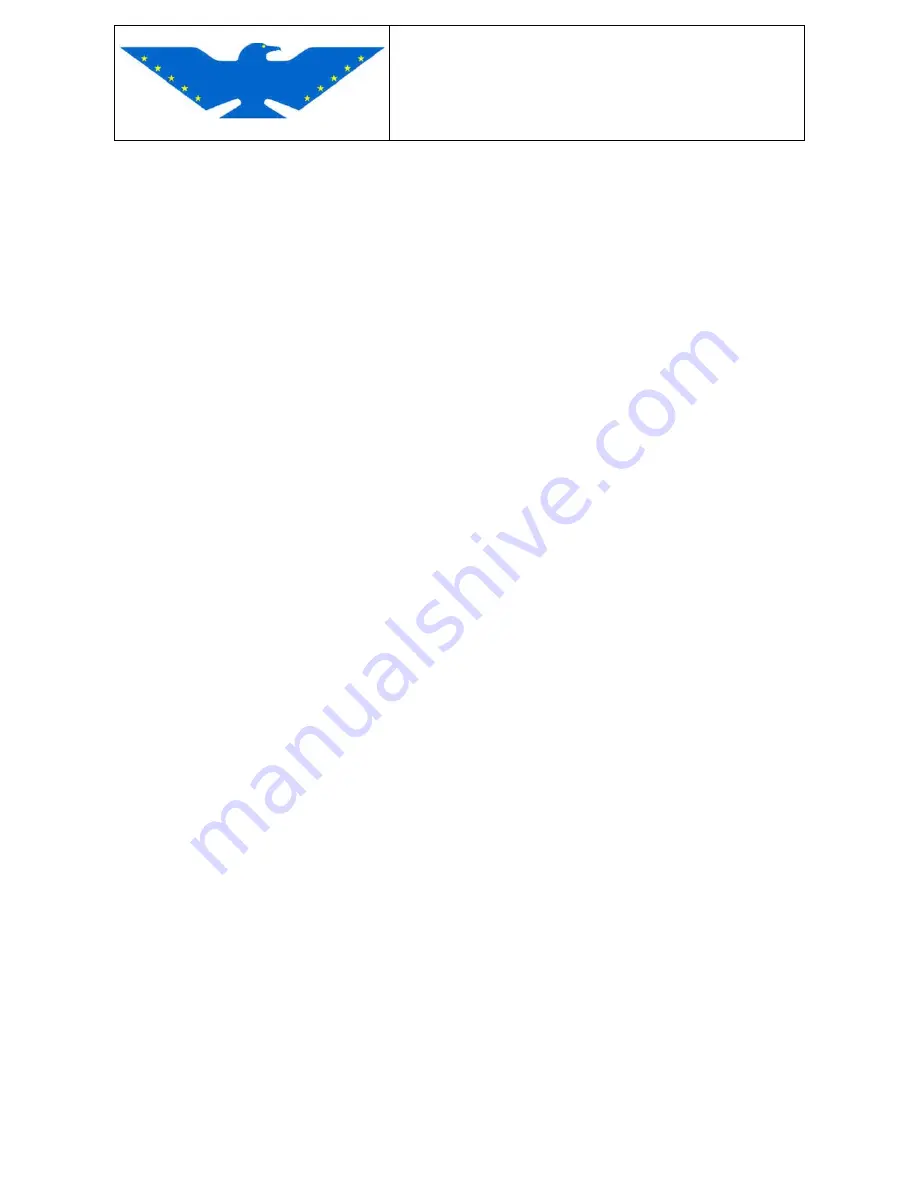
MAINTENANCE MANUAL
STORM Century S-LSA
STORM Century S-LSA
STORMAIRCRAFT
C. Topcoat Systems 1. Enamel
It can sometimes be a rather fine point whether a material is a lacquer or an enamel, but a pretty
general definition identifies a lacquer as a finish which cures by the evaporation of its solvents, and one
which can always be put back into its original condition by the use of thinners. An enamel cures by the
conversion of some of its solvents, by heat, oxidation, or by catalytic action. One test is to rub a little of
the thinner used to reduce the material for spraying over some of the dried material. If it softens the
film, the material is a lacquer. If it does not, it is in all probability an enamel.
The older enamels were essentially pigments suspended in an oil-type varnish. These are no longer used
in any production aircraft, but may be encountered when restoring old aircraft to their original finish.
These enamels air-dry to touch by flashing off, or the evaporation of the solvents; the true cure is by
oxidation or polymerization of the resins.
The only acrylic enamels which can be considered as suitable aircraft enamels are those whose cure is
produced by baking; that is, by heat conversion.
Conventional enamels are supplied at a solids content of about 45 to 50 percent; acrylics have about 2/3
this amount of solids, considerably less than the polyurethanes, which have at least 60 percent solids.
Enamels are reduced or thinned with a proprietary enamel reducer or with toluol by a ratio from 20 parts
of enamel to one part thinner, to a maximum of five parts enamel to one part thinner. Ten parts enamel to
one part thinner is about the typical reducing ratio. The thinners used have a high solvency and are used to
reduce the viscosity of the material, not to thin the solids. A five to one or a ten to one reduction allows
you to spray on a thin coat of material with high solids content.
Wash primer or epoxy primer should be applied to the surface, allowed to dry, then have its glaze broken
by scuffing it with crumpled kraft paper. Spray on a light mist coat of enamel, and allow the thinners to
flash off, which takes about fifteen minutes. Follow with a full wet cross-coat and allow to dry for about
forty-eight hours before taping or masking.
2. Acrylic lacquers
High-volume production of aircraft has brought out a requirement for a finish that has best been met with
acrylic lacquers. This material has a low solids content, compared with either conventional enamel or
polyurethane, and it may be applied over wash primer, favored for new production, or over any of the
epoxy primers. After the primer is thoroughly dry, rub it down with clean, dry kraft paper and apply the
finish. A white base coat should be applied to assure the proper color match for the finish.
The low solids content of acrylics makes them somewhat tricky in their application. Their low
viscosity and poor hiding qualities would seem to favor heavy coats, but not so; they should be
thinned, using four parts of material to five parts thinner. This seems more thinner than actually
required, but is good for a starting point. Adjust the amount of thinner to get the best coat. Spray on
a very light tack coat, then follow with at least three cross-coats, allowing about a half hour drying
time between coats. If the material is too heavy, pinholes or orange peel are likely to show up in the
finish. The gloss in the final coat may be improved by adding about a fourth as much retarder as you
have thinner in the material. If retarder has been used in the final coat, the finish should be allowed to
dry overnight before taping or masking.