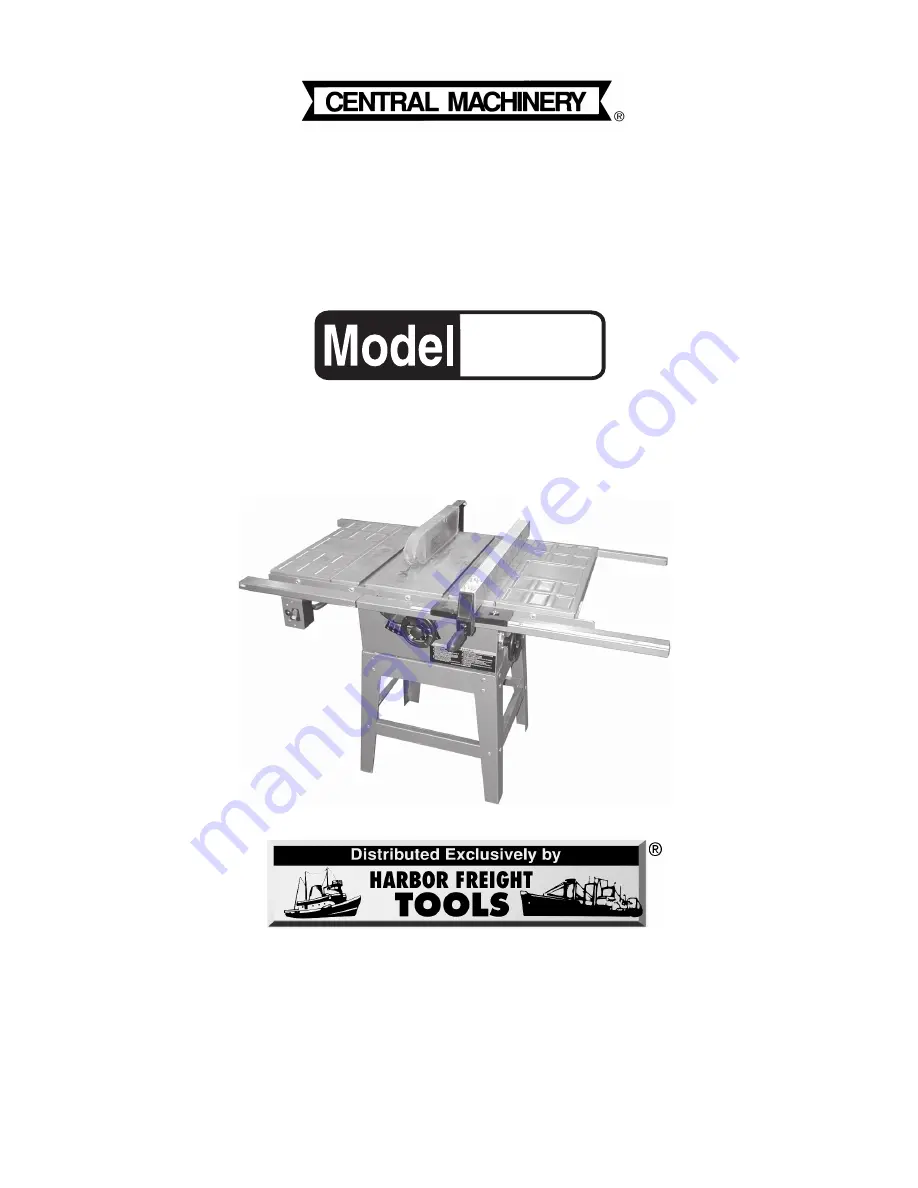
T
T
T
T
TABLE SA
ABLE SA
ABLE SA
ABLE SA
ABLE SAW - 10 INCH
W - 10 INCH
W - 10 INCH
W - 10 INCH
W - 10 INCH
DIRECT DRIVE
DIRECT DRIVE
DIRECT DRIVE
DIRECT DRIVE
DIRECT DRIVE
ASSEMBLY AND OPERATING INSTRUCTIONS
3491 MISSION OAKS BLVD., CAMARILLO, CA 93011
VISIT OUR WEB SITE AT HTTP://WWW.HARBORFREIGHT.COM
Copyright © 2004 by Harbor Freight Tools
®
. All rights reserved. No portion of
this manual or any artwork contained herein may be reproduced in any shape
or form without the express written consent of Harbor Freight Tools.
For technical questions and replacement parts, please call 1-800-444-3353
91815