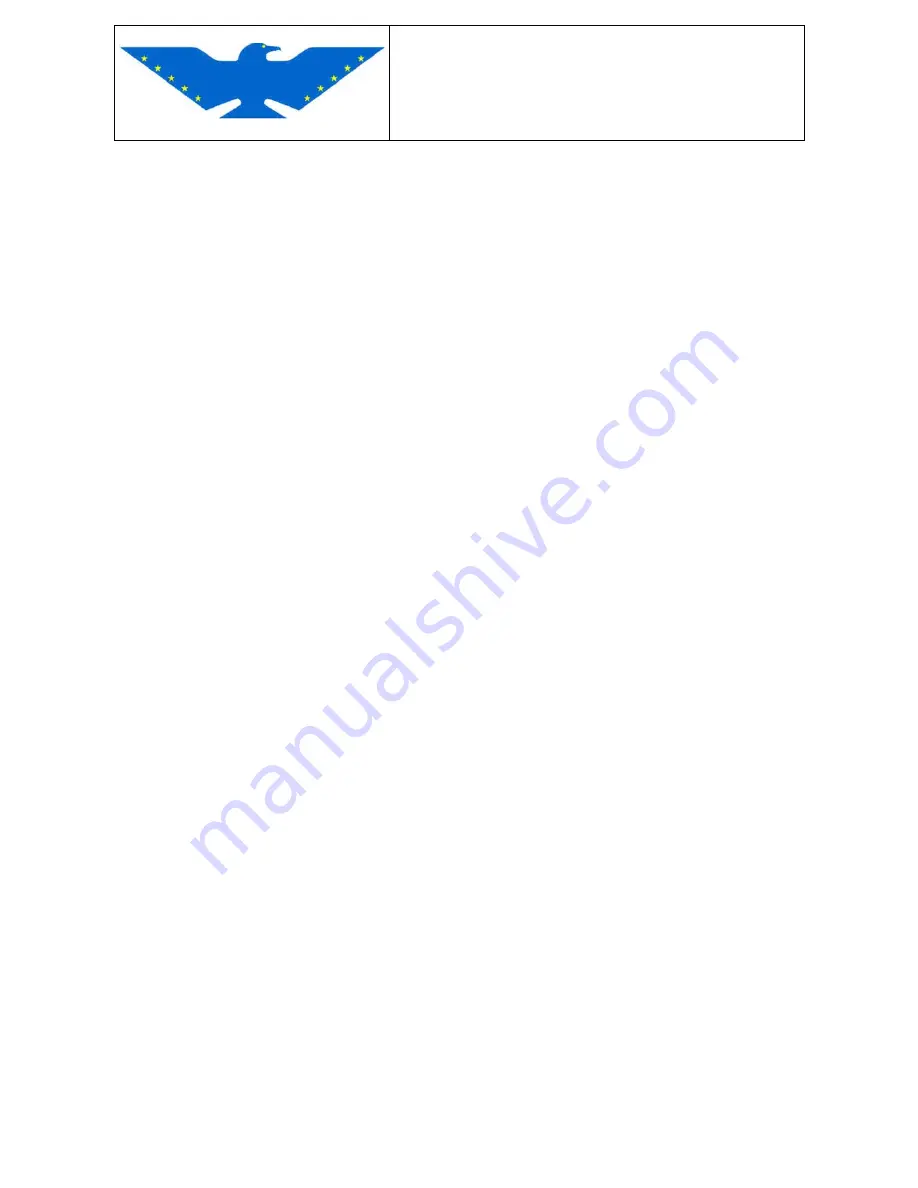
MAINTENANCE MANUAL
STORM Century S-LSA
STORM Century S-LSA
STORMAIRCRAFT
3. Polyurethane enamel
One of the most durable and attractive finishes for modern, high-speed, high-altitude airplanes is the
polyurethane enamel system. This hard, chemically resistant finish finds wide application with agricultural
aircraft, seaplanes, and others which operate in hostile environments.
Polyurethane enamel is a two-part, chemically cured finish having a very high solids content, at least
60%. The high gloss inherent with this system is primarily due to the slow-flowing resins used. The
thinners flash off quickly but the resins continue to flow for three to five days. It is this long flow-out time
and the even cure throughout the film that give the pigment and the film time to form a truly flat surface,
one that reflects light and has the glossy "wet" look which makes them so popular.
Polyurethane finish is used on agricultural air-craft and seaplanes because of its abrasion resistance and
resistance to chemical attack. Skydrol hydraulic fluid, which quite actively at-tacks and softens other
finishes, has only minimal effect on polyurethanes. Even acetone will not dull the finish. Paint strippers
must be held to the surface for a good while to give the active ingredients time to break through the film
and attack the primer.
Wash primers may be used for polyurethanes, but for corrosion resistance, epoxy primers are recom-
mended. The best undercoating is a conversion coating applied with care, using the manufacturer's
recommendation
to the letter,
with an epoxy primer applied over it.
Polyurethane enamel is mixed with its catalyst in the proportion specified in the mixing instructions,
usually in a one-to-one ratio. It is allowed to stand for about fifteen minutes as part of its induction
period. In this time the curing action is started. The primary purpose of this waiting period is to aid in the
inter-mixing or blending of the two components.
After this induction period, the material is stirred and mixed with reducer to the proper viscosity for
spraying. This is measured with a number 2 Zahn cup and is between 18 and 20 seconds. There is
more about this method of viscosity measurement in the section on paint shop equipment. When you
have the proper viscosity, spray on a
very
light tack coat, lighter than with a conventional enamel.
Allow it to set for about fifteen minutes so the thinner can flash off, or evaporate, and spray on a full wet
cross-coat.
The main problem with the application of poly-urethane lies in getting it on too thick. A film thickness of
about 1.5 mils (one-and-a-half thousandths of an inch) is about maximum for all areas except for those
subject to excessive erosion, such as leading edges. Too thick a film which might build up in the faying
strips can crack because of the loss of flexibility. A good practical way to tell when you have enough
material is to spray until you feel that one more pass will be just right, then quit right there, before you
make tha
t one more pass.
The high
solids content of polyurethane, its slow drying, and low surface
tension allow the finish to crawl for an hour or so after it has been put on. If you can still see the metal
when you think you have almost enough, don't worry; it will flow out and cover it. Almost no
polyurethane job will look good until the next day, because it is still flowing. It will actually flow for about
three to five days. It will be hard in this time, and the airplane may be flown in good weather, but the
paint below the surface is still moving.
Masking tape may be applied after 12 hours under the most ideal conditions, but it is far bet-ter if you
can wait 24 hours after application of the finish; it should be removed as soon after the trim is sprayed
as possible. If it is left on the surface for a day or so, it will be almost impossible to remove.