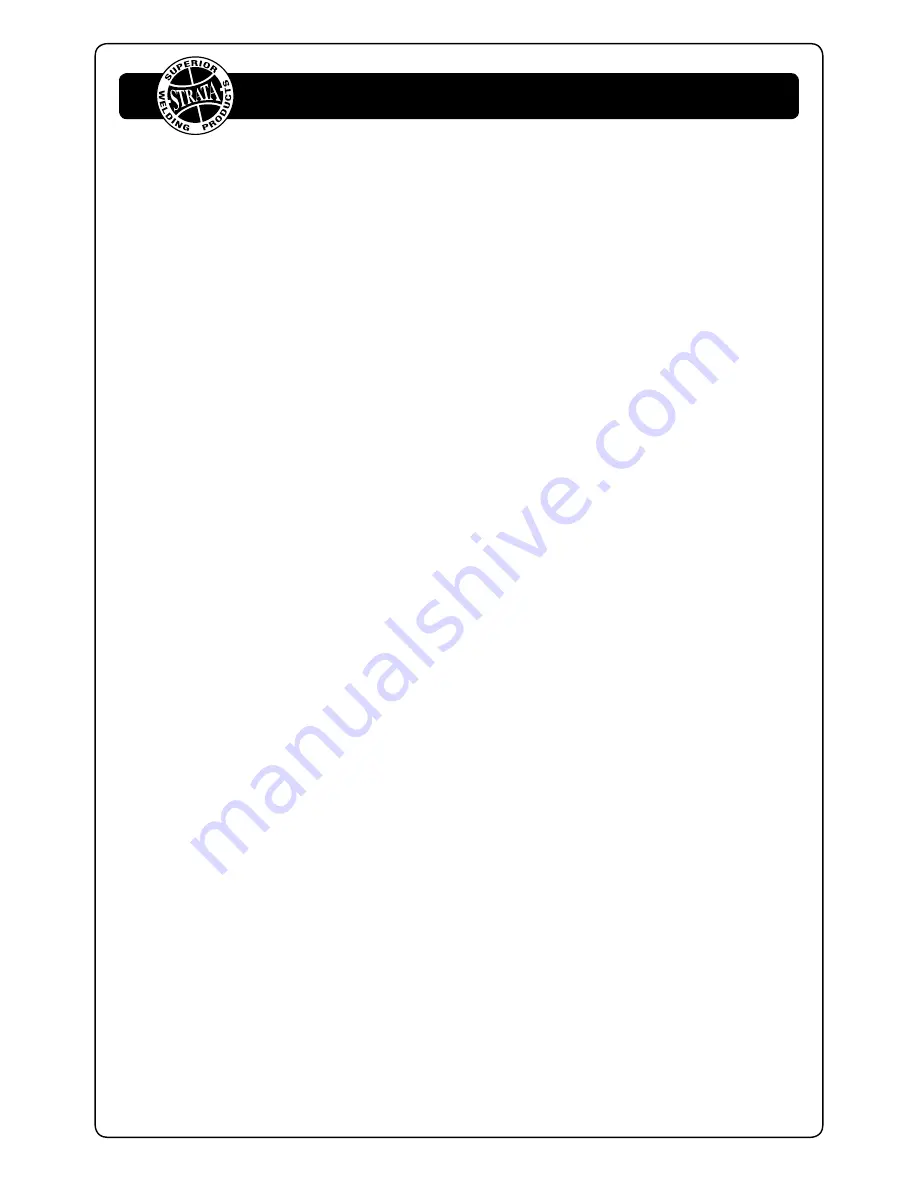
11
www.strata.co.nz
ADVANCEMIG 200
Note to welding with Aluminium and other soft wires.
MIG welding with aluminium provides a unique chal-
lenge, due to the low column strength of the wire. This
causes the wire to deform more as it is pushed through
the feed mechanism and the torch wire delivery liner,
greatly increasing friction. Because good MIG welding
results are dependent on a smooth wire feed, certain
changes must be made to the wire feed system to mini-
mise friction caused issues.
For a standard ‘push’ fed torch, a length of no longer
than 3m cable may be used, as well as the torch feed
liner must be changed to a special Teflon/ PVC liner,
rather than the conventional steel liner. Also the correct
style drive roller must be used and specific Aluminium
rated torch contact tip (or a standard tip in one size over-
size, e.g 0.8mm aluminium wire, use standard 1.0mm
contact tip). For this reason, it is quite common for op-
erators to have an extra MIG torch specifically set up for
aluminium use, if the machine is used for welding steel
as well.
Another option to overcome the friction issues is using a
spool gun, which will give better results than a 3m push
torch when welding aluminium. The ADVANCEMIG 200
is spool gun capable, refer following section for use with
a spool gun on the ADVANCEMIG 200.
4. Spool Gun Operation
Note: The Spool Gun is an optional extra for the
ADVANCEMIG 200
The spool gun is a very useful addition to a MIG welder.
It can be used for all types of MIG welding, but it has
two primary advantages over a conventional ‘push’ wire
feeder.
The main advantage is that distance that the wire has
to travel from the spool to the welding tip is very short,
compared with a conventional torch. This greatly re-
duces the wire feeding friction and improves the wire
feed speed smoothness and consistency, thus the weld-
ing quality is greatly improved. This is especially so with
‘soft’ wires such as Aluminium. It is difficult to get Alu-
minium to feed smoothly in welding machines equipped
with standard design wire feeders, even with special
torch liners and short torch lengths.
The second advantage is that the gun can allow the use
of the small D100 wire spools at a distance from the
power source (This distance is only limited by the length
of the spool gun lead). This is advantageous for high
cost wire, that is not used commonly such as Stainless
Steel or MIG brazing wire. It saves the outlay cost for a
much more expensive, larger D200 spool. When used
with the correct OEM spool gun, the welding voltage/
current may be controlled directly from the spool gun
for the ADVANCEMIG 200. This is especially useful in
synergic mode, as the primary MIG settings can be con-
trolled ‘one touch’ with the single knob on the spool gun.
4.1 Connect the earth cable quick connector to the
negative welding power output socket (6) Con-
nect the earth clamp to the work piece. Contact
with the work piece must be firm contact with
clean, bare metal, with no corrosion, paint or
scale at the contact point.
4.2 Connect the MIG power torch polarity connection
(13) to positive (+). Note if this connection is not
made, there will be no electrical connection to the
welding torch!
4.3 Connect the spool gun interface plug to the re-
mote socket (8). Connect the spool gun Euro
plug to the machine Euro connector (9). Set the
spool gun switch (12) to ‘spool gun’ position.
4.4 Assemble the female gas quick connector to the
gas line and to the regulator outlet fitting. Con-
nect the gas regulator to a gas cylinder (not in-
cluded with machine) and connect the female
quick connector to the male gas inlet on the rear
of the machine. Ensure all connections are tight.
Open gas cylinder valve and adjust regulator,
flow should be between 10-25 l/min depending
on application. Re-check regulator flow pressure
with the torch triggered as static gas flow setting
may drop once gas is flowing.
4.5 Set the welding parameters using the control
knobs and LCD screen, following the instructions
in the previous section. You are now ready to
weld!