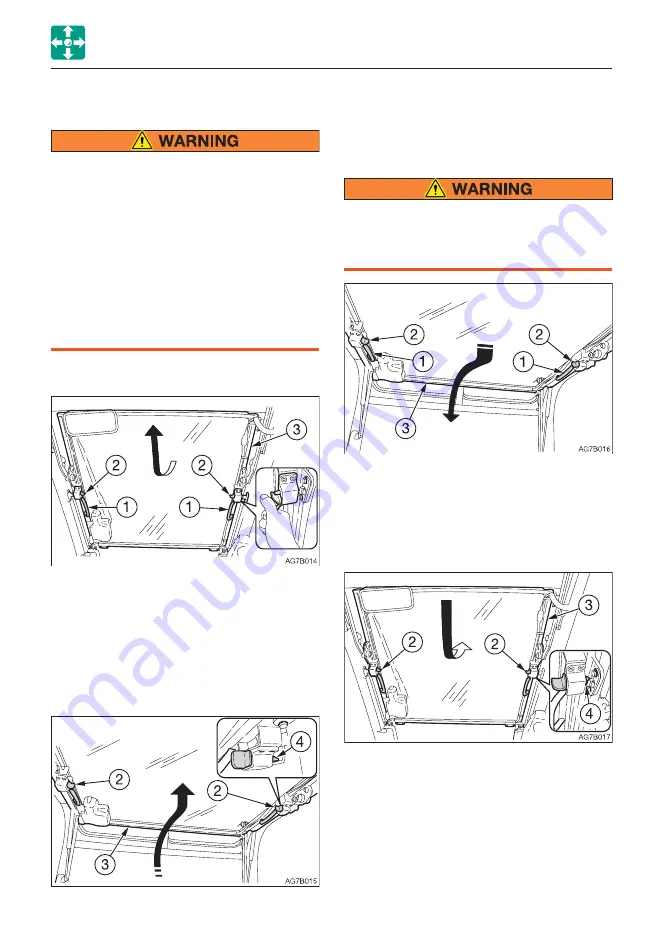
2-11
CONTROLS
FRONT WINDOW
• Grasp the handles firmly with both
hands when opening and closing the
front window. Your head or hands may
get caught if it slips from your hands.
• When the front window is opened or
closed, it will come close to the head.
Be careful that the window does not
strike the head.
• When you open the front window, be
sure to lock it in place with the lock pins
on the left and right sides. The window
may fall if it is not locked in place.
Opening
CAB
1. Park on a level surface and stop the engine.
2. Set the safety lock lever to the locked
position.
3. Grasp the left and right handles (1) and
press the knobs (2) with your thumb to
release the lock.
4. Pull the front window (3) toward you and
lift while doing so.
5. Release your thumb from the knobs (2)
and then lift the front window (3) fully and
lock the front window with lock pin (4).
Closing
When closing the front window slowly so
as not to hit your head. Lowering the
window abruptly may result injury or
damage the front window.
1. Grasp the left and right handles (1) and
press the knobs (2) with your thumb to
release the lock.
2. Pull down the front window (3) and while
doing so, slide it to the front and slowly
lower it.
3. Release your thumb from the knobs (2)
and then press the front window toward
front and lock the front window with lock
pin (4).
Summary of Contents for TB260
Page 1: ......
Page 11: ...1 1 SAFETY...
Page 46: ...1 36 SAFETY SAFETY SIGNS DECALS Applicable machine models 126100003 or later...
Page 47: ...1 37 SAFETY SAFETY SIGNS DECALS...
Page 48: ...1 38 SAFETY SAFETY SIGNS DECALS...
Page 49: ...1 39 SAFETY SAFETY SIGNS DECALS...
Page 50: ...1 40...
Page 51: ...2 1 CONTROLS...
Page 111: ...2 61 MEMO...
Page 121: ...2 71 MEMO...
Page 135: ...3 1 OPERATION...
Page 163: ...4 1 TRANSPORT...
Page 167: ...4 5 TRANSPORT HOISTING THE MACHINE...
Page 169: ...5 1 MAINTENANCE...
Page 236: ...5 68...
Page 237: ...6 1 TROUBLESHOOTING...
Page 245: ...6 9 MEMO...
Page 264: ...6 28...
Page 265: ...7 1 SPECIFICATIONS...
Page 268: ...7 4 SPECIFICATIONS MACHINE DIMENSIONS MACHINE DIMENSIONS...
Page 270: ...7 6 SPECIFICATIONS OPERATING RANGES OPERATING RANGES...
Page 272: ...7 8 MEMO...
Page 286: ...7 22...
Page 287: ...8 1 OPTIONS OPTIONS...