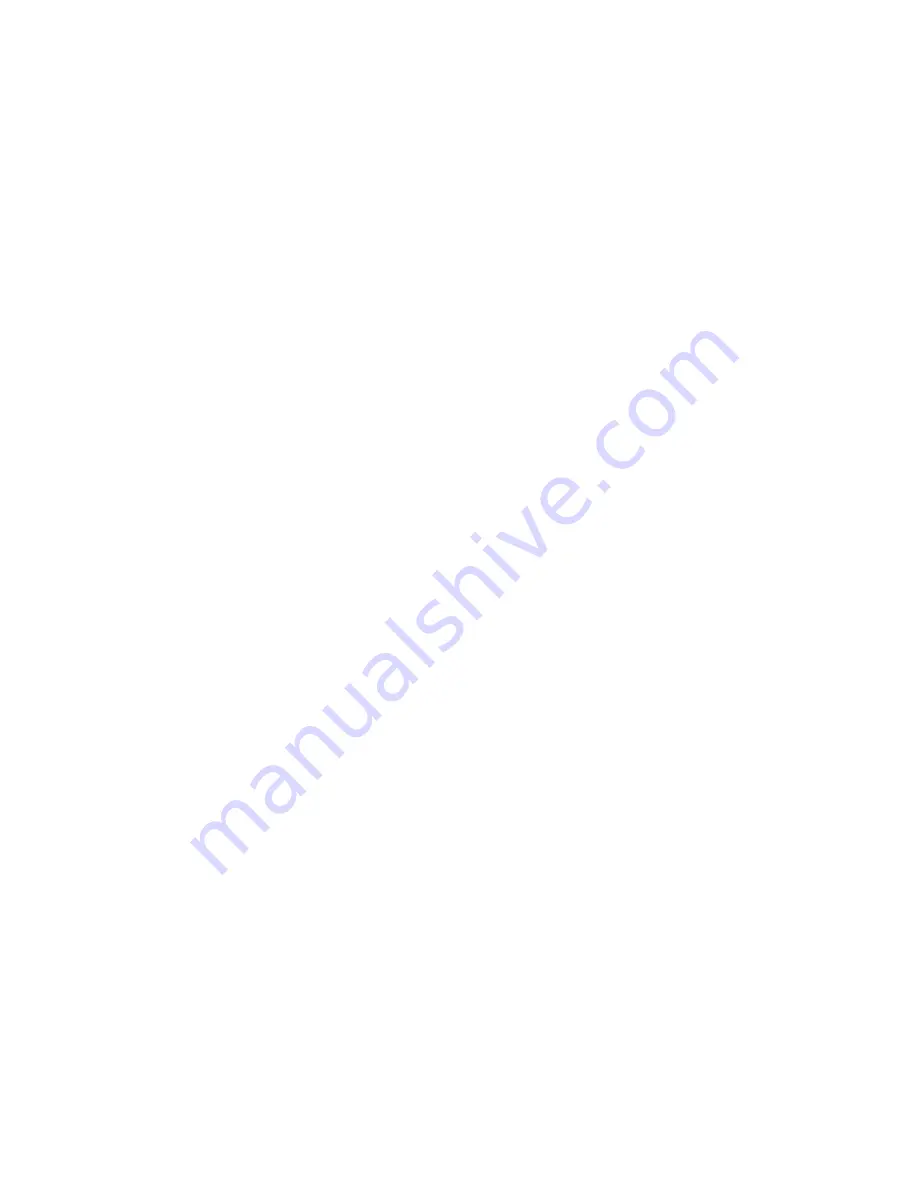
33
Front Droop
; is the amount of down travel the shocks allow the suspension arms to move. With standard 2.5" tall tires you will want
to maintain between a 2mm and 4mm shock droop. This is easily measured by removing the front tires and setting the chassis on the
droop gauge (included) so that the gauge extends across the chassis with the graduated notches to one side. Slide the gauge inward
using the set screw boss on the bottom of the spindle carrier as your reference. The set screw boss should just clear the 2mm
(minimum) step. Repeat this for the other side making sure that both sides are the same. Less droop makes the chassis react quicker
but is not as good on bumpy tracks. More droop reduces steering into the turn and slows down the overall reaction. This will also
make the chassis more stable on bumpy surfaces.
