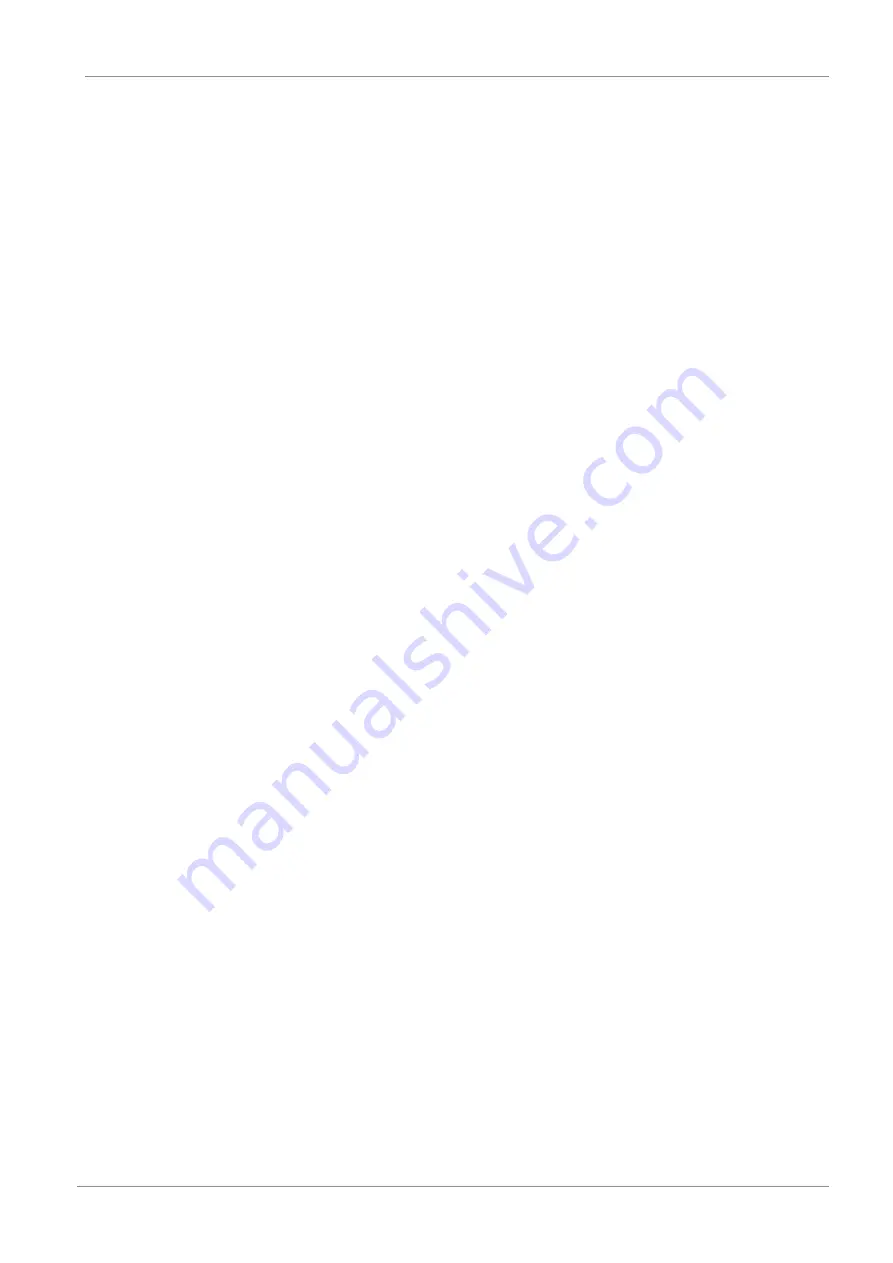
STOBER
9 | Looking for more information about EtherCAT?
02/2020 | ID 443025.06
63
9.5.2.1.2
Optimize values and correct problems
You have commissioned your EtherCAT network. If you need to optimize synchronization using distributed clocks after the
fact due to insufficient EtherCAT communication quality, we recommend the following measures.
9.5.2.1.2.1
EtherCAT master: DC-Sync configured for EtherCAT slaves?
Check whether DC-Sync is configured for all EtherCAT slaves on the master's end. If this is not the case, change the
configuration as described below.
ü
You are in AutomationControlSuite.
1.
Navigate to the first of the added drive controllers in the device tree and double click to open it.
2.
Distributed Clock
:
Select DC
: The list entry
DC enabled (multiplier = 1)
must be selected.
Sync 0
: The option
Enable Sync 0
must be activated.
Cycle Time, Sync Offset
: Make sure that the default settings match the corresponding values of A291 Cycle time
control and A293 PLL gain in DriveControlSuite.
3.
If you would like to change the default settings, activate the option
Additional
>
Enable Expert Settings
and adjust the
settings accordingly.
4.
Repeat steps 2 and 3 for all of the slaves in your EtherCAT network.
9.5.2.1.2.2
EtherCAT slave: Check PLL control
Check the status of PLL control for all EtherCAT slaves and take one of the described measures if necessary.
ü
You are in DriveControlSuite.
1.
Highlight the relevant drive controller in the project tree and click on the first projected axis in the project menu >
Wizard
area.
2.
Select the
PLL synchronization
wizard.
ð
A298 shows the status of the synchronization between the controller and the drive controller in question.
3.
Bit 0 – 1: PLL engaged
If one or both of the two associated LEDs lights up, the control range is working at ≥ 50% capacity (frequency too high
or too low).
In this case, adjust the cycle time of the Sync 0 signal on the master's end. Note that the cycle time of the Sync 0 signal
must be a whole-number multiple of the cycle time A150.
4.
Bit 2: Cycle time extended
If the associated LED lights up, the PLL has performed an extending control intervention on the task system.
5.
Bit 3: Maximum control range reached
If the associated LED lights up, check whether the cycle times of the master and drive controller agree. Realign these
to each other if necessary.
6.
Bit 4: Cycle time for the synchronization signals is greater than the specification (A296 > A291)
If the associated LED lights up, check whether the cycle times of the master and drive controller agree. Realign these
to each other if necessary.
7.
Bit 5: Control/synchronization deactivated
If the associated LED lights up, set A290 to
1: Active
.