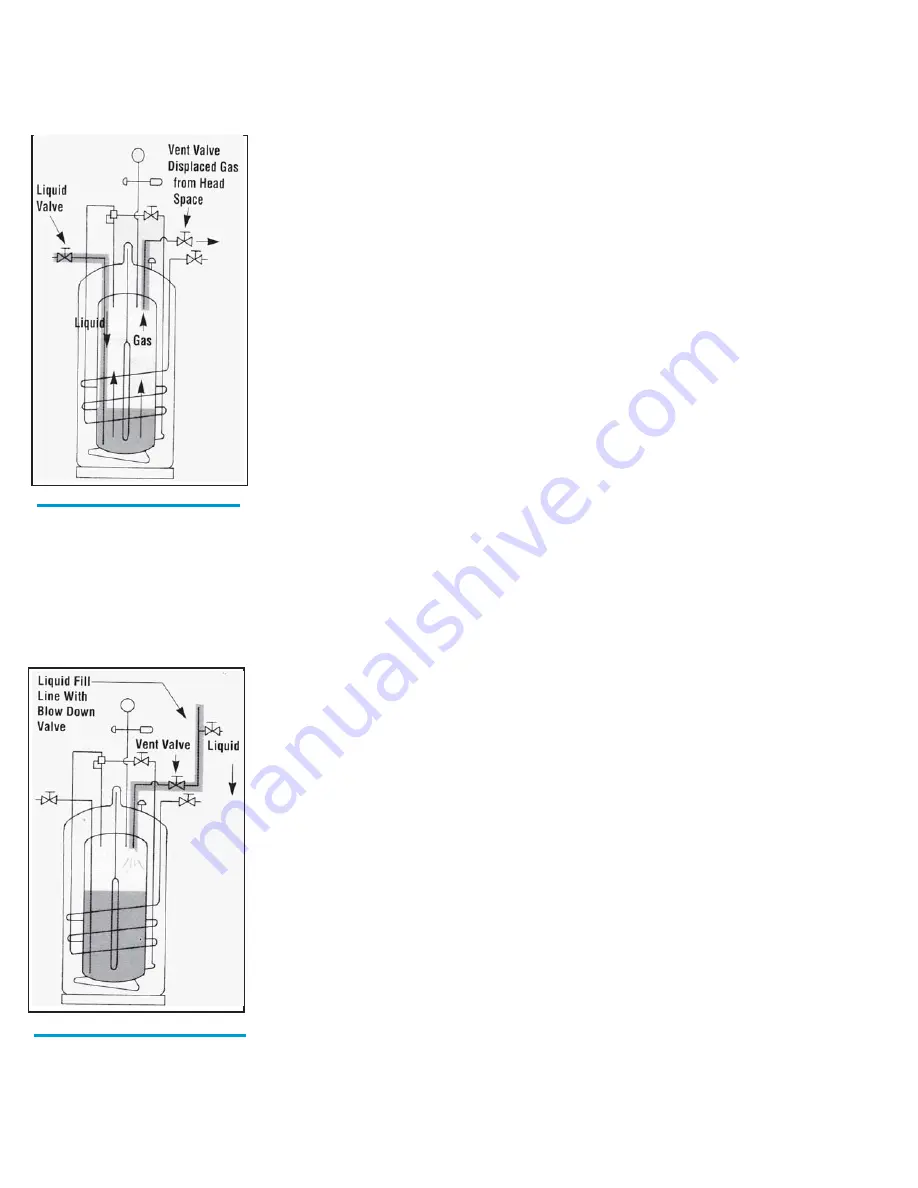
2. During the fill, monitor the container pressure and maintain a pressure of 10-15 psig
(0.7-1 bar/69-103 kPa) by throtting the VENT valve.
3. When the full weight is reached, close both the LIQUID and VENT valves.
4. Close the liquid supply valve and open the dump valve on the fill line assembly.
5. Disconnect the fill line from the container and remove the container from the scale.
Pump Transfer Filling Method
When a pump is used for filling liquid containers, the fill may be accomplished through
either the VENT valve or the LIQUID valve. Filling through the VENT valve recondenses
gas in the area over the liquid in the cylinder and reduces product loss during the fill. This
method will also result in liquid near the saturation temperature of the supply vessel.
Filling through the LIQUID valve may provide colder liquid and longer holding time before
the liquid warms to the point where venting beings, but will require more frequent venting
and greater product loss.
Pump Transfer Filling Procedure -
This method applies only to containers in gas
service that are equipped with a 230 psig (16 bar/ 1586 kPa) relief valve. Liquid is admitted
through the VENT valve and recondenses gas in the head space during the fill. The fill line
is connected from the liquid supply to the VENT valve on the cylinder. Both the fill line and
the container should be pre-cooled prior to beginning the fill process. Proper full weight is
determined by the previously explained method.
1. Open the supply valve. Then, on the container being filled, open only the VENT valve to
begin the fill. Start the pump at this time.
2. Observe the container pressure closely. If the pressure approaches the relief valve
setting (or the dump pressure rating) stop the fill process at the supply and open the fill
line dump valve to vent excess pressure. As soon as the pressure has dropped to a
level that will allow you to resume the fill, close the dump valve and restart the pump (or
reopen the supply valve.)
3. When full weight is reached, close the VENT valve. Stop pump (where applicable),
close liquid supply valve and open the dump valve on fill line assembly to vent trapped
liquid.
4. Disconnect the fill line from the container and remove the container from the scale.
Fill Hose Kits
Taylor-Wharton fill hose kits for the XL-45/50/55 are designed to transfer specific liquefied
gases to, or from, the containers. These accessories are comprised of a Fill Tee Assem-
bly and a Fill Hose. Cryogenic transfer hoses are constructed of stainless steel for the
transfer of cryogenic liquids and are available in four or six feet (1.2 or 1.8 m) lengths with
a 3/8 in. NPT fitting on one end and CGA service-specific female fitting on the other. A Fill
Tee Assembly consists of a cross fitting with a CGA end fitting, relief valve and manual
dump valve.
In use, the CGA Tailpiece couples to the fill connection on the container being filled. The
Relief Valve vents pressure over 350 psig (24 bar/2413 kPa) that builds up in the fill line
due to trapped liquid. The Dump Valve is used to allow the operator to blow-down the
receiving container during a pump fill, or to relieve residual pressure from expanding liquid
trapped in the line before disconnecting the fill line.
Pressure Transfer
Filling From a Low
Pressure Source
Pump Transfer Liquid
Fill Through Vent
Valve