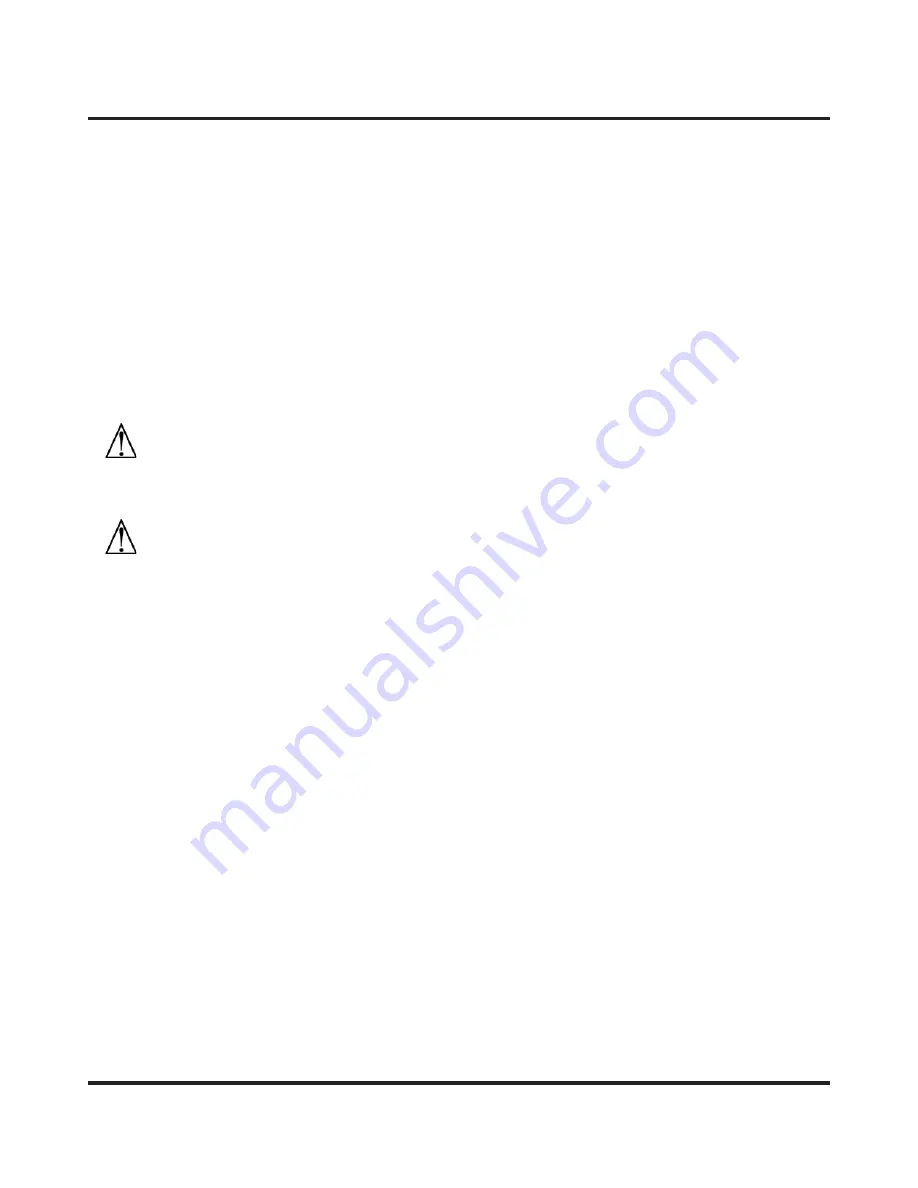
2090-0217 Rev 6
17
STEPS
The liquid push-pull recovery method requires the use of a third hose. In addition,
a sight-glass is useful for determining when all of the liquid has been pushed out
of the system. After all the liquid has been pushed out, you will need to
reconfigure the hoses for vapor recovery since the liquid push-pull recovery
method does not pull a vacuum on the system.
1.
Remove power from the refrigerant device to be evacuated.
2.
Make proper hose connections for liquid push-pull recovery as shown in
Figure 4.
CAUTION:
If the 80% tank full shutoff cord is
not
used, then use a
scale to monitor the refrigerant level in the recovery cylinder in order to
prevent overfilling.
CAUTION:
When recovering R-410A, you must use a recovery cylinder
approved for use with R-410A.
Standard recovery cylinders with
350 psi working pressures are not approved for use with R-410A.
3.
Turn the inlet and outlet valves to their “OPEN” position and the PURGE
valve to its “PURGE” position.
NOTE:
The “PURGE” position bypasses the condenser, optimizing the
push-pull flow rate.
4.
Open both the vapor and liquid valves on the DOT recovery tank.
5.
Turn ON the STINGER. The compressor will begin to “pull” vapors from the
cylinder and “push” the liquid out of the system and into the recovery
cylinder.
6.
If a sight-glass is being used, you should watch it to determine when all of
the liquid has been removed from the system.
7.
The liquid push-pull recovery method will not pull a vacuum in the system.
You must turn OFF the STINGER and reconfigure the hoses for vapor
recovery operations as described on page 13.
Summary of Contents for Refrigerant Recovery Unit
Page 9: ...2090 0217 Rev 6 9 Descriptions of Features Figure 1 Stinger Front View...
Page 15: ...2090 0217 Rev 6 15 Figure 3 Standard Recovery Hose Connections...
Page 18: ...18 2090 0217 Rev 6 Figure 4 Liquid Push Pull Recovery Operation...
Page 21: ...2090 0217 Rev 6 21 Figure 6 Special Notes for R410 A Recovery...
Page 26: ...26 2090 0217 Rev 6 Figure 8 Recovery Tips...
Page 30: ...30 2090 0217 Rev 6 Schematic Diagram Figure 9 Schematic Diagram...
Page 32: ...32 2090 0217 Rev 6 Figure 10 Stinger Exploded View...
Page 34: ...34 2090 0217 Rev 6 Figure 11 Compressor Exploded View...