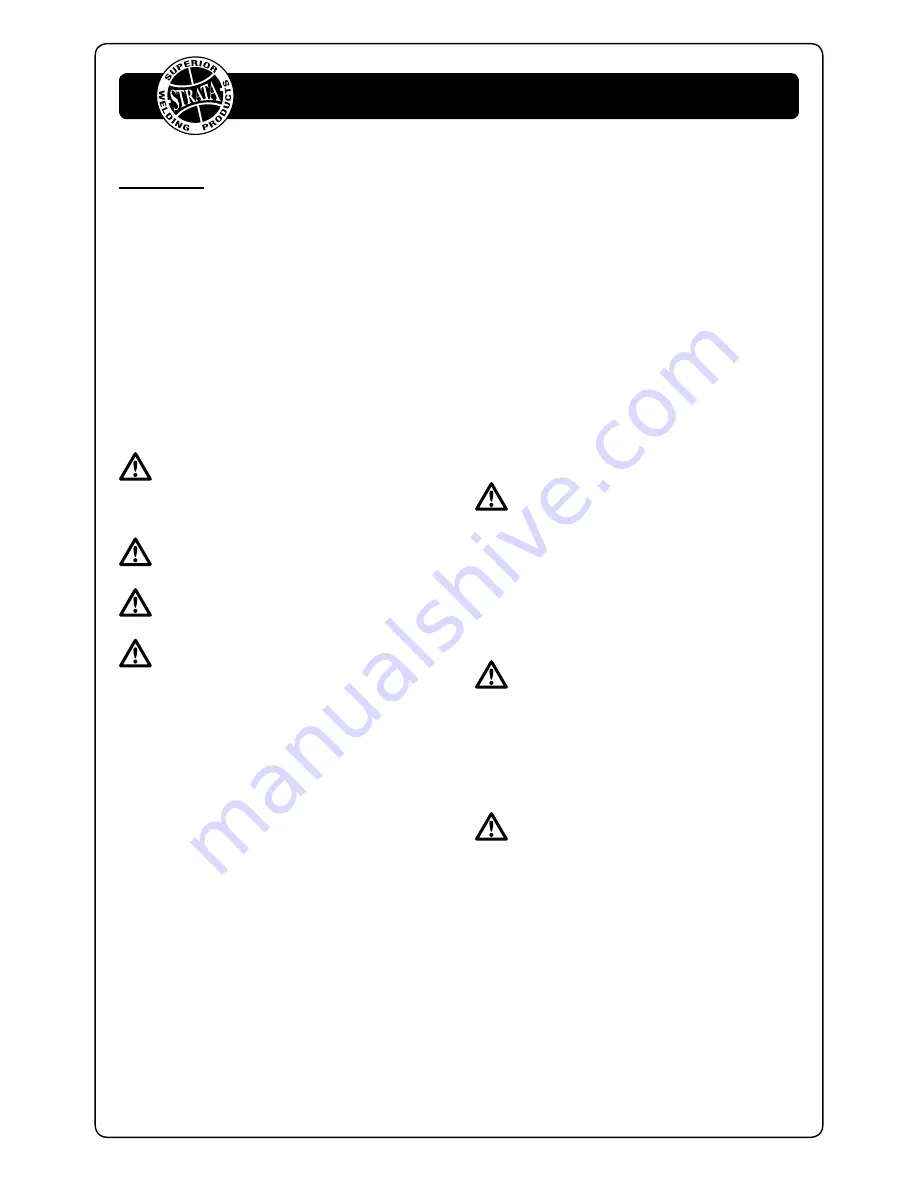
17
www.strata.co.nz
ADVANCEMIG 200
Safety
Store and Retain this Manual
Retain this manual for the safety warnings and precau-
tions, assembly, operating, inspection, maintenance and
cleaning procedures. Write the product’s serial number
into the NOTES section at the rear, and keep this manual
and the receipt in a safe and dry place for future reference.
Important Safety Information
Failure to follow the warnings and instructions may result
in electric shock, fire, serious injury and/or death. Save all
warnings and instructions for future reference.
This is the safety alert symbol to alert you to po-
tential personal injury hazards. Obey all safety
messages that follow this symbol to avoid possible
injury or death.
DANGER!
indicates a hazardous situation which, if
not avoided, will result in death or serious injury.
WARNING!
indicates a hazardous situation which, if
not avoided, could result in death or serious injury.
CAUTION,
used with the safety alert symbol,
indicates a hazardous situation which, if not avoid-
ed, could result in minor or moderate injury.
NOTE,
used to address practices not related to personal
injury.
General Safety Warnings
1. Maintain labels and nameplates on the welder.
These car-
ry important information. If unreadable or missing, contact
Euroquip for a replacement.
2. Avoid unintentional starting.
Make sure the welder is
setup correctly and you are prepared to begin work before
turning on the welder.
3. Unplug before performing maintenance.
Always unplug the welder from its electrical outlet before
performing any inspection, maintenance, or cleaning pro-
cedures.
4. Never leave the welder unattended while energised.
Turn power off before leaving the welder unattended.
5. Do not touch live electrical parts.
Wear dry, insulating
gloves. Do not touch the electrode or the conductor tong
with bare hands. Do not wear wet or
damaged gloves.
6. Protect yourself from electric shock.
Do not use
the welder outdoors. Insulate yourself from the work
piece and the ground. Use non-flammable, dry insulating
material if possible, or use dry rubber mats, dry wood or
plywood, or other dry insulating material large enough to
cover the area of contact with the work or the ground.
7. Avoid inhaling dust.
Some dust created by power
sanding, sawing, grinding, drilling, cutting, welding and
other construction activities, contain chemicals known to
cause cancer, birth defects or other harm. Your risk from
these exposures varies, depending on how often you do
this type of work. To reduce your exposure to these chemi-
cals, work in a well-ventilated area, and work with approved
safety equipment, such as dust masks that are specially
designed to filter out microscopic particles.
8. People with pacemakers should consult their
physician(s) before using this machine.
WARNING!
Electromagnetic fields in close proximity to a heart
pacemaker could cause interference, or failure of
the pacemaker. The use of a Welder is NOT REC-
OMMENDED for pacemaker wearers. Consult your
doctor.
9. Ensure that the unit is placed on a stable location before
use.
WARNING!
If this unit falls while plugged in, severe injury,
electric shock, or fire may result.
10. Transportation Methods
Lift unit with the handles pro-
vided, or use a handcart or similar device of adequate ca-
pacity. If using a fork lift vehicle, secure the unit to a skid
before transporting.
CAUTION!
Disconnect input power conductors from de-ener-
gized supply line before moving the welding power
source.
11. Exercise good work practices.
The warnings, precau-
tions, and instructions discussed in this instruction manual
cannot cover all possible conditions and situations that may
occur. It must be understood by the operator that common
sense and caution are factors which cannot be built into
this product, but must be considered by the operator.