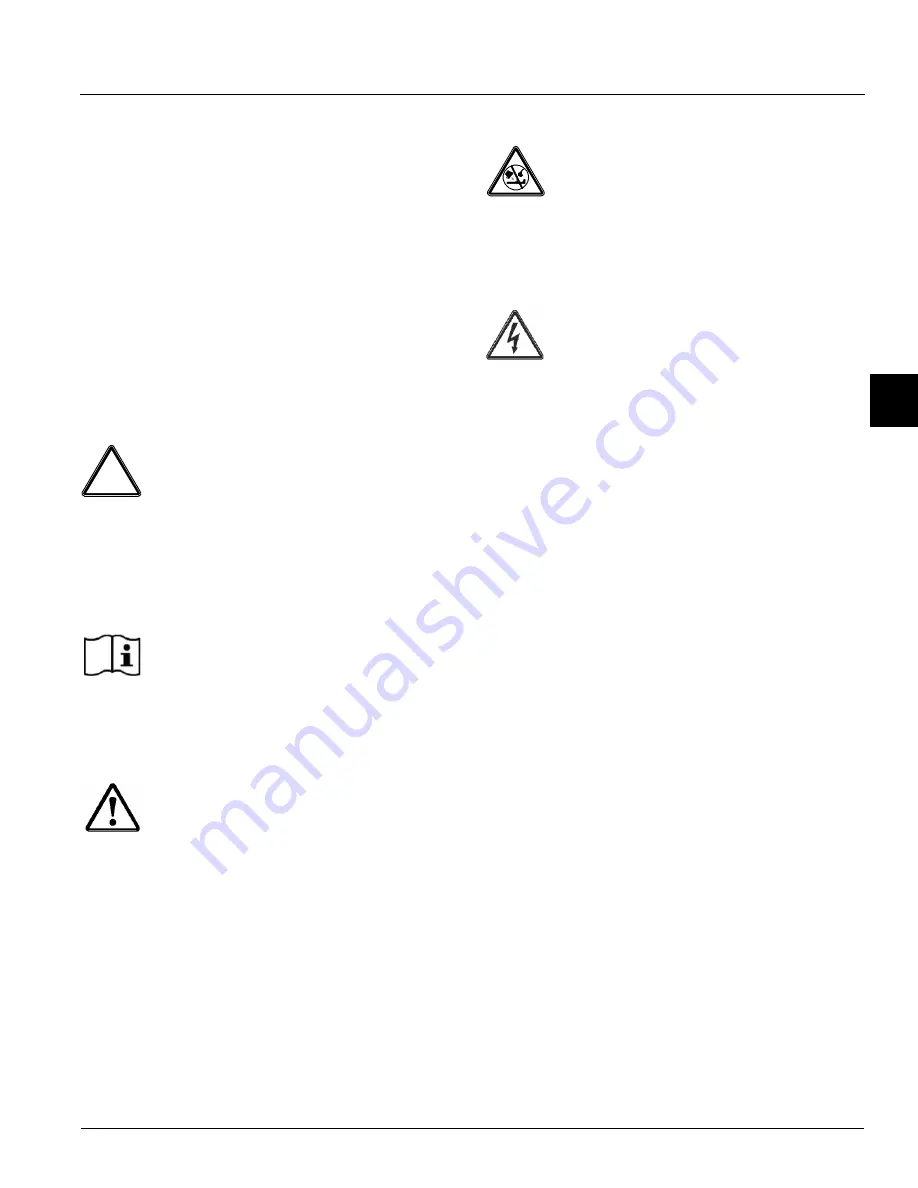
Section 3
3-1
Model 104
Safety
3
Safety
We at Taylor Company are concerned about the safety of
the operator at all times when they are coming in contact
with the machine and its parts. Taylor makes every effort
to design and manufacture built-in safety features to
protect both operators and service technicians.
Installing and servicing refrigeration equipment can be
hazardous due to system pressure and electrical
components. Only trained and qualified service
personnel should install, repair, or service refrigeration
equipment. When working on refrigeration equipment,
observe precautions noted in the literature, tags, and
labels attached to the machine, and other safety
precautions that may apply. Follow all safety code
requirements. Wear safety glasses and work gloves.
DANGER!
Failure to adhere to the following
safety precautions may result in severe personal injury or
death. Failure to comply with these warnings may also
damage the machine and/or its components. Such
damage may result in component replacement and
service repair expenses
.
NOTICE! DO NOT
operate this machine
without reading this entire manual first. Failure to follow
all of these operating instructions may result in damage
to the machine, poor performance, health hazards, or
personal injury.
IMPORTANT!
This machine is to be used only
by trained personnel. It is not intended for use, cleaning,
or maintenance by children or people with reduced
physical, sensory, or mental capabilities or lack of
experience and knowledge. Where limited machine
operation is allowed for public use, such as a self-serve
application, supervision or instruction concerning the use
of the machine by a person responsible for their safety is
required. Children should be supervised to ensure that
they do not play with the machine.
WARNING!
This machine must
NOT
be
installed in an area where a water jet or hose can be
used.
NEVER
use a water jet or hose to rinse or clean
the machine. Failure to follow this instruction may result
in electrocution.
WARNING!
Avoid injury.
•
DO NOT
operate the machine unless it is
properly grounded.
•
DO NOT
operate the machine with fuses larger
than specified on the machine's data label.
•
All repairs should be performed by a Taylor
service technician.
•
The main power supplies to the machine must
be disconnected prior to performing installation,
repairs, or maintenance.
•
For Cord-Connected Machines:
Only Taylor
service technicians or licensed electricians may
install a plug or replacement cord on the
machine.
•
Machines that are permanently connected to
fixed wiring and for which leakage currents may
exceed 10 mA, particularly when disconnected
or not used for long periods, or during initial
installation, shall have protective devices to
protect against the leakage of current, such as a
GFI, installed by the authorized personnel to the
local codes.
•
Stationary machines which are not equipped
with a power cord and a plug or another device
to disconnect the machine from the power
source must have an all-pole disconnecting
device with a contact gap of at least 0.125 in.
(3 mm) installed in the external installation.
•
Supply cords used with this machine shall be
oil-resistant, sheathed flexible cable not lighter
than ordinary polychloroprene or other
equivalent synthetic elastomer-sheathed cord
(code designation 60245 IEC 57) installed with
!
Summary of Contents for 104
Page 8: ...1 4 TO THE INSTALLER Model 104 To the Installer 1 Notes...
Page 14: ...3 4 SAFETY Model 104 Safety 3 Notes...
Page 18: ...4 4 PARTS Model 104 Parts 4 Notes...
Page 30: ...7 2 OPERATOR CHECKLIST Model 104 Operator Checklist 7 Notes...
Page 32: ...8 2 TROUBLESHOOTING Model 104 Troubleshooting 8 Notes...
Page 34: ...9 2 PARTS REPLACEMENT SCHEDULE Model 104 Parts Replacement Schedule 9 Notes...
Page 40: ...11 4 LIMITED WARRANTY ON PARTS Model 104 Limited Warranty on Parts 11 Notes...