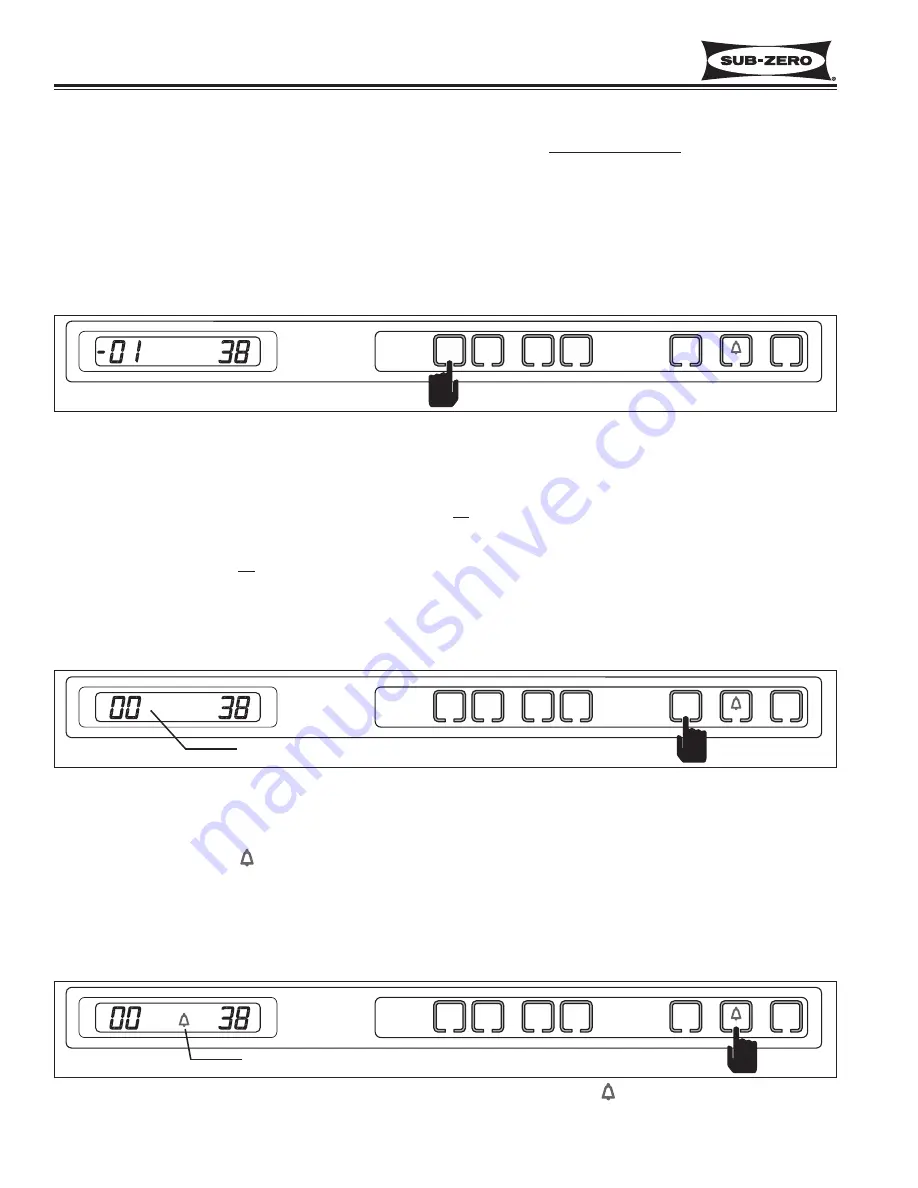
Electronic Control System
Integrated
Integrated
(700-
(700-
3
3
T
T
ALL)
ALL)
Series
Series
3-6
#3758412 - Revision B - December, 2006
Adjusting Set-Point (Temperature Adjustment)
To adjust set-points, press WARMER or COLDER key on control panel in multiple key strokes until desired set-point
is achieved (See Figure 3-6). One key stroke equals one degree change.
NOTE:
The temperature range in a freezer zone is -5°F (-21°C) to +5°F (-15°C). The temperature range in a refrig-
erator zone is +34°F (+1°C) to +45°F (+7°C).
NOTE:
The initial stroke of the WARMER or COLDER key will change the previous set-point by one degree.
NOTE:
The set-point will be displayed on the LCD for 10 seconds after the last key stroke. After the 10 second
delay, the zone temperature will be displayed. As the zone temperature changes, the temperature displayed on the
LCD will change by no more than one degree per minute.
UNIT
ICE
REFRIGERATOR
ON/OFF
ON/OFF
ON/OFF
WARMER
COLDER
FREEZER
WARMER
COLDER
Figure 3-6. Adjusting Set-Point - Press WARMER or COLDER Key In Multiple Key Strokes
Icemaker System ON/OFF
When a unit first arrives in a home, the icemaker system is off. By pressing and releasing the ICE ON/OFF key,
power is allowed to the icemaker system and “ICE” appears on the LCD (See Figure 3-7). To switch the icemaker
system off, press and release the ICE ON/OFF key again and the “ICE” indicator disappears from the LCD, indicat-
ing the icemaker system is off.
NOTE:
When in “Sabbath Mode,” the icemaker system is deactivated. Sabbath Mode will be explained later.
NOTE:
To allow ice to freeze fully and reduce effects of low water pressure, power to the icemaker system is inter-
rupted for 45 minutes after each ice harvest. This can be bypassed for service purposes by switching the icemaker
system OFF, then back ON with the ICE ON/OFF key.
Figure 3-7. Icemaker System ON/OFF - Press ICE ON/OFF Key
ICE
UNIT
ICE
REFRIGERATOR
ON/OFF
ON/OFF
ON/OFF
WARMER
COLDER
FREEZER
WARMER
COLDER
UNIT
ICE
REFRIGERATOR
ON/OFF
ON/OFF
ON/OFF
WARMER
COLDER
FREEZER
WARMER
COLDER
Ice system active if “ICE” is displayed
Door Ajar Alarm Feature ( ) ON/OFF
All units are equipped with a door ajar alarm feature. To enable the door ajar alarm, press and release the Alarm
Bell ON/OFF key on the control panel (See Figure 3-8). The bell indicator appears on the LCD indicating the alarm
feature is active. With the alarm enabled, the bell indicator will flash and an audible alarm will beep whenever the
door is left open for more then thirty seconds. To disable the door ajar alarm, press the Alarm Bell ON/OFF key
again and the bell indicator disappears from the LCD, indicating the alarm feature is inactive.
Door Ajar Alarm active if Bell is displayed
Figure 3-8. Switching Door Ajar Alarm ON or OFF - Press ( )ON/OFF Key
Summary of Contents for 700TC-3
Page 2: ......