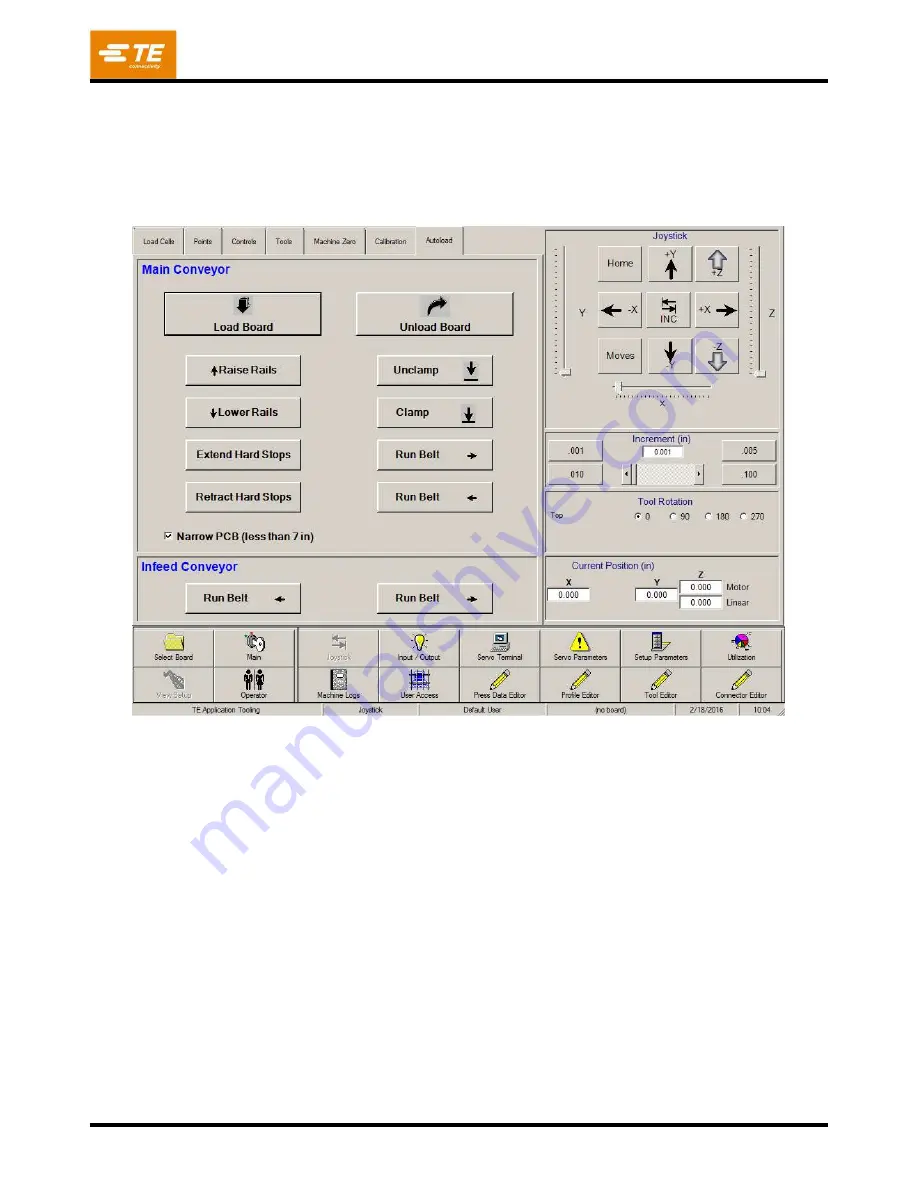
409-32048
Rev A
40
of 64
9. Raise the clamps and conveyor rails and retract the hard stops, then slide the PCB along the rails
from one end to the other while checking for tightness or excessive looseness. Adjust conveyor width
slightly if needed.
10. Extend the hard stops and push the PCB against them. Retract the stops and lower the rails while
observing if the PCB is smoothly guided onto the fixture guide pins. Re-adjust conveyor width and
hard stop position if needed.
Figure 41
8.6.
Autoload Conveyor
–
Maintenance
Features on the CAPI-6T Autoload system that may require periodic visual checks have been listed below. See
Figure 42.
Check Guide Rods, Y axis (PCB width) bearing guide rails, conveyor belts, and all other areas of motion
for foreign matter (dust, dirt, metal shavings, etc.). Wipe or clean as necessary. Use a light general
purpose oil on the bearing guide rails.
Check all air lines for crushing/crimping during motion of the clamps, hard stops and/or main conveyor
rails.
Check for any binding in the up/down motion of the clamps, in/out motion of the hard stops and up/down
motion of the main conveyor rails. If necessary, loosen the mount / attachment screw to the actuators;
check for smooth fixture motion and retighten as necessary.
Check the condition of the conveyor belts for tightness, alignment and physical integrity.
Observe smooth and equal up / down motion of clamps and main conveyor rails. Small in-line pneumatic
flow controls are provided at each of the conveyor lift cylinders
–
see below. Front cylinder controls are
under the sheet metal cover.
“Down” controls are plumbed to the lower
port, “up” controls are plumbed
to the upper port on the air cylinder.
Adjust the flow controls as required to eliminate “slamming” the
PCB and equalize motion speed for all four corners of the conveyor. Four additional flow controls (up &
Joystick Screen
–
Autoload Tab