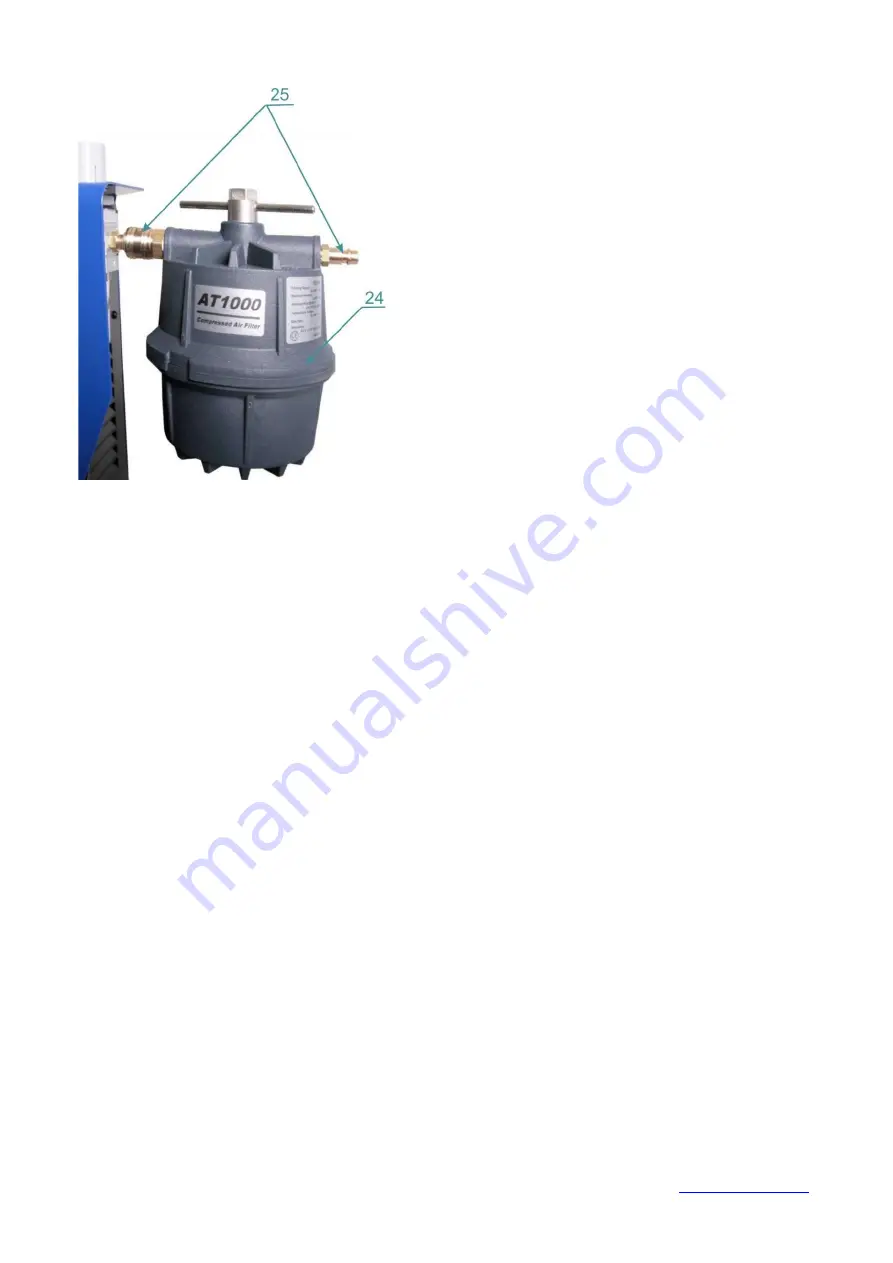
19/30
ALFA IN a.s ©
www.alfain.eu
Pic. 5 Air filter
9. CUTTING
1. The burning time of the pilot arc must be limited to the time necessary. The
team wear of the nozzle and electrode is reduced. Frequent idling starts
that the nozzle and electrode are loaded and the pilot arc resistance ballast
could be played.
2. After cutting, never switch off the machine with the main switch, but always
let the so-called torch cooling cycle run. Perform an immediate shutdown
only in an emergency.
3. Compressed air has a decisive influence on the quality of the cut, the
service life of the nozzles, electrodes and the entire burner. Make sure that
the pressure value is set correctly: the optimum value is 5.5 bar,
fluctuations in the range of 5.0 - 6.0 bar are permissible. The air must be
free of mechanical impurities, oil and water condensate. These
contaminants reduce the quality of the cut, cause instability and the arc to
go out, and can damage the torch. The compressed air source must
therefore be equipped with efficient filtration and a reliable oil and water
condensate separator. The use of a filter and separator built into the
SVAROG 105 PLASMA as the only stage of air conditioning is completely
insufficient. In cases where the compressor sucks in high-humidity air,
which results in the need for frequent desilting of the pressure vessel, it is
necessary to include another effective sludge trap as the 3rd stage in the
supply. The collected condensate must be drained daily from all sludge
traps and compressor pressure vessel. Pay attention to a good el. contact
of earthing pliers and material.
The nozzle and electrode must be inspected and replaced in a timely