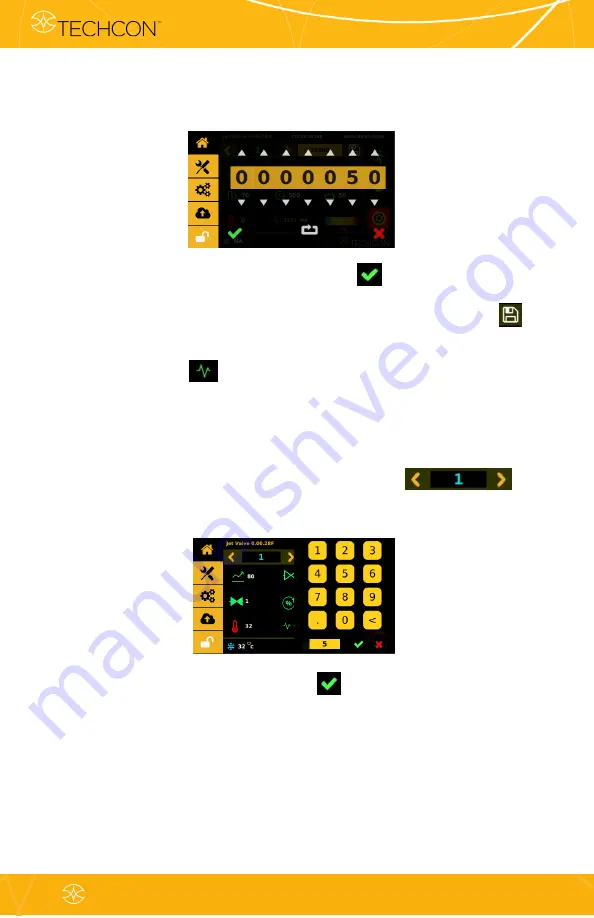
17. Touch the up and down arrows to set the desired number of strokes per
dispensing cycle.
18. Touch the ‘Accept’ icon to save and exit
19. Enter all desired dispensing parameters, then touch the ‘Save’ icon.
Note:
The system will automatically calculate and display the operating
frequency
based on the entered dispensing parameters.
9.5.6
Calling Up Dispensing Parameters
The controller has 50 memory cells store all dispensing parameters.
1.
Touch the forward or backward arrow to select
the desired memory cell or touch the value to type in a specific
location.
2.
Touch the ‘Accept’ icon to exit.
48
Jet Valve Dispensing System User Guide
TS9800
& TS980