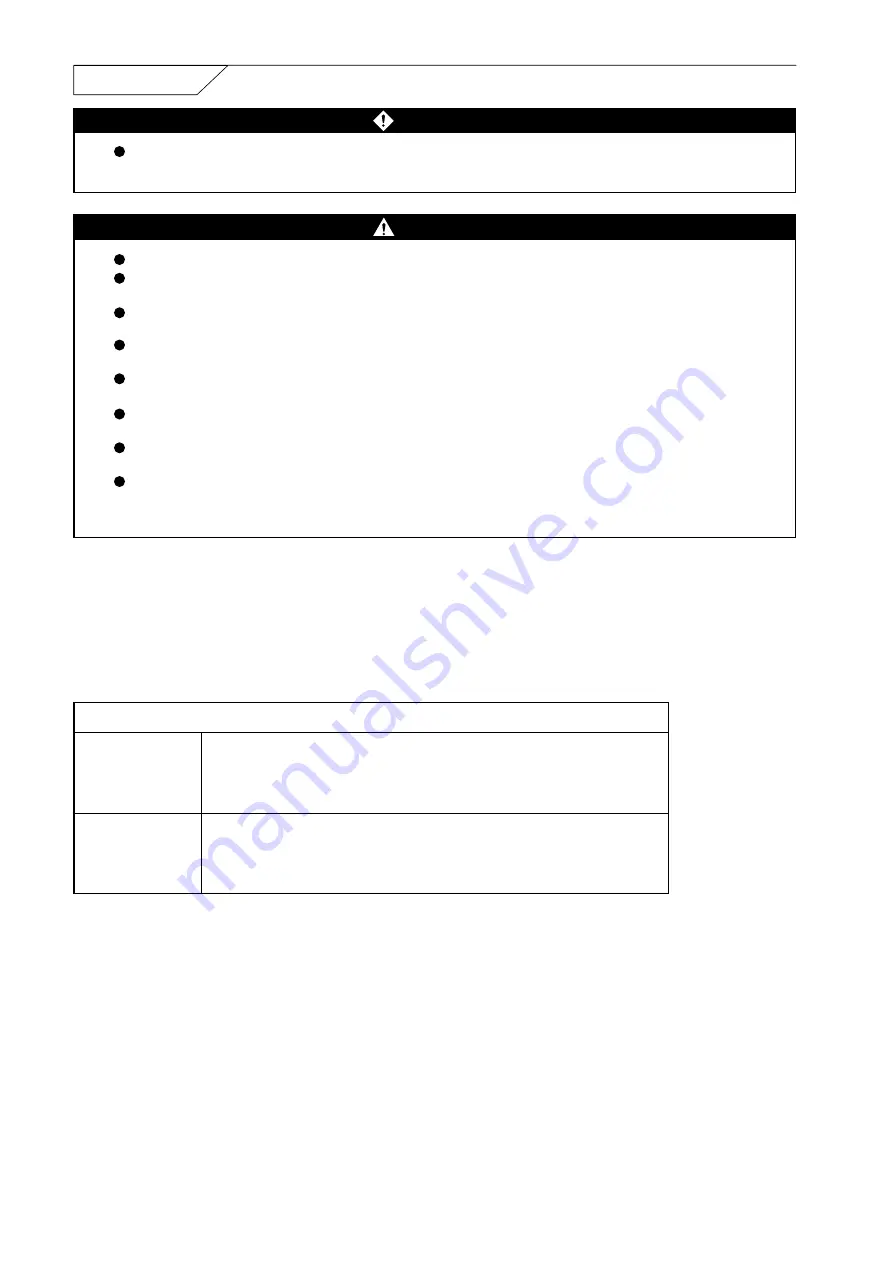
7
8. Operation
After installation, check the following points prior to operation.
(2) Is the reducer correctly coupled with the mating machine ?
(1) Is the oil filled to the correct oil level ?
(3) Are foundation bolts firmly tightened ?
(4) Does the direction of rotation conform to the one specified and designed for ?
After confirming the above, allow for a no-load break-in period. Then gradually apply the design load.
At this time, confirm the following :
DANGER
Never approach or touch any rotating parts (shaft, etc.) during operation. Loose clothing caught in these
rotating parts may result in severe injury and/or death.
CAUTION
The reducer will get very hot during operation. Do not touch or come in contact in any way with the reducer ;
otherwise, you may suffer burns.
If the reducer is operating in an abnormal way, stop the unit immediatery ; otherwise, electric shock, personal
injury, or fire may result.
Do not operate the reducer in a manner that exceeds its rating criteria ; otherwise, injury or damage to the
system may result.
Do not remove any covers or open the reducer during operation ; otherwise, splashing lubricant may cause
burns.
Do not loosen the oil filler plug during operation ; otherwise, splashing lubricant may cause burns.
When reversing the direction of rotation, first bring the unit to a complete stop, then commence reverse
rotation ; otherwise, the system may be damaged.
Check the oil level with the oil gauge before operation.
When using pole change motors to change from high speed to low speed, control the fan rotation speed so that
regeneration braking torque does not act on the reducer.
Items to be checked during break-in period/possible causes.
Abnormal sound
and vibration
(1) The housing is deformed because the installation surface is irregular.
(2) Resonance is occurring due to the lack of rigidity of the installation base.
(3) The shaft center is not properly aligned with the
motor
.
(4) The vibration of the fan is transmitted to the
reducer
.
(1) The motor current has exceeded the rated current shown in the rating plate.
(2) The voltage rise and drop of the motor is too large.
(3) The ambient temperature at which the reducer is operating is too high.
(4) The oil is not at its specified level (too low or too high).
The surface
temperature of the
reducer is
abnormally high.
Table 6
When an anomaly is found, stop operation, and contact the nearest agent, dealer, or service office.
The reducer is not operated for an extended period, operate the unit a minimum of 5 minutes for every 200
hours of non-operation.
Summary of Contents for PARAMAX SFC Series
Page 14: ...GM2202E 1 0 2004 2...