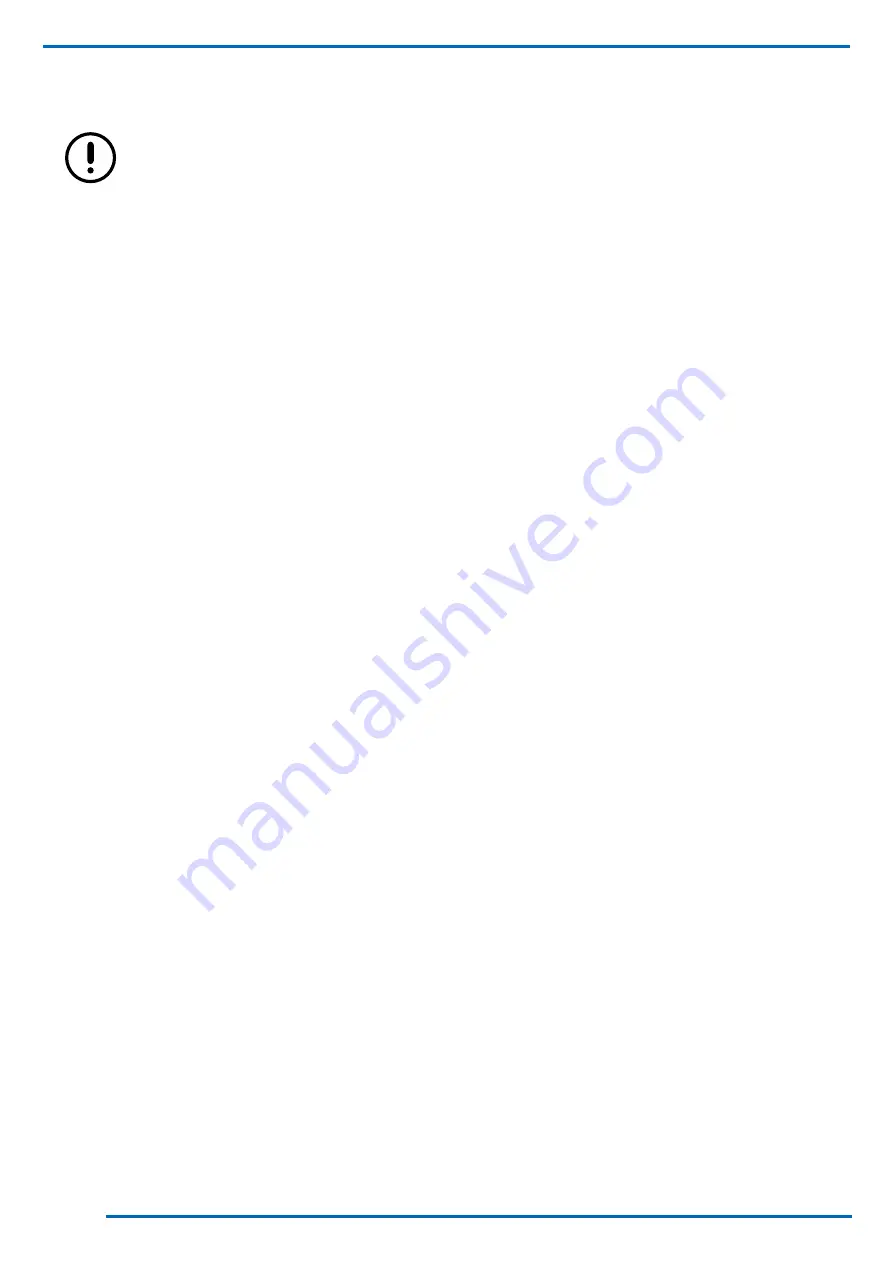
56
We reserve the right to make changes without any prior notice.
Translation from original instructions
7.3.6.5
Setting the operating setpoint difference
The value stored in the operating temperature difference parameter, as set at the factory, is the result of our
experience with different systems.
An incorrect value will eventually reduce the setting efficiency.
Below is the procedure to be followed to edit the temperature difference setpoint.
- go to the main screen and press the arrow right button;
-
click the arrow down button to select the “Flowzer” function and then press “Enter” to confirm;
-
Press the button “SET” to access the screen where the setpoint difference value is set up: use the “arrow” buttons to
move and select the parameter to be edited.
-
Press “ENTER” to enable the edit window.
-
Use the “arrow” buttons to set the new value and press “ENTER” to confirm.
7.3.6.6
Instructions for system start-up
In addition to the instructions provided in the section on unit “Commissioning”, a check is required in systems featuring the
“VPS” function for correct sizing of the pumps in order to ensure proper setting and increased efficiency under low load
conditions.
Correct sizing is obtained with checking of the flow rate in the bypass and in the primary circuit.
The bypass (or hydraulic circuit breaker) compensates any flow rate differences between the primary circuit where the VPS
system management is present and the secondary circuit where management is to be provided by the customer.
To have an optimal delivery temperature in the system/plant and maximum efficiency, the flow rate in the primary circuit
must be the same as that in the secondary circuit and therefore no water must pass through the bypass.
In the case of system/plant operating conditions with a flow rate lower than 50% of the rated flow rate of the refrigerant unit,
the primary circuit water will go through the bypass.
For correct operation of the unit, even when there is no secondary circuit demand, 50% of the flow rate must be ensured in
the primary circuit.
This check requires the system to be loaded.
7.3.6.7
Checking the rated flow rate
The operations to carry out are as follows.
1. start the VPS system on the primary circuit;
2.
start the secondary circuit at the rated flow rate;
3.
allow the system to reach a steady state (stable speed/frequency of the pump).
The check can be considered successful if at steady state the pump of the primary circuit operates at a stable speed above
80% and the pressure difference at the ends of the unit is within the value range set in parameters “PA22” and “PA55”.
On the other hand, if the value ΔPex is higher than the setpoint in parameter “PA55”, the rated flow to the secondary circuit
is higher than the rated flow of the unit.
In this condition, the possibility should be investigated to reduce the flow rate to the secondary circuit in order to bring the
pressure difference at the ends of the unit below the setpoint in parameter “PA55”.
If, at steady state, the pump of the primary circuit works at a stable speed below 80%, the pump is oversized for the specific
system/plant and it should therefore be re-selected, otherwise its control margin would be excessively reduced with conse
-
quent reduction in efficiency of the variable flow rate system.
Finally, if the pump in the primary circuit at steady state operates at 100% and the value ΔPex is lower than the setpoint in
parameter “PA22”, the pump in the VPS system cannot overcome the head losses of the primary circuit. In this case, if there
is no margin for improvement on the primary circuit (partially closed valves/gate valves, clogged filters, etc.), the pump must
be replaced with one having a higher head.