Front Diff
; running the diff a little tighter will give less off power turn-in but increase on power steering as you exit a turn. Running
it a little looser will give more initial turn-in but make the car want to "push" (lose steering) on exit.
Front Spool
; Running the front spool will give your car less off-power steering, but like a oneway, it will give you more forward drive
and more on-power steering. Also with the spool, your car will be more stable under braking, unlike a oneway.
Ride Height
; is the height of the chassis in relation to the track surface. Initially, set the front and rear ride height to 1/4" (6mm). This
will workwell on parking lot and bumpy surfaces. This will also generate more weight transfer and chassis roll, which can help on
slick surfaces. Lowering the ride height will make the car change direction quicker and should be helpful on high traction surfaces and
carpet.
Battery Position
; Moving the battery pack forward will give more steering and less rear traction. Moving the pack to the rear will
increase rear traction and diminish steering slightly. Splitting the pack leaving an empty space in the middle will have various effects
depending on the traction and size of the track.
Belt Tension
; can be run a little looser on long tracks and with stock motors. It is normal for the belt to skip (2 or 3 clicks) under
heavy braking without doing harm to the belt. Do not run the belt too loose or it will drag on the chassis and bottom cover hurting
performance.
Rear Shock Location
; leaning the shocks in (toward the center of the tower) frees up the back end of the car, allowing easier rotation
in the turn. This might be helpful for fast flowing tracks where corner speed is critical. Moving the shocks out (away from the center
of the tower) will give more forward traction but slows the initial reaction into the turn with a more abrupt rear rotation. This can be
good for tight tracks.
Rear Camber Link
; Moving the rear camber link to the outside position (shorter) on the tower and/or the inside position of the hub,
will give more traction and chassis roll but less steering and stability. This should also carry more corner speed and help on slick
surfaces. Moving the camber link to the inside position (longer) will increase stability but slow down rear rotation. Moving the link to
the lower hole position on the shock tower will result in less forward traction and more sidebite in low speed turns. It will also
increase corner speed on high speed, on-power sweeping turns. Moving the link to the outside position on the hub will give less
chassis roll.
Rear Toe-in
; There is 2 degrees of toe-in per side stock. Adding toe-in will create more forward traction and make the car freer on
entering a turn. This is good for slick surfaces. Too much toe-in will make the car twitchy and hard to drive.
Camber
; refers to the angle of the wheels/tires in relation to the track surface when viewed from the front or back. Negative camber
means that the top of the tire leans inward toward the chassis. Positive camber means the top of the tire leans out away from the
chassis. Adjust for optimum tire wear as noted for front camber.
Rear Anti-Squat
; is like the "kick-up" at the front except it works slightly different. Marked and used like the front, you can choose
from 0, 2, and 4 degrees of anti-squat (pin angle). Zero anti-squat is the starting point. Adding (from 0, 2, 4 degrees) will reduce rear
grip and allow easier rotation into a turn and increase the traction out of the turn. This is good for slicker track surfaces.
Rear Roll Center -
We have included new roll center mounts with your XXX-S Graphite. The kit is built with low roll center mounts
in the rear. From our testing we have found that the low roll center in the rear has yielded the best results on most tracks, including
carpet tracks on foam tires. Low roll center gives the car more roll in the rear, while increasing mid corner rotation. There is an
optional high roll center for the rear to achieve different handling characteristics. We have found that high roll center keeps the car
flatter through the turns and also transitions right to left quicker. When running high roll center you will have to mount the rear pivot
in the higher set of holes on the diff cover.