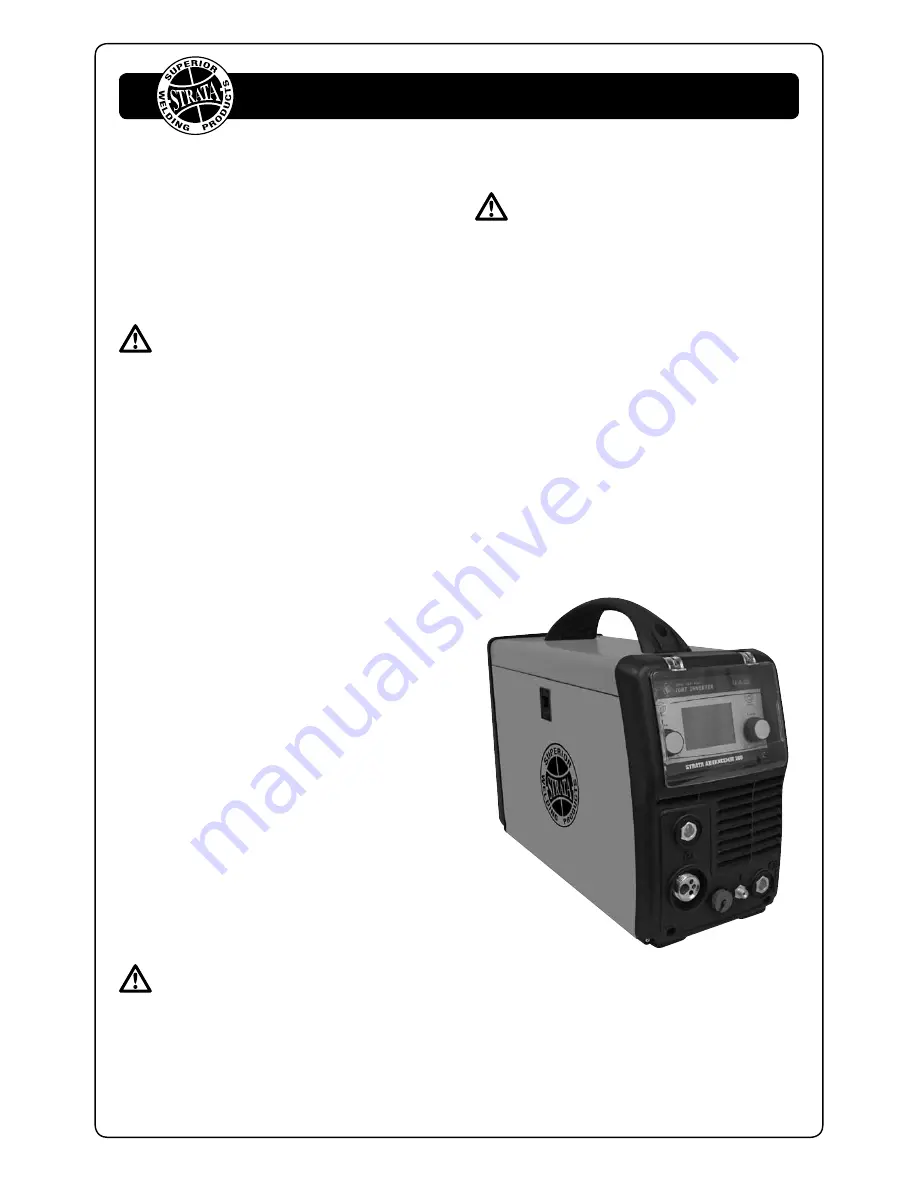
21
www.strata.co.nz
ADVANCEMIG 200
Cylinders
WARNING!
Gas cylinders contain gas under high pressure. If
damaged, a cylinder can explode. Since gas cylin-
ders are normally part of the welding
process, be sure to treat them carefully.
1. Protect compressed gas cylinders from excessive
heat, mechanical shocks, and arcs.
2. Install and secure cylinders in an upright position by
chaining them to a stationary support or equipment
cylinder rack to prevent falling or tipping.
3. Keep cylinders away from any welding or other
electrical circuits.
4. Never allow a welding electrode to touch any cylinder.
5. Use appropriate shielding gas, regulators, hoses,
and fittings designed for the specific application;
maintain them and their associated parts in good con-
dition.
6. Turn your face away from the valve outlet when
opening the cylinder valve.
7. Do not weld on coated metals, such as galvanized,
lead, or cadmium plated steel, unless the coating is
removed from the weld area, the area is well venti-
lated, and if necessary, while wearing an air- supplied
respirator. The coatings and any metals containing
these elements can give off toxic fumes if welded.
Fire & Explosive Risks
WARNING!
Sparks and spatter fly off from the welding arc.
The flying sparks and hot metal, weld spatter,
work piece, and hot equipment can cause fires
and burns.
Accidental contact of electrode or welding wire to metal
objects can cause sparks, overheating, or fire.
1. Protect yourself and others from flying sparks and hot
metal.
2. Do not weld where flying sparks can strike flammable
material.
3. Remove all flammables within 10m of the welding
site.
4. Be alert that welding sparks and hot materials from
welding can easily go through small cracks
and openings to adjacent areas.
5. Watch for fire, and keep a fire extinguisher nearby.
6. Be aware that welding on a ceiling, floor, bulkhead, or
partition can cause fire on the hidden side.
7. Do not weld on closed containers such as tanks or
drums.
8. Connect the work lead/clamp to the job as close to
the welding area as practical to prevent welding cur-
rent from travelling long, possibly unknown paths and
causing electric shock and fire hazards.
9. Do not use a welder to thaw frozen pipes.
10. Remove the stick electrode from the holder or cut off
the welding wire at the contact tip when not in use.
Sparks & Hot Metal
WARNING!
Chipping and grinding causes flying metal, and as
welds cool they can throw off slag.
1. Wear an AS/NZS approved face shield or safety gog-
gles. Side shields are recommended.
2. Wear appropriate safety equipment to protect the skin
and body.