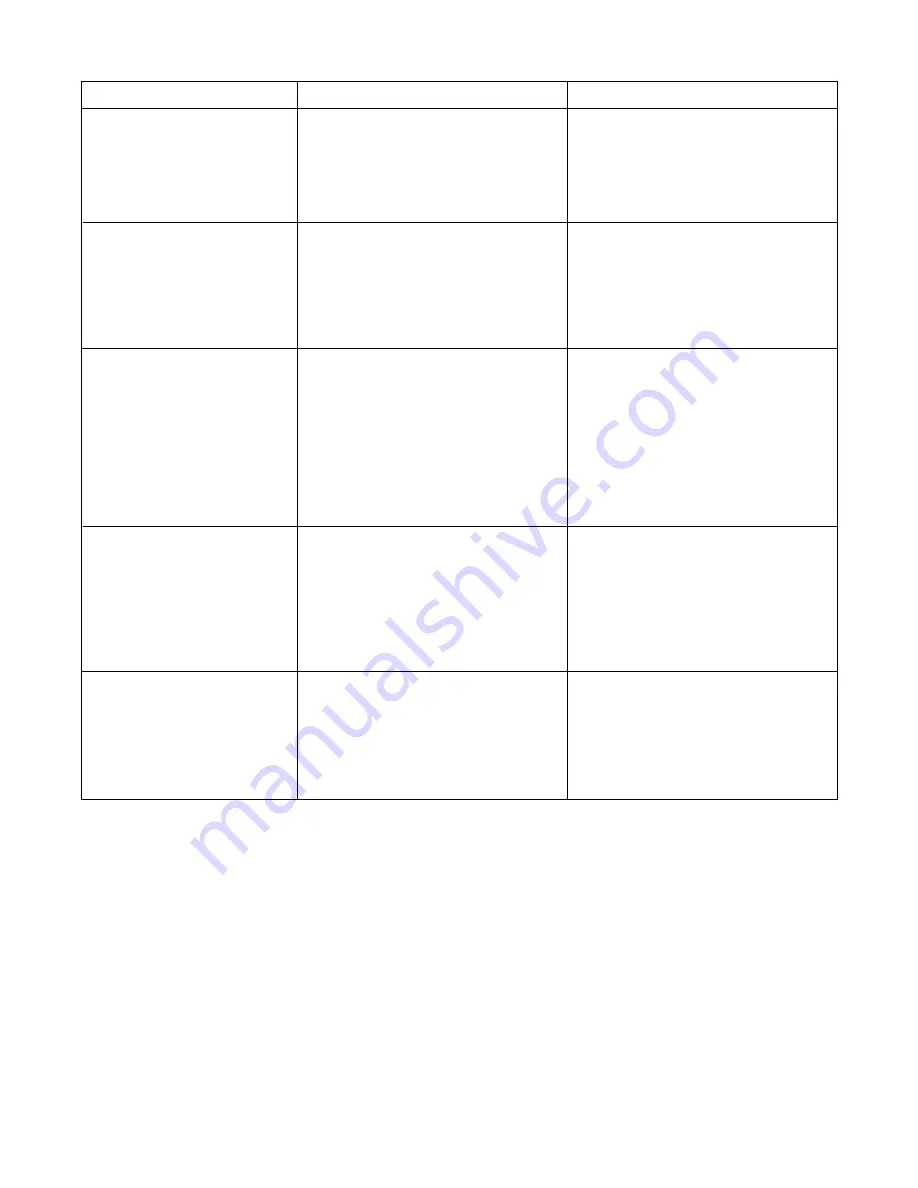
25
Table 7 - Troubleshooting Guide
SYMPTOMS
POSSIBLE CAUSE(S)
CORRECTIVE ACTION
1. Incorrect manifold pressure
or
input.
2. Voltage to unit too high.
3. Air through put too high.
1. Thermostat not calling for heat.
2. No low voltage.
3. Spark gap closed or too wide.
4. Broken or cracked ceramic on
spark
electrode.
1. Loose S8600 connections.
2. Improper gas pressure.
3. Is spark in pilot gas stream?
4. No pilot gas — do not use match
to test - presence of gas is easily
detected by the odor.
1. Loose S8600 connections.
2. Cracked or broken sensor ceramic.
3. Check sensor/spark lead for
continuity.
4. Measure 24 volts from term.
MV to term. MV/PV.
1. Unit is overfi ring.
2. Air fl ow too low
3. Defective
switch.
1. Refer to "Operation".
2. Check motor voltage with fan
running. Should be 115 volts AC.
3. Refer to "Operation".
1. Close thermostat contacts.
2. Check for 24V across
24V terminals of S8600.
3. Set gap to 0.1".
4. Replace pilot assembly.
1. Check all connections, term.
PV feeds 24V to pilot valve.
2. Check pressure — pressure that
is either too high or too low may
cause a problem.
3. Spark should arc from electrode.
4. Check pilot line for kinks. Ensure
there are no drafts.
1. Check connections-term.
MV feeds main valve.
2. Replace pilot assembly.
3. Replace if needed.
4. If present, replace main valve; if
not, replace S8600 Igniter.
1. Manifold pressure too high; adjust.
Burner
orifi ces may be too large:
verify/replace if req'd.
2. Increase air fl ow; check fan size.
Check for proper voltage.
3. Replace.
V. Cold air is delivered
during heater operation.
W.
No
spark.
X. Spark present but pilot
does not light.
Y. Pilot lights — Main valve
does not energize.
Z. Hi-Limit switch tripping.