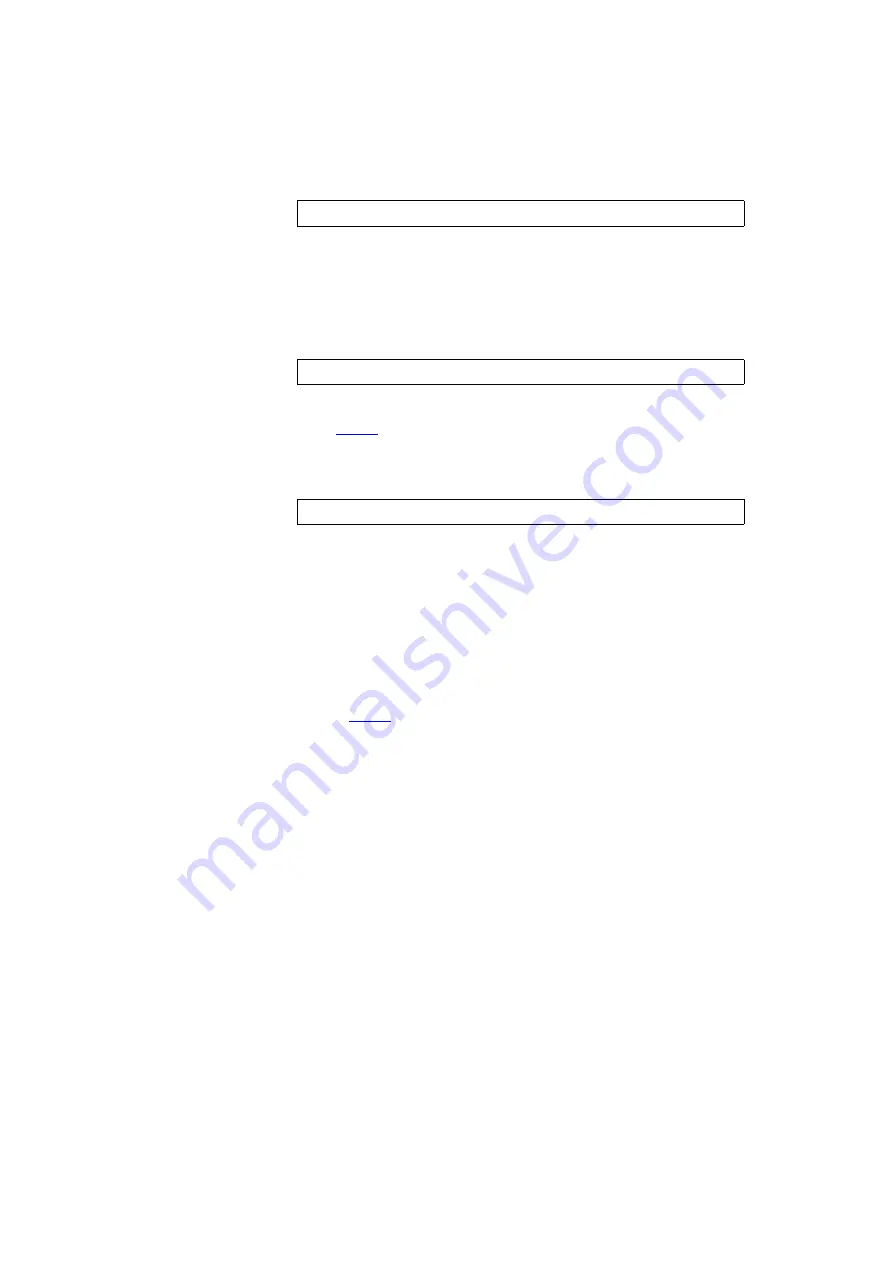
282
Transmitter Fault Finding (50W/40W)
TB7100 Service Manual
© Tait Electronics Limited
October 2005
Task 2 —
Check Switch Circuit
If the power supply to the drains of the PAs and PA driver is not correct, the
switch circuit is suspect. Check the circuit as follows:
1.
Measure the voltage at the point 1 on R350 shown in
(B1 band) or
(H5, H7 bands). The voltage should be:
2.
If the voltage measured in
is correct, go to
. If it is not,
check for continuity between R350 and the power connector. Repair
any fault and conclude with
.
3.
Measure the voltage at R339 as shown in
(B1 band) or
(H5, H7 bands). The voltage should be:
4.
If the voltage measured in
is correct, go to
. If it is not,
and check the 9 V power supply.
5.
Measure the voltage at the point 2 on R350 shown in
(B1 band) or
(H5, H7 bands). The voltage should be:
6.
If the voltage measured in
is correct, go to
. If it is not,
replace Q308 — see
(B1 band) or
(H5,
7.
Remove the heat-transfer block from the main board. Replace Q311
(situated on the bottom-side of the main board next to the power
connector). Replace the heat-transfer block, and conclude with
8.
Repeat
to confirm the removal of the fault, and go to
. If the repair failed or the fault could not be
found, replace the main-board assembly and go to
point 1 on R350: 13.8V DC
R339: 9V DC
point 2 on R350: < 5V DC
Summary of Contents for TB7100
Page 1: ...TB7100 base station Service Manual MBB 00005 01 Issue 1 October 2005...
Page 18: ...18 Mechanical Design TB7100 Service Manual Tait Electronics Limited October 2005...
Page 38: ...38 Functional Description TB7100 Service Manual Tait Electronics Limited October 2005...
Page 62: ...62 Circuit Descriptions TB7100 Service Manual Tait Electronics Limited October 2005...
Page 124: ...126 Servicing Procedures TB7100 Service Manual Tait Electronics Limited October 2005...
Page 140: ...142 Interface Fault Finding TB7100 Service Manual Tait Electronics Limited October 2005...
Page 216: ...218 Receiver Fault Finding TB7100 Service Manual Tait Electronics Limited October 2005...
Page 366: ...368 CODEC and Audio Fault Finding TB7100 Service Manual Tait Electronics Limited October 2005...