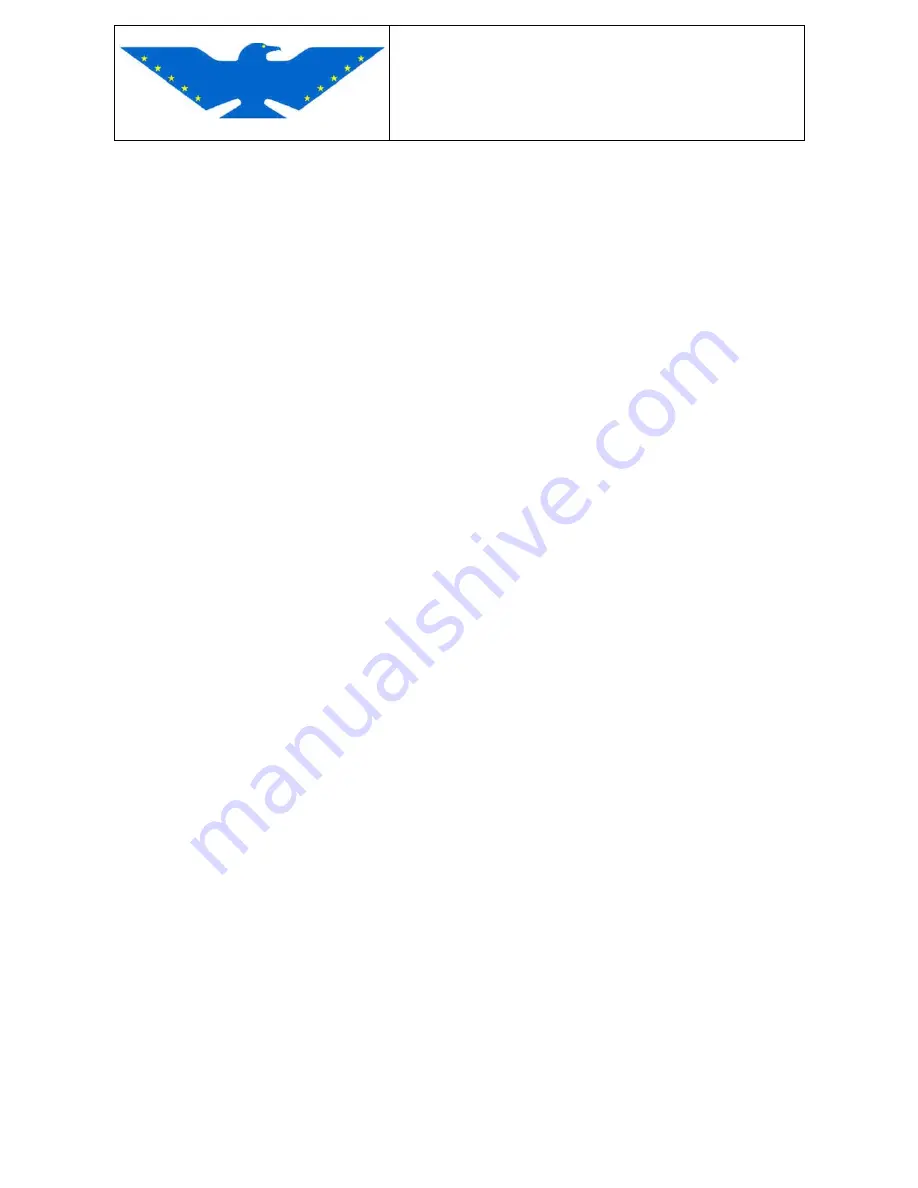
MAINTENANCE MANUAL
STORM Century S-LSA
STORM Century S-LSA
STORMAIRCRAFT
CHAPTER 2
INSPECTION AND MAINTENANCE PERIODS
PERIOD DESCRIPTION
This chapter includes all the inspection and maintenance procedures needed for STORM Aircraft.
The operative life of STORM Century S-LSA, as determined in the project, is 10000 flight hours.
Regular inspections shall be carried out when reaching respectively :
50
,
100
,
200
,
600
,
1000
and
1200
flight hours.
Moreover, after the first
25
hours , when the aircraft is new, the
100
hours inspection must also be
done on the engine,
as specified
in ROTAX 912 UL S engine manual
, and a visual check shall
be made on all screws coupling the structural parts.
The period between the two 200 hours inspections must not exceed one year.
For each inspected item, the person in charge for the aircraft maintenance shall sign the check list.
The completion of the inspection must be entered in a special register.
The results and the corrections must be registered in a special report and filed with the inspection
list in the maintenance register of the aircraft.
NOTE : maintenance may be done in advance, but for no reason should it be postponed.-
Maintenance can only be postponed upon agreement with the aircraft airworthiness check
Authority, upon engine and fittings builder’s specifications or on aircraft designer’s directions.