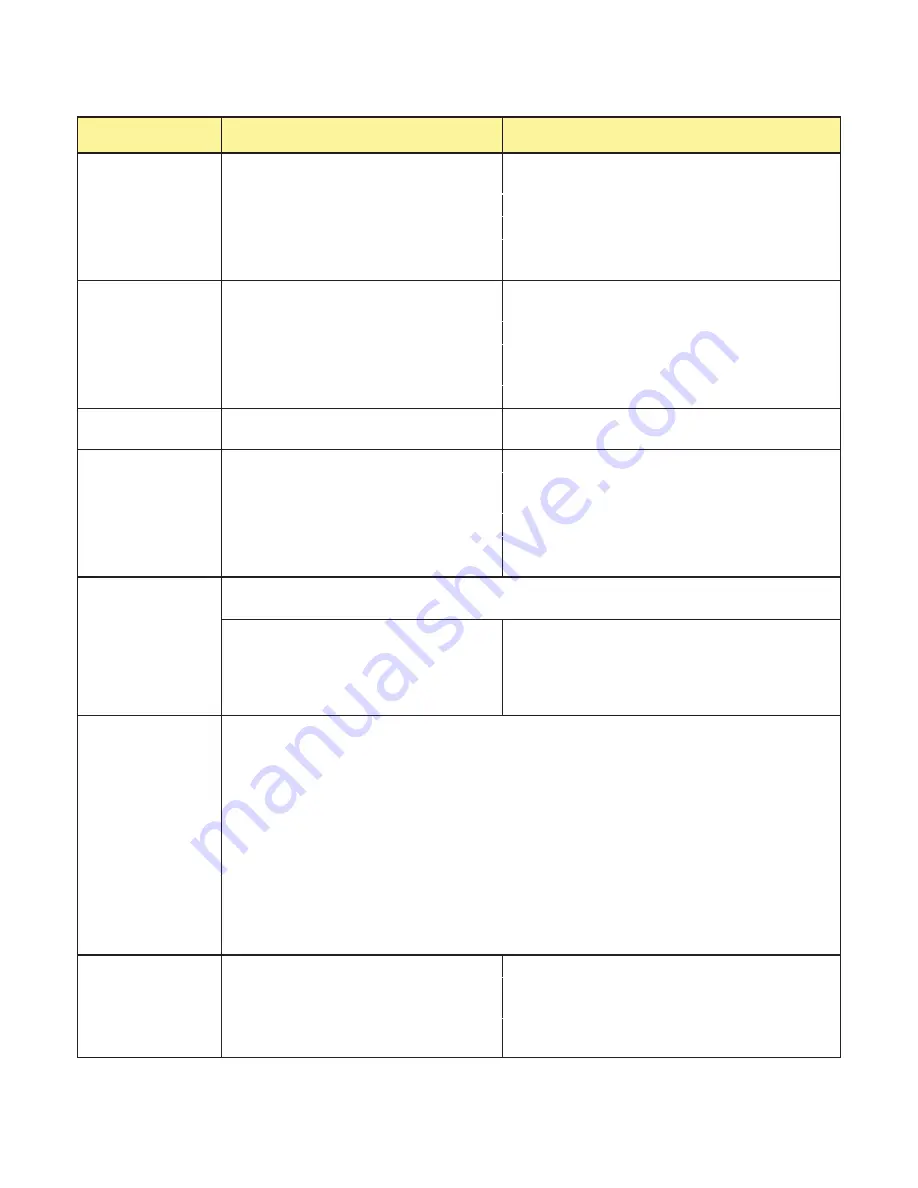
32
PROBLEM
POSSIBLE CAUSE
REMEDY
Overrun too high.
1
Mix pump hose service life is
exceeded.
1
Reposition/replace mix pump hose.
2
Out of mix.
2
Replenish mix supply.
3
Overrun setting too high.
3
Decrease overrun setting.
4
Pick-up leg of mix pump hose is
collapsing.
4
Reposition hose.
Replacement mix
pump hose won’t
feed through pump.
1
Feeding hose into discharge hole of
mix pump cover.
1
Feed hose into suction side of cover.
2
Hose ends not cut squarely.
2
Carefully cut hose end off squarely (no tails).
3
Force feeding too quickly.
3
Gently and slowly assist feeding of hose up
into pick-up hose side of cover.
4
Pump motor not running.
4
Turn on motor switch.
Air exiting mix pick-
up hose.
1
Pickup tube check valve missing.
1
Contact local Stoelting Distributor.
Dispensed product
air “pops”
1
Overrun setting too high.
1
Decrease overrun setting.
2
Mix pump hose service life is
exceeded.
2
Reposition/replace mix pump hose.
3
Overdrawing the machine’s capacity.
3
Reduce dispense rate.
4
Recent low mix condition.
4
Open spigot fully and allow excess air to
escape.
Mix leakage from
pump.
CAUTION: To prevent mix pump damage from dried mix deposits, immediately
disassemble and clean pump.
1
Mix pump hose service life is
exceeded.
1
Remove mix pump hose. Disconnect pump
from power source. Remove mix pump cover/
clamp. Clean the rollers a small amount of
soapy water. Clean mix from pump. See
Section 4.2 for hose replacement.
Pump is noisy/
squeaking.
Note: The action of the air compressor rocking arm creates a repetitive clicking sound during
operation. This is normal.
Note: The peristaltic mix pump has three squeeze rollers that use self lubricating bearings.
If squeaking exists with the mix pump hose in place and stops with the hose removed, the
squeeze roller bearings can be lubricated using a silicone based spray. Remove the mix
pump hose. Disconnect pump from electrical power. Remove four cover/clamp thumbscrews.
Remove entire cover/clamp as one unit. Spray silicone based lubricant on each end of each
squeeze roller. Spin rollers to work lubricant into bearings. Repeat as needed.
Caution: Do not use cleaning/dissolving type lubricants like wd-40. These lubricants
are not bearing friendly and will accelerate bearing wear.
Mix in air hoses.
1
Air/mix tee above black cover/clamp.
1
Air/mix tee must be below black cover/clamp.
2
Air leak.
2
Check stainless steel tube connection. Tighten
all hose clamps.
3
Mix hose on wrong air/mix tee fi tting.
3
Refer to diagram for correct hose connections.