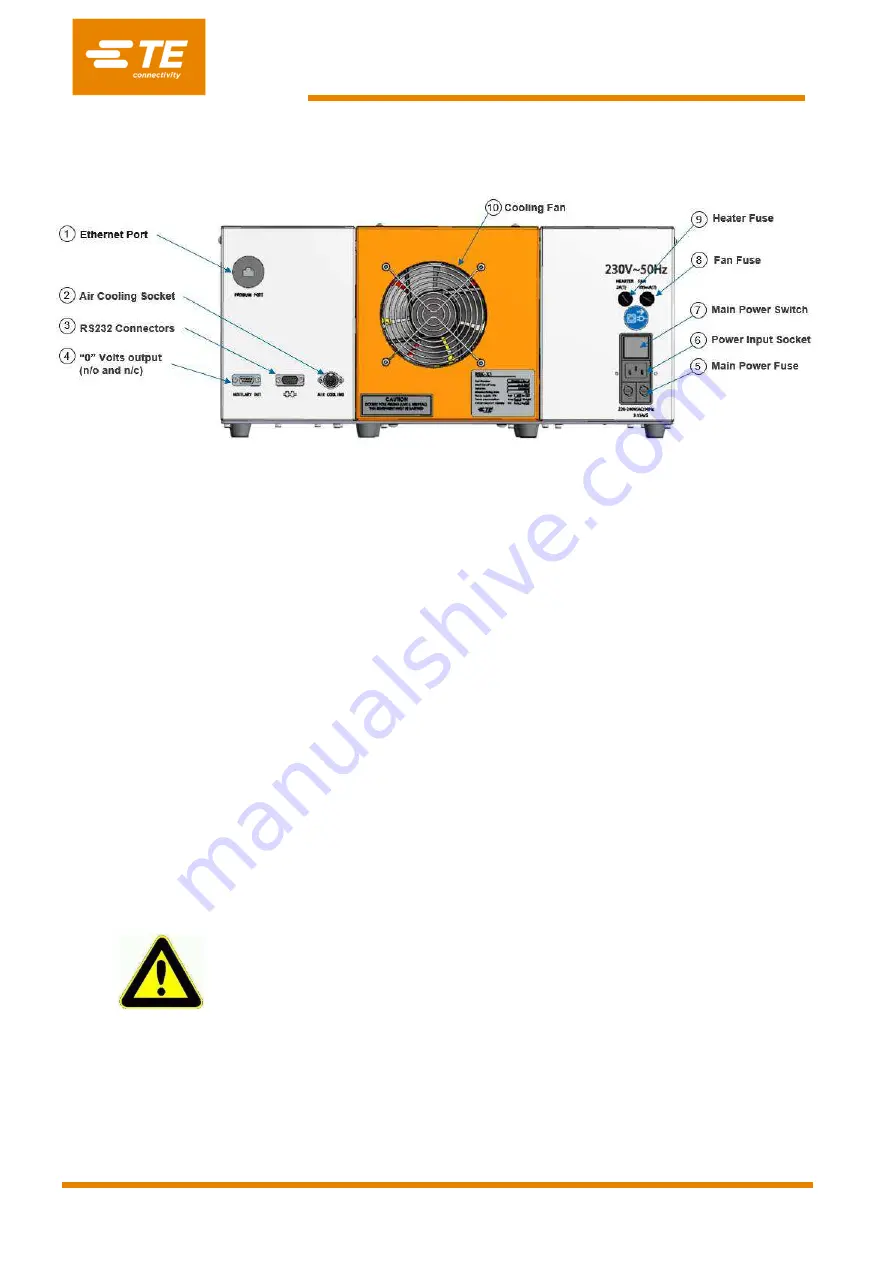
RBK-X1
PN 2234800-1
Page 8 Rev A Sept 2019
1.4 Rear Panel
Fig. 1-4: Rear Panel
1.
Ethernet Port
(Access to upgrade program to PLC and touch screen)
2. Air Cooling Socket
(Connect to air cooling kit 1-529533-7)
3. RS 232 Connector
(Connect to welding machine, like Schunk welding machine.)
4.
“0” Volts output
(n/o and n/c, normally open and normally closed)
5. Main Power Fuse
(2 X 230V, 3.15A anti-surge)
6. Power Input Socket
(230V)
7. Main Power Switch
(Used to turn off power to the RBK-X1, when in stand-by mode)
8. Fan Fuse
(240V, 1A anti-surge)
9. Heater Fuse
(240V DC, 3A anti-surge)
10. Cooling Fan
(Operates above 190
°C heater temperature
)
Do not use the Mains Power Switch or E-stop button as normal process to turn off the
machine, as this will cause a significant reduction to the life of the heater element.
Turn off the Heater using the I/O Switch. The temperature will drop and cooling will
continue, once below 190º C, the fan will turn off and the machine will enter the
stand-by mode. The power can now be switched off using the Main Power Switch.