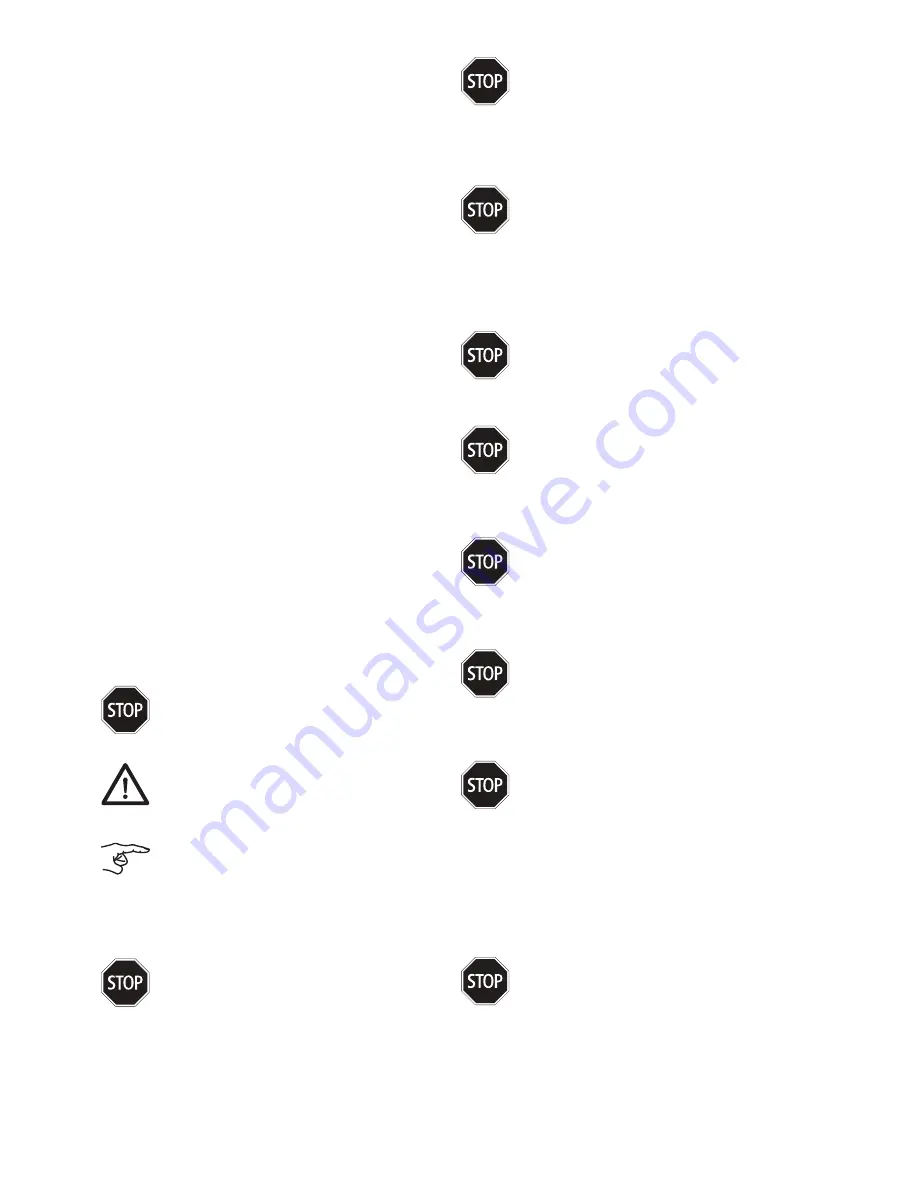
3
5.2. Operator
A operator refers to a user of this equipment who is properly
trained in the use, maintenance, and troubleshooting of this
robotic floor scrubber system. The operator is responsible
for ensuring that maintenance is performed only by trained
maintenance personnel.
5.3. Maintenance Personnel
Maintenance personnel must be properly trained to maintain
this robotic floor cleaning equipment. Maintenance includes
replacement of consumables such as water, detergent,
filters, scrubbing pads, and scheduled cleaning of the
machine.
5.4. Service Technician
A service technician refers to a field engineer who is properly
trained in the use, maintenance, troubleshooting, and service
of this robotic floor scrubber system. A service technician
must have factory service training.
The service technician is responsible for all repairs,
upgrades, and accessory installations requested by
the customer or mandated by TASKI Intellibot. Service
technicians are equipped with proper tools and parts for the
installation, maintenance, and service of this robotic floor
scrubber system.
6. General Safety Awareness
The following section includes important information required
for safe operation of this robotic floor scrubber system.
6.1. User Manual Safety Symbols
The following symbols are used to identify important safety
information:
Warning:
Failure to follow this information could result
in serious harm to people and/or property.
Caution:
Failure to follow this information could result
in damage to the machine and/or property.
Note:
Failure to follow this information could result
in malfunction or damage to the machine.
6.2. General Safety Instructions
The following symbols are used to identify important safety
information:
This machine may only be used by a trained
operator that is physically and mentally
capable of maintaining control and safety of
the machine. Physical or mental impairment
of the user may result in serious injury to
people, property, and/or the machine.
In case of damage to safety relevant
components such as the Emergency Stop
switch, safety interlock, safety touch shields,
front door, batter, etc., the machine must be
stopped immediately. Repair or replacement
of the damaged component by a qualified
service.
Unauthorized use or modification of this
machine may result in unsafe operating
conditions, personal injury, property damage
or machine malfunction. Any unauthorized
modification or use contrary to the intended
purpose will result in voiding the machine
warranty, CE marking, and applicable safety
marks.
Do not use this machine around any
explosive or flammable materials or in
any areas where vapors from flammable
materials such as solvents, fuel, oil or dust
could ignite.
Do not use this machine to vacuum
flammable, toxic, caustic, or irritating
substances. The machine is not designed
for this use and serious injury to persons
and damage to property and the machine
may result.
Do not use this machine in areas with
high electromagnetic fields (EMF). This
machine uses electronics susceptible
to electromagnetic fields. Use of this
equipment in high EMF areas may result in
unintended and uncontrolled operation.
Stairways and doorways must be blocked
when the scrubber is used in robotic mode.
Failure to block a stairway could result in the
machine tumbling down the stairs, resulting
in serious property damage, machine
damage and injury.
Operators must take note of the
surrounding area and be ready to stop the
machine in case a hazardous situation. The
machine must be stopped if any potentially
hazardous situation arises, such as children
entering the cleaning area, objects falling
in the machine path, stairway blocks are
moved, etc. Children should never be
allowed to play in or around the cleaning
area while the robotic floor scrubber system
is in operation.
Never use the robotic floor scrubber system
to transport people or materials. Serious
injury and property damage may result.