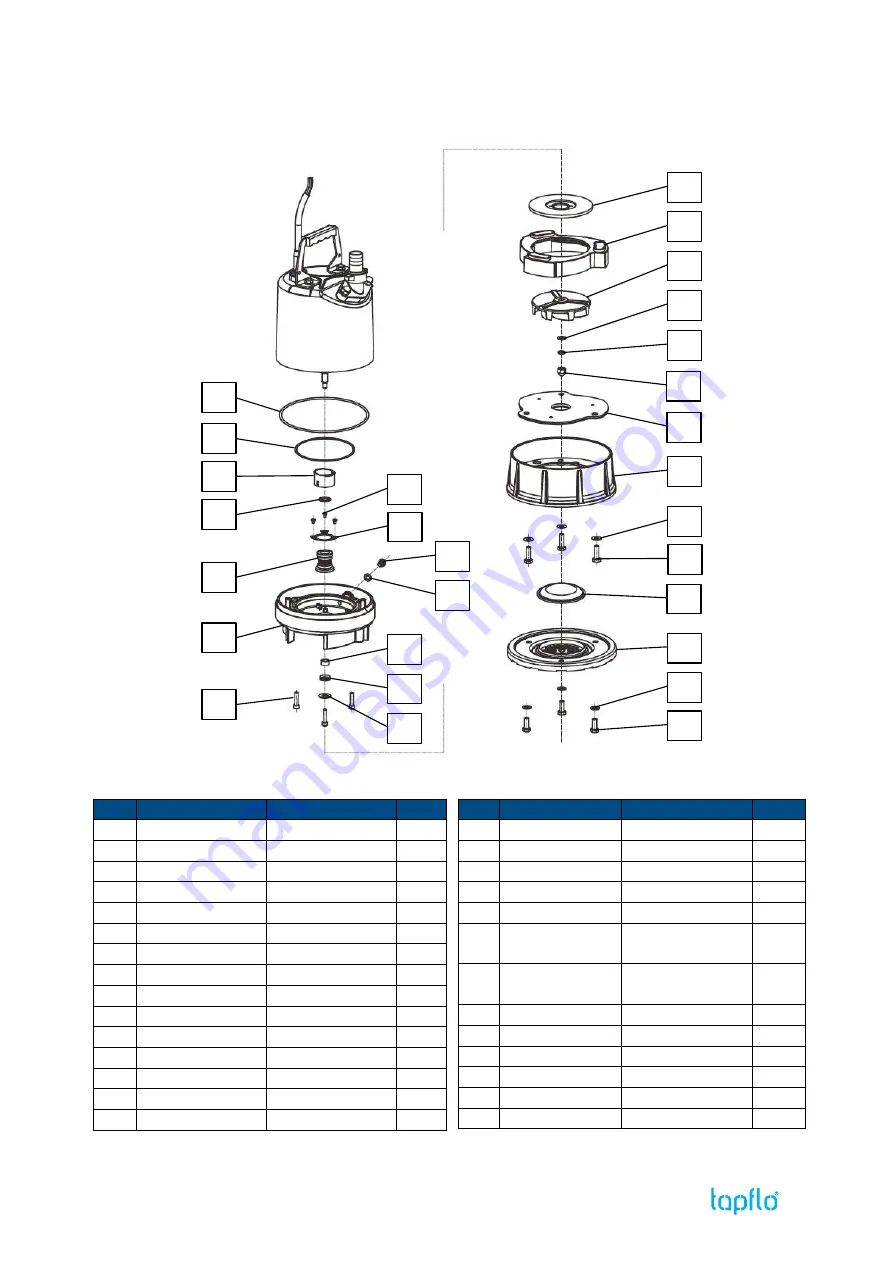
5. Maintenance and inspection
IOM manual
–
SG series
25
5.5.2.
Exploded view
5.5.3.
Parts list
No. Part name
Material
Q-ty
1
Bolt
AISI 304
3
2
Washer
AISI 304
3
3
Bottom plate
NBR & steel
1
4
Check valve
NBR & steel
1
5
Bolt
AISI 304
3
6
Washer
AISI 304
3
7
Stand
Aluminium
1
8
Suction cover
NBR & steel
1
9
Doomed nut
AISI 304
1
10 Spring washer
AISI 304
1
11 Washer
AISI 304
1
12 Impeller
Cast iron
1
13 Oil casing
NBR
1
14 Rear wear plate
NBR & steel
1
15 Washer
AISI 304
1
No. Part name
Material
Q-ty
16 Sand guard
NBR
1
17 Shaft sleeve
AISI 201
1
18 Screw
AISI 304
3
19 Back casing
Aluminium
1
20 Screw
-
3
21
Mechanical seal
fixing plate
Steel
1
22 Mechanical seal
Ceramic-Sic/
Carbon-Ceramic
1
23 Washer
AISI 304
1
24 Oil riser
LDPE
1
25 O-ring
NBR
1
26 O-ring
NBR
1
27 Screw
AISI 304
3
28 O-ring
NBR
1
2
15
17
16
20
3
21
22
23
24
25
26
27
28
1
4
5
6
7
8
9
10
11
12
13
14
18
19