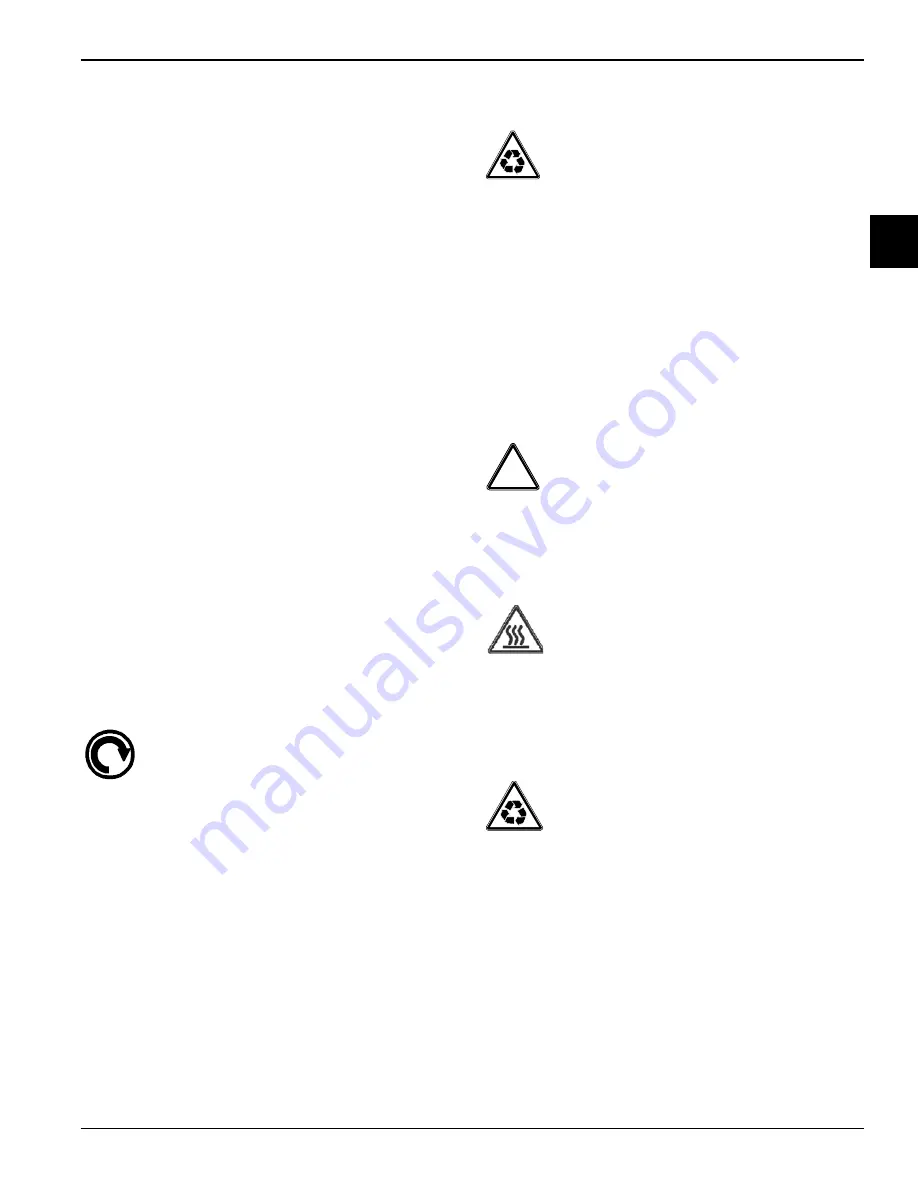
TO THE INSTALLER
1-3
Model 490
To the Installer
1
with a power cord and a plug or another device
to disconnect the machines from the power
source must have an all-pole disconnecting
device with a contact gap of at least 0.125 in.
(3 mm) installed in the external installation.
•
Machines that are permanently connected to
fixed wiring and for which leakage currents may
exceed 10 mA, particularly when disconnected
or not used for long periods, or during initial
installation, shall have protective devices to
protect against the leakage of current, such as a
GFI, installed by the authorized personnel to the
local codes.
•
Supply cords used with this machine shall be
oil-resistant, sheathed flexible cable not lighter
than ordinary polychloroprene or other
equivalent synthetic elastomer-sheathed cord
(code designation 60245 IEC 57) installed with
the proper cord anchorage to relieve conductors
from strain, including twisting, at the terminals
and protect the insulation of the conductors from
abrasion.
If the supply cord is damaged, it must be replaced by an
authorized Taylor service technician in order to avoid a
hazard. Secure the supply cord ground lead to the
machine in a location where if the cord is pulled, the main
power leads will become taut before the ground lead can
break loose.
Beater Rotation
NOTICE!
Beater rotation must be clockwise as
viewed looking into the freezing cylinder.
To correct the rotation on a three-phase machine,
interchange any two incoming power supply lines at the
machine main terminal block only. To correct rotation on
a single-phase machine, exchange leads inside the
beater motor. (Follow the diagram printed on the motor.)
Electrical connections are made directly to the terminal
block provided in the main control box located behind the
service panel.
It is recommended that beater rotation adjustment be
performed by an authorized Taylor service technician.
Refrigerant
CAUTION!
This equipment contains
fluorinated greenhouse gases (F-Gas) to provide
refrigeration using a hermetically sealed circuit or within
foam insulation. This unit's type of gas, quantity, Global
Warming Potential (GWP) and CO
2
tonnes equivalent
information is recorded on the unit's data label. The
refrigerant used is generally considered non-toxic and
non-flammable. However any gas under pressure is
potentially hazardous and must be handled with caution.
NEVER
fill any refrigerant cylinder completely with liquid.
Filling the cylinder to approximately 80% will allow for
normal expansion.
CAUTION!
Use only approved refrigerant
listed on the machine's data label or authorized through a
manufacturer's technical bulletin. The use of any other
refrigerant may expose users and operators to
unexpected safety hazards.
WARNING!
Refrigerant liquid sprayed onto the
skin may cause serious damage to tissue. Keep eyes
and skin protected. If refrigerant burns should occur,
flush the area immediately with cold water. If burns are
severe, apply ice packs and contact a physician
immediately.
NOTICE!
Taylor reminds technicians to be
aware of and in compliance with local government laws
regarding refrigerant recovery, recycling, and reclaiming
systems. For information regarding applicable local laws,
please contact your local authorized Taylor distributor.
!
Summary of Contents for 490
Page 16: ...4 4 OPERATOR PARTS IDENTIFICATION Model 490 Operator Parts Identification 4 Notes...
Page 18: ...5 2 USER INTERFACE Model 490 User Interface 5 Notes...
Page 32: ...9 2 PARTS REPLACEMENT SCHEDULE Model 490 Parts Replacement Schedule 9 Notes...
Page 38: ...11 4 LIMITED WARRANTY ON PARTS Model 490 Limited Warranty on Parts 11 Notes...