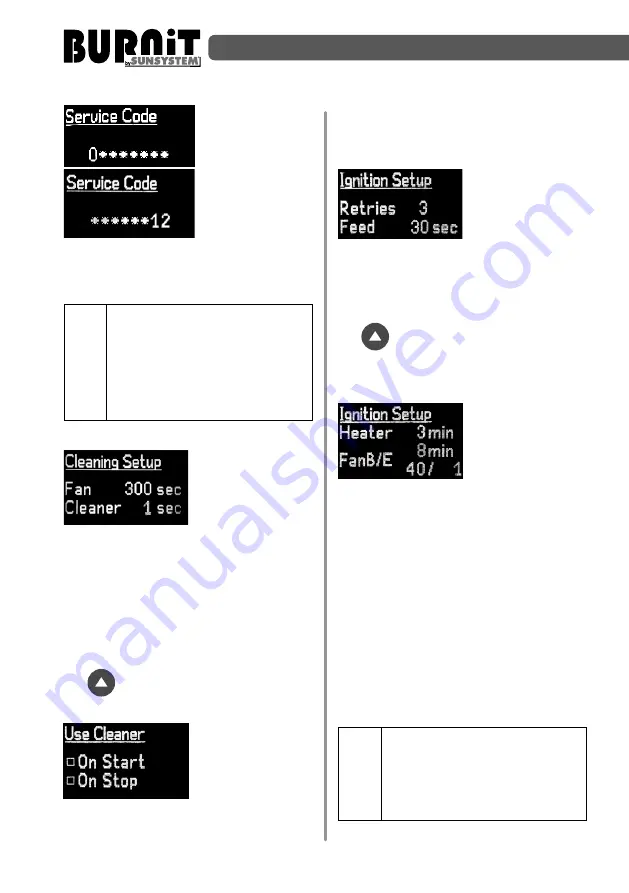
TECHNICAL PASSPORT. INSTALLATION and OPERATION MANUAL
TECHNICAL PASSPORT. INSTALLATION and OPERATION MANUAL
20
The service menu
comprises only
and uniquely
parameters with
direct impact on
boiler combustion
process, as well as
on
heating
installation management (depending on
the peripherals management capacity of
the boiler digital controller unit).
Fuel switching and / or change
the configuration of the heating
installation must be performed
by an authorized installer /
service. Some of these reasons
may affect the safe operation of
the facility.
9
.3.1. Cleaning setup
The burner
performs automatic
cleaning before
each ignition and
shut-down.
You can use this menu to adjust the
running time of the main fan
(FAN)
and
of the cleaning motor
(Cleaner) -
not
active
.
Select the desired option using the
navigation arrows. Use the „
Enter
”
button to open the next parameter. Use
the
button to open the next page of
the menu.
In this submenu
you can activate or
deactivate
the
automatic cleaning
of the burner in
Ignition
(Start)
mode or extinguished
(Stop)
mode. The checkmark in the box
indicates that the automatic cleaning
system is active.
9.3.2. Ignition setup
In this submenu
you can set the
number of attempts
(
Retries
) to ignite
the burner and the
time of the initial feed portion of pellets
(
Feed
). Select the desired option using
the navigation arrows. Use the „
Enter
”
button to open the next parameter. Use
the
button to open the next page of
the menu.
9.3.3. Cycle setup
Use this submenu
to adjust the
running time of the
heater (
Heater
) and
the running time
and output of the main fan during the
ignition of the initial portion of pellets.
Principle of operation:
After feeding the initial portion of pellets,
the heater operates for
3
minutes , and
the main fan is turned on at
40%
of its
capacity and operates for
8
minutes (the
heater continues to work). If upon the
expiration of that period the photosensor
detects the presence of stable flame, the
burner enters into operating mode. If no
stable flame is present, the burner feeds
in pellets again and repeats the process.
NOTE! Fan B/E 40/1 is a set up
for the main fan at 40% and set
up for the fan for fume gases 1%
(if there is installed). Fan for the
fume gases must be connected
to termonal FSG (see shceme 5).