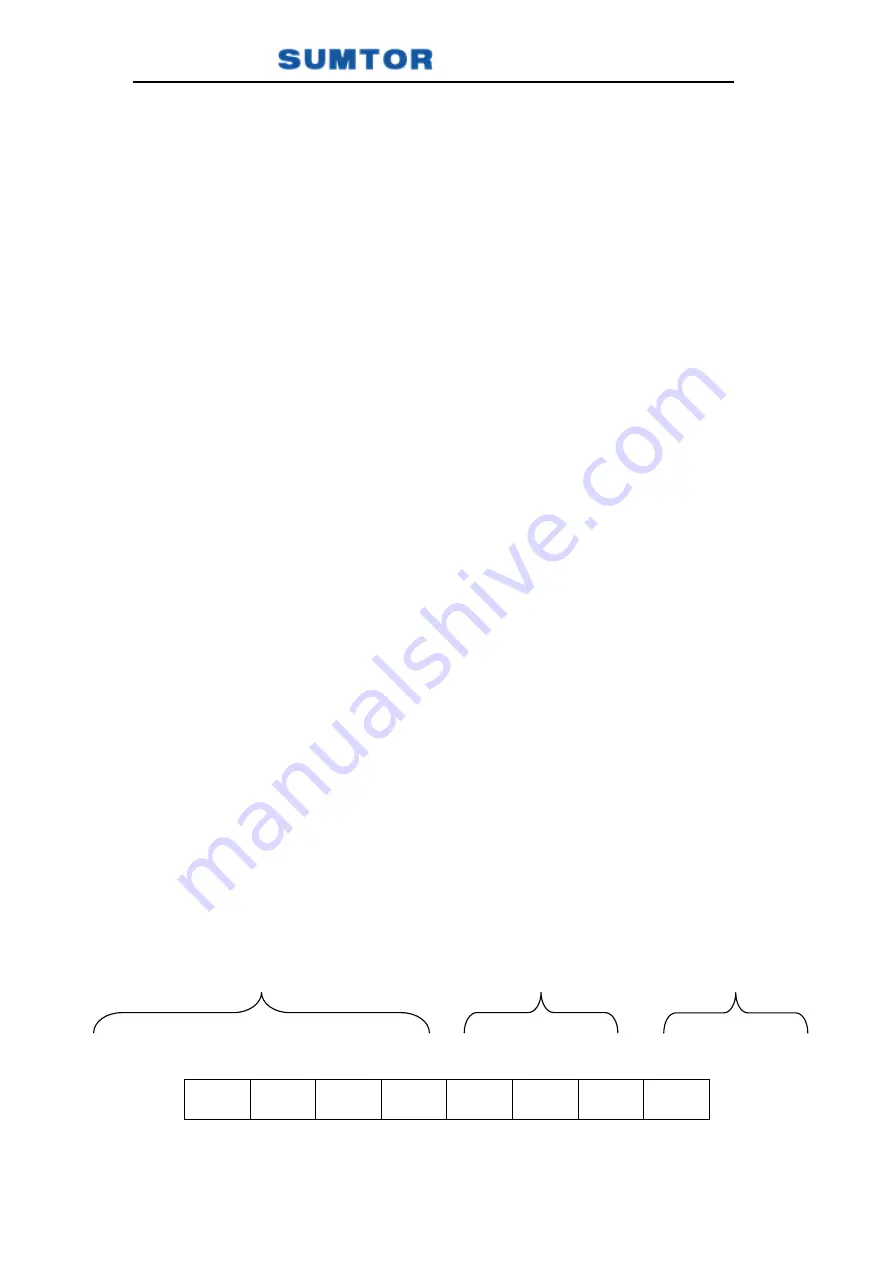
HSC86AInstruction manual of hybrid servo driver
11
requirements, the shielded wire of the control signal cable is grounded at one end: the upper end of the
shielded wire is grounded and the shielded wire End of the drive is floating. The same machine is only
allowed to be grounded at the same point. If it is not a real ground wire, the interference may be serious.
At this time, the shielding layer is not connected. If the conditions permit, thermal grounding
technology is most effective for shielding.
2) The pulse and direction signal lines and the motor line are not allowed to be bundled side by side,
preferably separated by at least 10cm or more, otherwise the motor noise will easily interfere with the
pulse direction signal and cause motor positioning inaccuracy, system instability and other faults.
3) If one power supply is used for multiple drives, parallel connection should be adopted at the power
supply, and it is not allowed to go to one first and then to another chain connection.
4) It is strictly forbidden to plug and unplug the driver terminal with el ectricity. When the live motor
stops, a large current still flows through the coil. Pulling and plugging the terminal will cause a huge
instantaneous induced electromotive force to burn the driver.
5) It is strictly forbidden to insert the wire head into the terminal after tin, otherwise the terminal may
be damaged due to overheating of the contact resistance.
6) The wiring head should not be exposed outside the terminal to prevent accidental short circuit and
damage to the driver.
四、DIP switch setting
HSC86A digital integrated low-voltage servo driver adopts 8-bit dial switch to
set the subdivision accuracy (electronic gear ratio), the initial direction of
motor rotation, self-test and function mode selection. The detailed description
is as follows
:
SW1
SW2
SW3
SW4
SW5
SW6
SW7
SW8
Direction and function mode settings
Subdivision accuracy (electronic gear ratio)
Motor selection