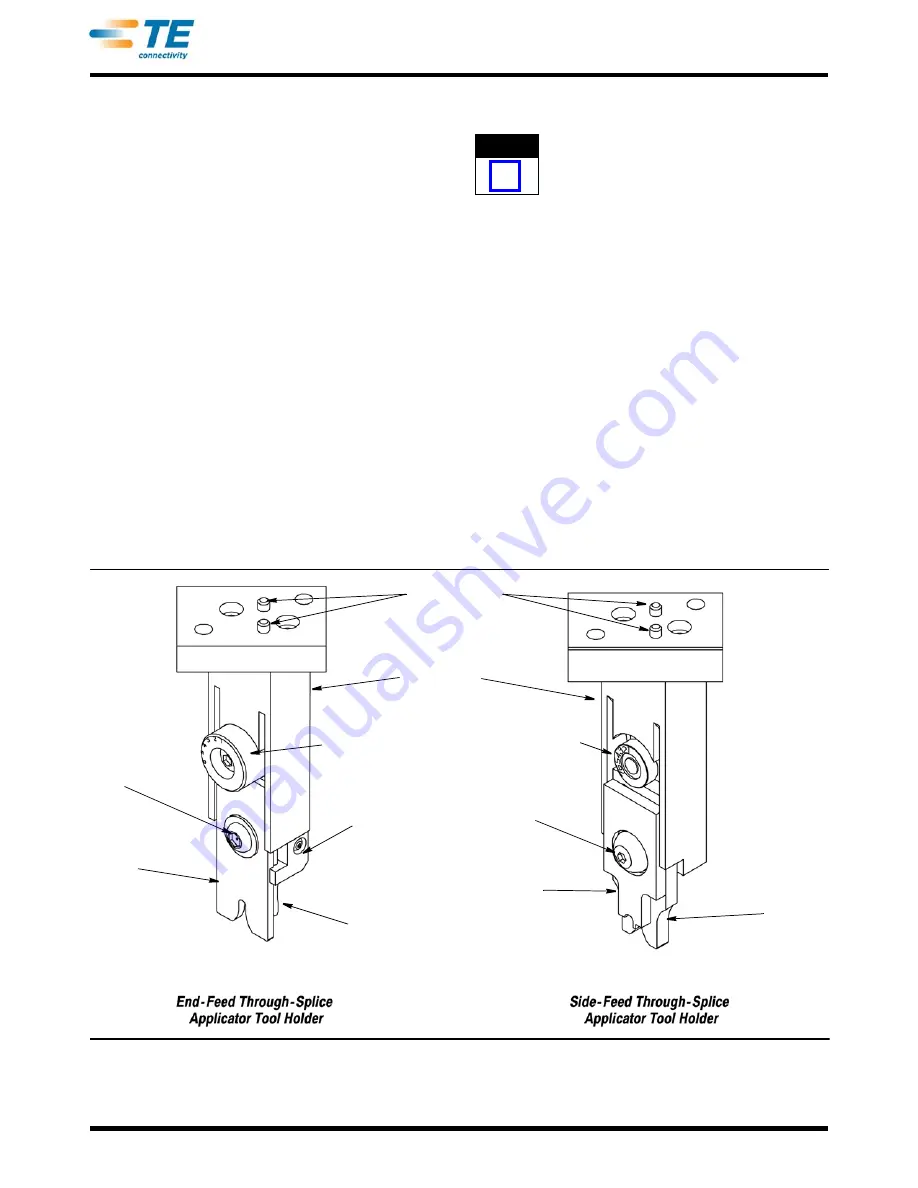
408-32027
3 of 11
Rev A
The front guard has been modified to remove the
guard insert. The front guard works together with the
applicator guarding to protect the operator. The front
guard retains its keyed interlock to actuate the guard
safety switch when closed.
The modified guards on the AMP 5K/40 CE through-
slice terminator will work with side-feed and end-feed
CE through-splice applicators.
2.2. Applicator Description
End-Feed and Side-Feed applicators used with AMP
5K/40 CE through-splice terminators are two-piece
applicators consisting of a tool holder and applicator
base.
The tool holder is secured to the ram of the AMP
5K’/40 Through-Splice Terminating Machine with two
screws. The tool holder contains locating pins
(Figure 4) to facilitate it's location on the terminator
ram. The locating pins allow an easier tooling
changeover.
The wire crimper, insulation crimper, and the front
shear depressor are located in a pocket in the tool
holder, and are secured by a crimper bolt. The front
shear depressor pushes the front floating shear down
to cut the crimped terminal from the strip.
The wire crimp is easily adjusted, providing an array of
different wire crimp sizes.
NOTE
i
All AMP 5K/40 CE Through-Splice Terminators are
equipped with a "precision adjust" feature.
The hold-down bracket (see Figure 4) is attached to
the ram and, with bracket attached, holds the terminal
in place during the crimping and shearing process.
The applicator's mounting surface is its base plate.
The base plate attaches to the base of the terminator.
The anvil, shear tooling and strip guide plates are all
located on the base plate.
Since the upper tooling is permanently located, the
lower tooling can be adjusted to the correct position
and locked (screwed) into place.
End-Feed and Side-Feed Through-Splice Applicators
can withstand the high crimping pressures required to
apply terminals to the larger CMA ranges (up to
approximately 17,000 CMA ). Although these
applicators accept only certain terminals, they provide
valuable application flexibility. The design optimizes
accessibility which aids in more precise wire
placement, and increased production throughout.
Locating Pins
Tool Holder
Crimp Height
Adjustment Wheel
Hold-Down
Bracket
Shear Blade
Crimper
Bolt
Wire
Crimper
Front Shear
Depressor
Crimp Height
Adjustment Wheel
Wire
Crimper
Crimper
Bolt
Figure 4