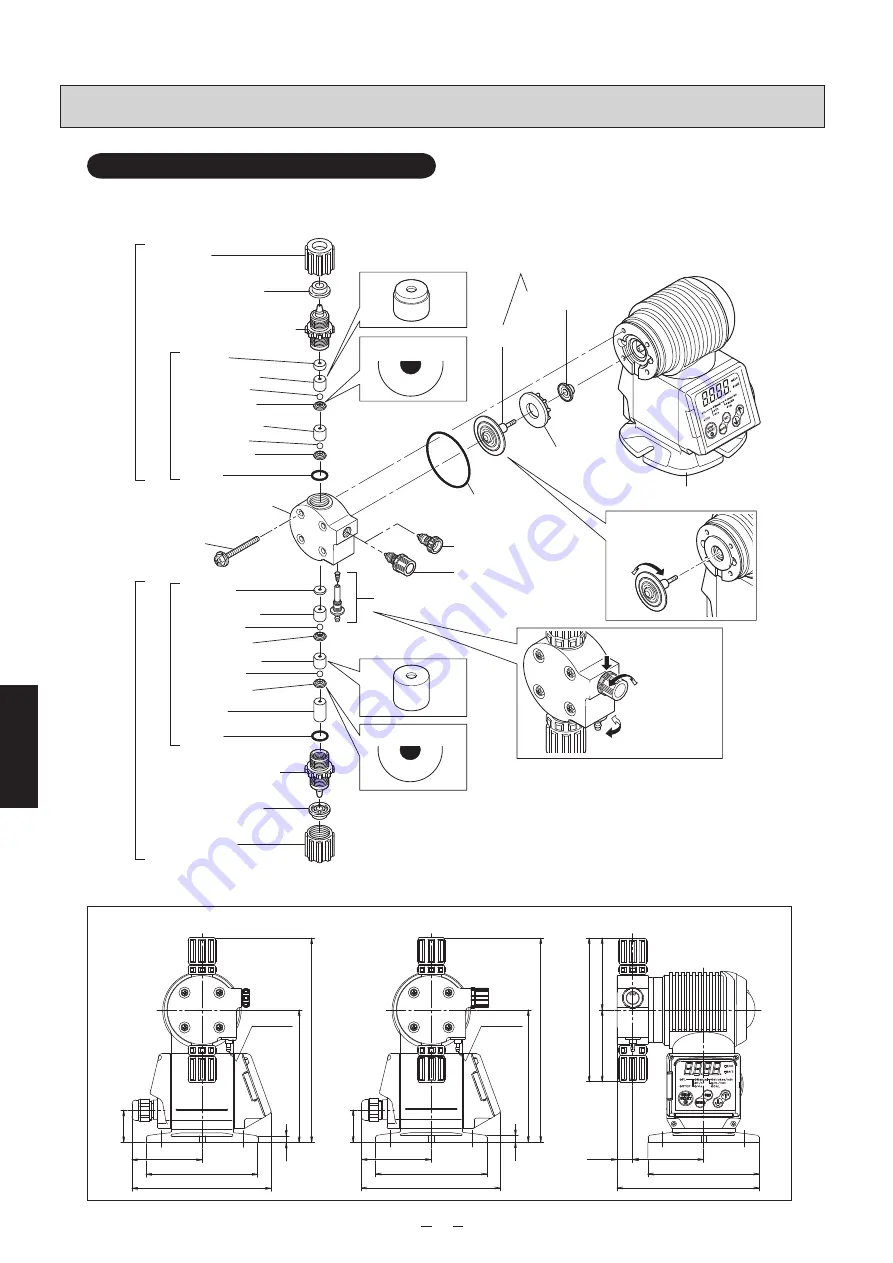
43
Maintenance
Exploded views of liquid-end parts and external dimension
■
Exploded views of liquid-end parts
■
External dimension
Model w/o relief-valve function
Model w/ relief-valve function
118
(150.5)
16.5
75
(147)
74
7
34
152
(216
)
76
76
140
Air-release port
118
(147)
74
7
34
(216
)
140
Air-release port
118
Pump head
Head bolt (cross-recessed
head hexagon bolts)
Packing
O-ring
Spacer
Ball stopper*
3
Check ball
Valve seat*
4
Valve seat*
4
Ball stopper*
3
Check ball
Relief valve
*
Air-release knob
*
Air-release nozzle assembly
*
Discharge-side joint assembly
Suction-side joint assembly
Valve seat assembly
*
Valve seat assembly
*
Nut
Retaining ring
Discharge-side joint
Spacer
O-ring
Ball stopper*
1
Check ball
Valve seat*
2
Ball stopper*
1
Check ball
Valve seat*
2
Suction-side joint
Retaining ring
Hose nut
Turn this way
to loosen.
Turn this way
to tighten.
Turn this way
to tighten.
Turn the retaining nut
(the part indicated by the arrow)
to remove and install the relief valve.
Turn this way
to tighten.
·
*
Consumables that must be replaced at periodic intervals. For
further details, refer to the “Consumables” on page 59 to 60
· Also have ready the pump head set consisting of the top and bottom
joint set and pump head.
Auxiliary ring
Body
O-ring
(S60)
*
Diaphragm
Protective diaphragm
Diaphragm assembly
*
*1
*2
*3
*4
Turn this way
to loosen.
Turn this way
to loosen.
Back : Engraved mark “CL”
Back : No engraved mark
CL
Series: CLPW/CLPWM/CLPWT Model: 30R/30/60R/60/100R/100 Liquid-end material: ATCF
For injection of sodium hypochlorite type
33-66(白)̲EM-127̲PW(E).indd 43
2014/11/17 11:56:44
Summary of Contents for CLPW Series
Page 67: ......
Page 68: ...EM 127 8 03 2014 11 DDD ...