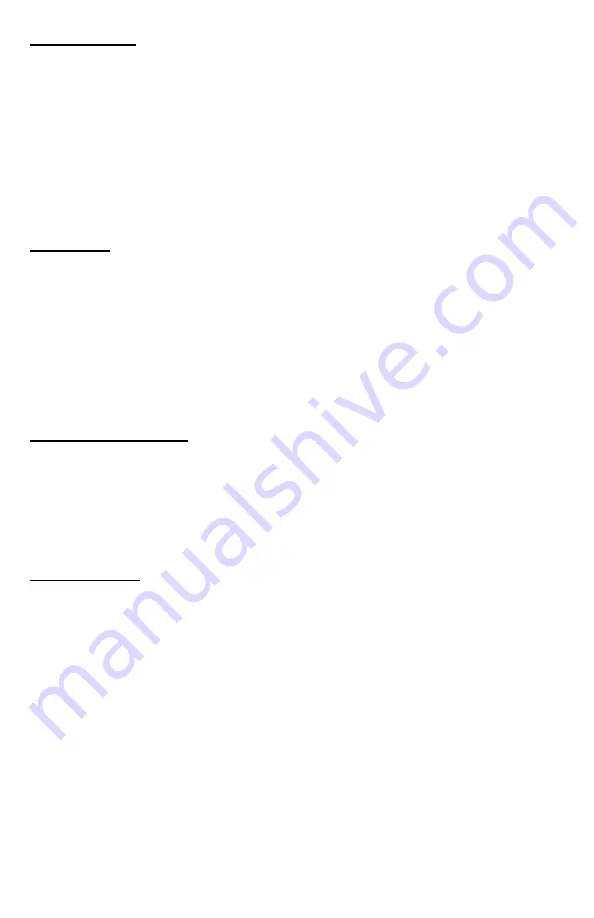
-
7 -
6/07 A1
PROGRAMMING
1. Rotate the MODE SELECT switch to the parameter to be programmed. SymCom recommends
that LV be programmed first and then move clockwise through the positions to complete the
process.
2. Press and hold the RESET/PROGRAM button.
3. Rotate the DISPLAY/PROGRAM knob until the proper setting for the parameter that is being
programmed is displayed.
4. Release the RESET/PROGRAM button. This stores the new parameter in the nonvolatile
memory. If the number changes back to what is was before programming, then the tamper guard
is on and will need to be unlocked before programming can be completed (see the TAMPER
GUARD section for a complete description).
5. Continue steps 1-4 until all parameters are programmed.
OPERATION
The relay operation of the Model 777-P is designed to be fail safe. This means when everything is
within the limits programmed into the unit, the relay will energize, the NO contact will close and the
NC contact will open. Once the unit has been wired and programmed, the unit is ready to operate.
Turn MODE SELECT to the RUN position. The display will show “run” alternating with some number
(the numbers displayed will be the number corresponding to where the DISPLAY/PROGRAM knob
is pointed). It will do this for the amount of time programmed into RD1. After this time has expired,
the relay will energize (NO contact will close and the NC contact will open). If something else is in
the display, see the troubleshooting section for more information. If MODE SELECT is taken out of
the RUN position, the unit’s relay will de-energize.
CLEARING LAST FAULT
The last fault stored can be cleared on the MotorSaver
®
Plus following these steps:
1. Rotate the MODE SELECT switch to GF.
2. Press and hold the RESET/PROGRAM button. Adjust the DISPLAY/PROGRAM adjustment until
“cLr” appears on the display. Release the RESET/PROGRAM button.
To verify the last fault was cleared, place the MODE SELECT switch in the RUN position. Then
press and hold the RESET/PROGRAM button; “cLr” should be on the display.
TAMPER GUARD
The MotorSaver’s setpoints can be locked to protect against unauthorized program changes.
1. Rotate the MODE SELECT switch to GF.
2. Press and hold the RESET button. Adjust the DISPLAY/PROGRAM knob until “Loc” appears on
the display.
3. Release the RESET button.
4. Turn MODE SELECT switch to RUN.
The program is now locked, but all settings can be viewed. The unit can be unlocked by
following the same steps except adjust the DISPLAY/PROGRAM knob to “unL” in step 2.