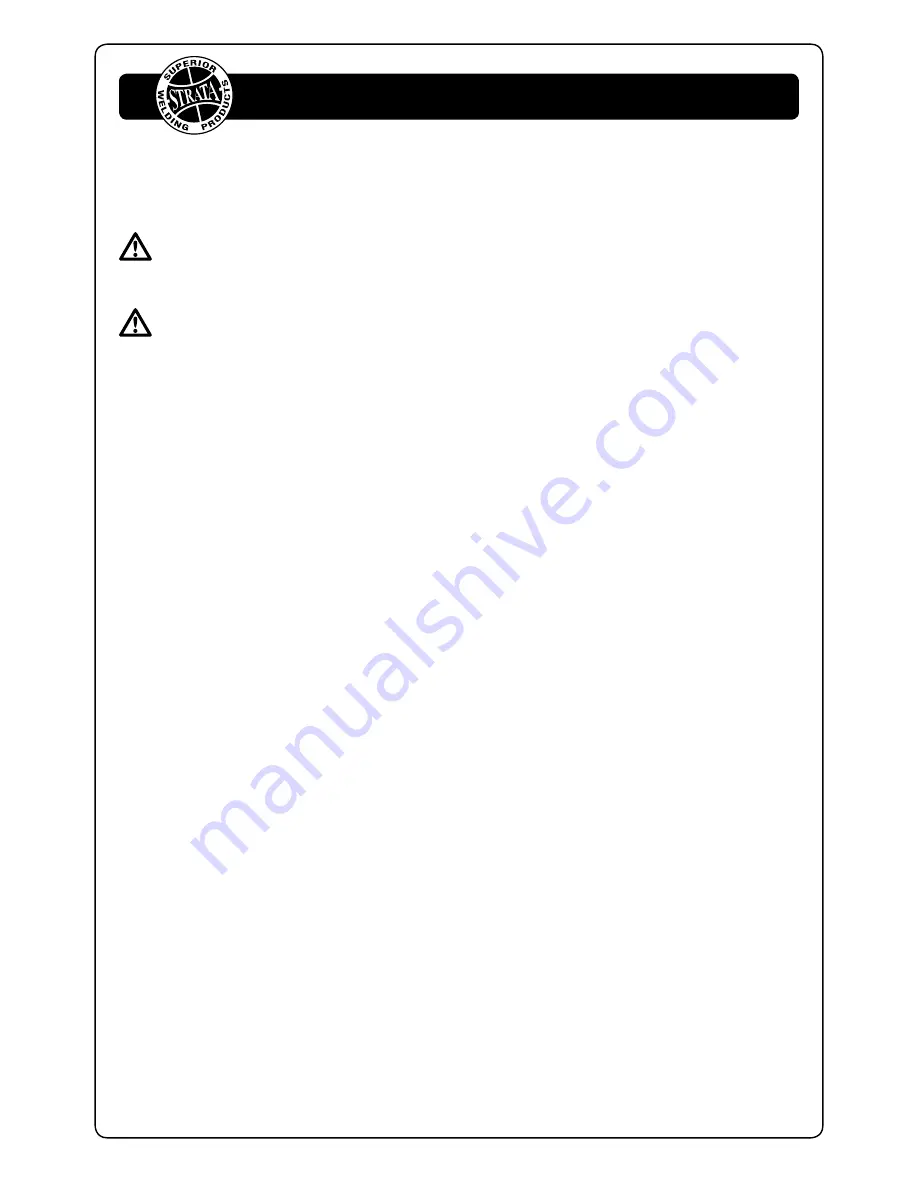
10
www.strata.co.nz
ADVANCEMIG 200
justment lever (16) to indicate the adjustment position.
The higher the number indicated, the higher the tension
that is set.
WARNING!
Before changing the feed roller or wire
spool, ensure that the mains power is switched
off.
WARNING!
The use of excessive feed tension
will cause rapid and premature wear of the drive
roller, the support bearing and the drive motor/
gearbox.
1.7 Connect the MIG Torch Euro Connector to the
MIG torch Euro connection socket (9) on the
front of the machine. Secure by firmly hand tight-
ening the threaded collar on the MIG Torch con-
nector clockwise.
1.8 Check that the correct matching MIG wire, drive
rollers (18) and MIG torch tip are fitted.
1.9 Connect the machine to suitable mains power us-
ing the mains input power lead. Switch the mains
power switch to ‘on’ to power up the machine.
Select MIG/MAG mode from the main menu
screen.
1.10 Set the spool gun switch (12) to ‘wire feeder’ po-
sition.
1.11 You are now ready to feed the wire through the
torch. With the wire feeder cover open, pull the
trigger of the MIG torch to check that the wire is
feeding smoothly through the feeder and into the
torch.
1.12 With the tip removed from the torch and the torch
laid out as straight as possible, activate the torch
trigger until the wire feeds out through the end
of the MIG torch. The AdvanceMig 200 has an
intelligent wire feeding system, when the torch is
triggered for more than 2 seconds without an arc
starting, the wire feeder will go into torch feeding
mode and operate at full speed. Replace the tip on
the MIG torch and trim off any excess wire.
2. Gasless Welding Operation
2.1 Connect the earth cable quick connector to the
positive welding power output socket (10). Con-
nect the earth clamp to the work piece. Contact
with the work piece must be firm contact with
clean, bare metal, with no corrosion, paint or
scale at the contact point.
2.2 Connect the MIG power torch polarity connection
(14) to negative (-). Note if this connection is not
made, there will be no electrical connection to the
welding torch!
2.3 Set the welding parameters using the control
knobs and LCD screen, following the instructions
in the previous section. You are now ready to
weld!
3. Gas Shielded Welding Operation
3.1 Connect the earth cable quick connector to the
negative welding power output socket (6) Con-
nect the earth clamp to the work piece. Contact
with the work piece must be firm contact with
clean, bare metal, with no corrosion, paint or
scale at the contact point.
3.2 Connect the MIG power torch polarity connection
(13) to positive (+). Note if this connection is not
made, there will be no electrical connection to the
welding torch!
3.3 Assemble the female gas quick connector to the
gas line and to the regulator outlet fitting. Con-
nect the gas regulator to a gas cylinder (not in-
cluded with machine) and connect the female
quick connector to the male gas inlet on the rear
of the machine. Ensure all connections are tight.
Open gas cylinder valve and adjust regulator,
flow should be between 10-25 l/min depending
on application. Re-check regulator flow pressure
with the torch triggered as static gas flow setting
may drop once gas is flowing.
3.4 Set the welding parameters using the control
knobs and LCD screen, following the instructions
in the previous section. You are now ready to
weld!