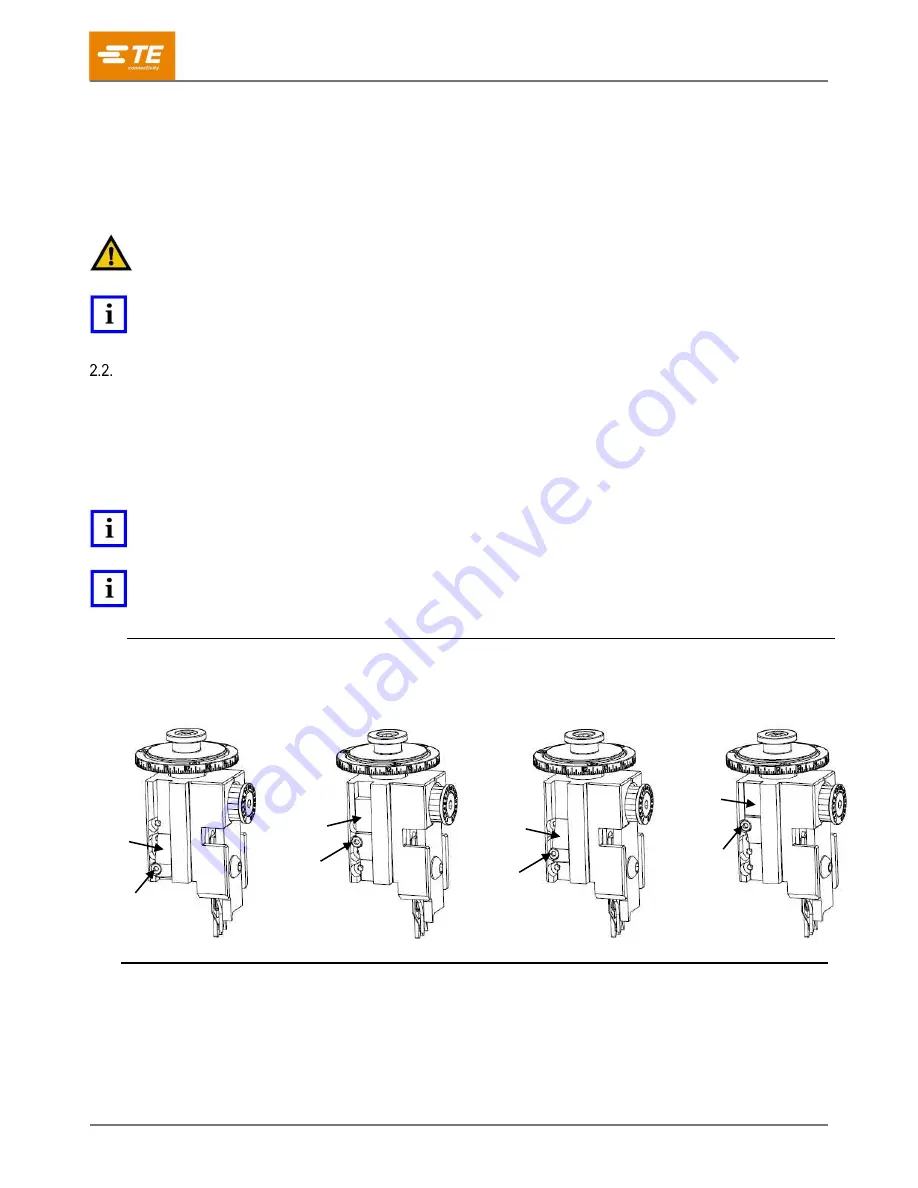
408-35042
Rev C
5
of 26
5. Lubrication
Some terminal strips require the use of a terminal lubricant. Wick-type lubricators apply lubricant to the
terminal strip as it feeds into the applicator. Terminal lubricants reduce tooling wear and help reduce
damage to the plating on some terminals.
OCEAN applicator, Side-Feed Lubricator Assembly PN 2119955-1 is available.
For rear-carrier style terminals, Lubricator Assembly PN 2119955-5 is available.
CAUTION
Depending on the final use of the crimped terminal, terminal lubrication is not always recommended. To determine if your
applications warrant the use of a terminal lubricator, contact your Field Representative.
NOTE
If your application warrants the use of a terminal lubricator, the recommended lubricant is Stoner Mechanical Lubricant E807
available from Stoner, Inc. Call 1-800-227-5538 or visit www.stonersolutions.com.
Applicator with Mechanical Feed System
With a Mechanical Feed applicator, the terminals are fed by the action of the Feed Cam and a series of rods
and levers, which move the Feed Pawl. Two feed cams are available (Pre-Feed and Post Feed) and can be
mounted in two different mounting holes depending on machine stroke length and feed type (see Figure 7).
The
Post-Feed
feed cam advances the lead terminal over the Anvil on the
downward
stroke of the ram
assembly; leaving the Anvil clear when the machine is at rest.
The
Pre-Feed
feed cam advances the lead terminal over the Anvil on the
upward
stroke of the ram assembly;
leaving a terminal over the Anvil when the machine is at rest.
NOTE
When not in use, the spare Feed Cam can be mounted to the applicator housing in the spare feed cam storage location (see
Figure 8).
NOTE
Pacific applicators can only be used with 30-mm stroke machines and, therefore, only have the 30-mm feed cam mounting
positions on the applicator ram.
Figure 7
Mounting Feed Cam (Atlantic Applicator w/Mechanical Feed shown)
40-mm [1
5
/
8
-in.] Stroke Machine
30-mm [1
1
/
8
-in.] Stroke Machine
Pre-
Feed
Pre-
Feed
Post-
Feed
Post-
Feed
Mounting
Screw
(typ)
Mounting
Screw
(typ)
Mounting
Screw
(typ)
Mounting
Screw
(typ)