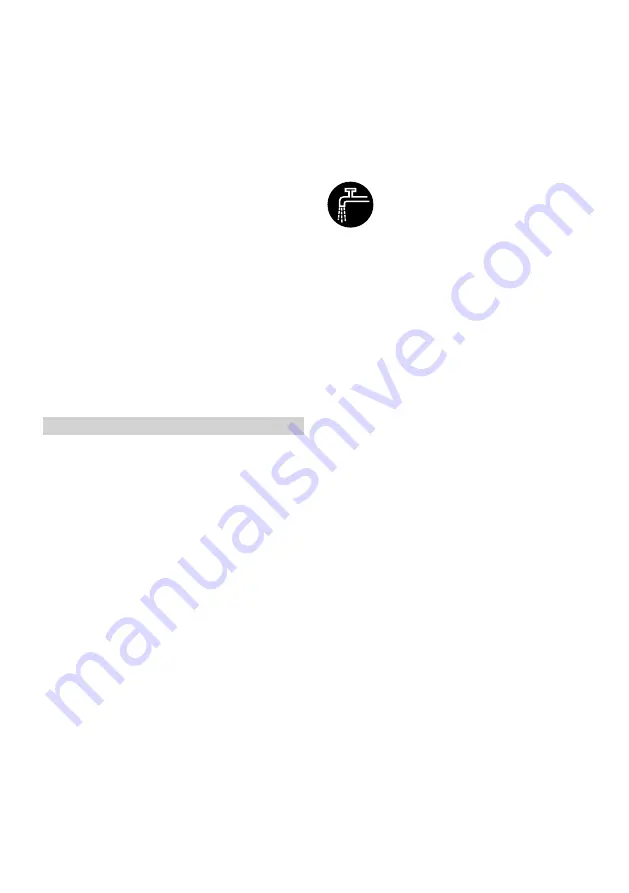
the starter with the spark plug boot removed or
the spark plug unscrewed.
Do not service or store the machine near a
naked flame – risk of fire due to the fuel.
Check fuel cap regularly for tightness.
Use only spark plugs that are in perfect condition
and have been approved by STIHL – see Specifi‐
cations.
Inspect ignition lead (insulation in good condi‐
tion, secure connection).
Check that the muffler is in perfect working con‐
dition.
Do not use the machine if the muffler is damaged
or missing - risk of fire! – Hearing damage!
Never touch a hot muffler – risk of burns!
Check the rubber buffers underneath the
machine - the housing must not rub against the
ground - risk of damage!
The condition of the antivibration elements influ‐
ences vibration behavior – inspect antivibration
elements periodically.
3
Sample Applications
3.1
Water must always be used for
wet cutting when working with
diamond abrasive wheels
3.1.1
Extend service life and increase cut‐
ting speed
Always ensure a supply of water to the abrasive
wheel.
3.1.2
Binding dust
The abrasive wheel must be supplied with at
least 0.6 liters of water per minute.
3.1.3
Water attachment
–
Water attachment on the machine for all types
of water supplies
–
Pressurized water tank 10 l for binding dust
–
water tank usable on the cut-off machine cart
for binding dust
3.2
Use composite resin abrasive
wheels with or without water –
depending on version
Depending on the version, resin abrasive wheels
are only suitable for dry cutting or only for wet
cutting.
3.2.1
Composite resin abrasive wheels suit‐
able only for dry cutting
During dry cutting, wear a suitable dust mask.
If fumes or smoke are anticipated (e. g., when
cutting composite materials), wear respiratory
protection.
3.2.2
Composite resin abrasive wheels suit‐
able only for wet cutting
Use abrasive wheel only with water.
To bind dust, the abrasive wheel must be sup‐
plied with at least 1 liter of water per minute. To
avoid a reduction in cutting performance, the
abrasive wheel must be supplied with not more
than 4 liters of water per minute.
After using the abrasive wheel, the wheel should
be allowed to continue spinning at operating
speed for approx. 3 to 6 seconds without water in
order to spin off the water remaining on it.
–
Water attachment on the machine for all types
of water supplies
–
Pressurized water tank 10 l for binding dust
–
water tank usable on the cut-off machine cart
for binding dust
3.3
Observe with diamond and
composite resin abrasive
wheels
3.3.1
Objects to be cut
–
Must be fully supported
–
Must be secured so it cannot roll or slip off
–
Must be prevented from vibrating
3.3.2
Severed parts
With openings, recesses, etc., the sequence of
the cuts is important. Always make the last cut
so that the abrasive wheel does not become jam‐
med and so that the operator is not endangered
by the severed or separated part.
If necessary, leave small ridges that hold the part
that is to be separated in position. Break these
ridges later.
Before finally separating the part, determine:
–
how heavy the part is
–
how it can move after separation
–
whether it is under tension
When breaking out the part, do not endanger
assistants.
English
3 Sample Applications
10
0458-370-8321-C
Summary of Contents for TS 410
Page 1: ...TS 410 420 2 36 Instruction Manual...
Page 37: ...26 EC Declaration of Conformity English 0458 370 8321 C 37...
Page 38: ...English 26 EC Declaration of Conformity 38 0458 370 8321 C...
Page 39: ...26 EC Declaration of Conformity English 0458 370 8321 C 39...
Page 40: ...www stihl com 04583708321C 04583708321C 0458 370 8321 C 0458 370 8321 C...