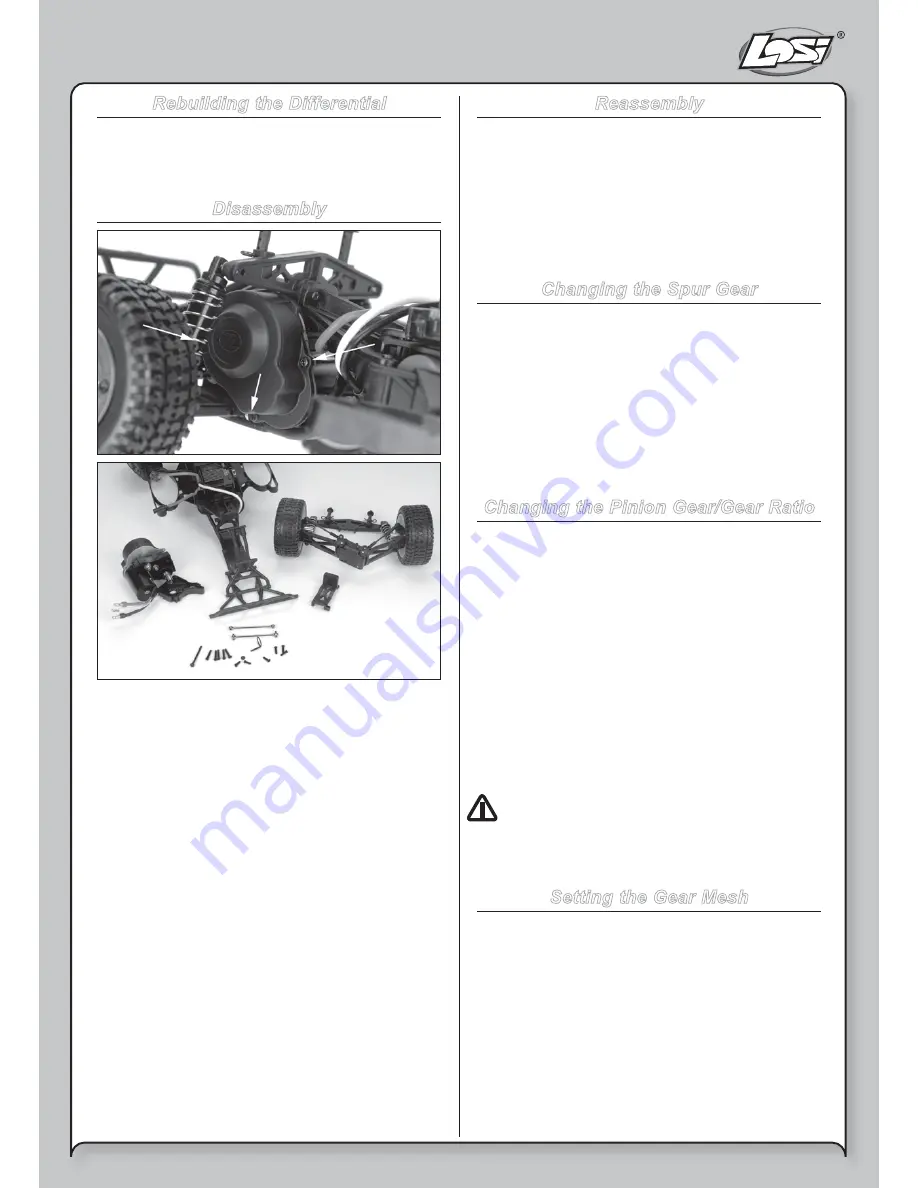
Rebuilding the Differential
The gears in the differential will wear over time. The same
is true for the outdrives, driveshafts, and rear axles. We
suggest using a small rag or paper towel to lay out the parts
you remove to make it easier to reassemble.
Disassembly
1. Unplug the 3 motor wires from ESC.
2. Remove the gear cover (three screws pictured)
3. Remove the 2 screws on the front of the rear shock
tower that attach to the rear upper cage. Once the
screws are removed, rotate the rear cage toward the
rear enabling access to the rear camber block.
4. Remove the 2 screws attaching the rear camber block to
the transmission case.
5. Remove 4 screws from rear skid plate and remove
transmission from vehicle.
6. Remove bracket on top of transmission by removing the
2 front screws and removing the long screw (secured
with a bolt), which passes through the transmission from
the motor plate side.
7. Remove the left side of the gearbox by removing the
three screws.
8. Remove any shims on the bevel gears (not used on all
models) and set them aside so they can be reinstalled in
the same location.
9. Carefully remove the large plastic sun gear and the
bevel gears on either side of it. You can use the
removed differential assembly as a guide for putting
together the replacement unit. For the best performance
Losi Grease (LOSA3066) can be applied to these gears.
10. Remove the center mounted idler gear from the
gearbox. Remove the shaft and push the ball bearings
out of both sides. Install these bearings in the new gear.
Reassembly
Replace the idler gear and shaft into the center of the same
right side of the gearbox. Replace any shims removed from
the right bevel gear and slide it through the lower bearing.
Replace any shims that came off of the left side bevel gear
and allow it to slide through the lower bearing as you put the
left gearbox half back into position. Replace the screws and
reinstall the rebuilt gearbox using the above steps in reverse
order. Consult the exploded view in the back of this manual
for more details.
Changing the Spur Gear
Remove the gear cover by removing the three small screws.
If you are replacing the spur gear with one of a different size
(number of teeth), you must first loosen (do not remove) the
two screws that secure the motor and slide it back slightly.
Remove the 3mm nut at the end of the slipper shaft and all
of the slipper parts on the outside of the spur gear as well
as the old gear. Place the new spur gear into position and
replace the slipper parts. If you have changed the size of
the spur, see Setting the Gear Mesh below. After you have
changed the spur gear, you will have to adjust the slipper as
described elsewhere.
Changing the Pinion Gear/Gear Ratio
Before you change the pinion gear ask yourself why you are
doing it. In general, if you change to a larger pinion the top
speed will improve but you will see less acceleration and
run time. This would only be advisable for really long track
layouts with few tight turns. Changing to a smaller pinion
will give you quicker acceleration and possibly a bit longer
run time but a little less top speed. This would be good for
short layouts or when running hotter motors. The pinion on
the Mini SCT offers the best balance of both. To change the
pinion, remove the gear cover, loosen the motor screws, and
slide the motor back. Use a pair of small needle-nose pliers
between the motor plate and back of the pinion to push the
pinion off. Place the new pinion on the end of the motor shaft
and, using the flat of the pliers or a similar flat tool, push it
on to the same position as the one removed. See Setting the
Gear Mesh below.
CAUTION
: When running aftermarket motors, check
with the motor manufacturer for correct gearing. Never
over-gear the motor as it can cause overheating, damaging it
and the speed control.
Setting the Gear Mesh
The motor screws should be slightly loose. Slide the motor
forward allowing the pinion gear to mesh with the spur gear.
Snug (not tight) the bottom motor screw and try rocking the
spur back and forth. There is a slight bit of movement before
the motor is forced to turn over. If not, pull the top of the
motor back slightly and recheck. If there is too much slop
between the gears, push the top of the motor forward. When
set properly, the wheels can be spun forward freely with
very little noise. Make sure to tighten both motor screws and
replace the gear cover before running.
10