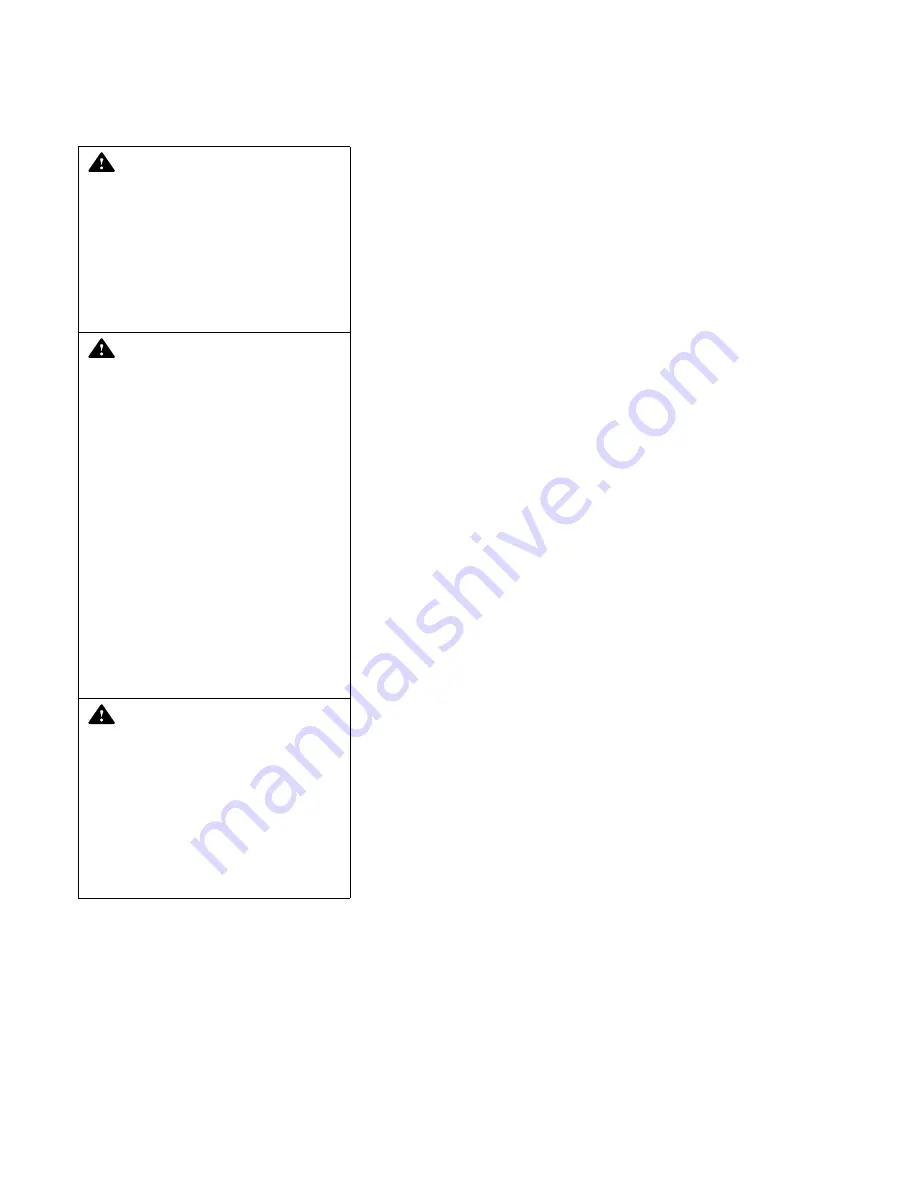
6-11
Routine Maintenance
Operator Manual
920509-645
6.5.2 Clean Side Tanks
Side tanks must be cleaned once every two months using Manual
Control mode as follows:
1.
Press
MANUAL
touch pad
to access Manual Control mode and
display menu of available manual functions.
2.
Press
DRAIN
touch pad to select DRAIN function.
3.
A menu screen appears listing chamber sump and other washer
tanks which may be drained using this function.
4.
Press
ALKALINE TANK
or
ACID TANK
touch pad to begin
draining corresponding tank.
5.
Allow tank to drain.
6.
Lock disconnect switch in OFF position and close building sup-
ply valves.
7.
Open manual drain valve (see Figure 6-4) to allow any remaining
liquids to drain.
8.
Lift off tank cover and flush out tank by spraying inside of tank
with a hose. Allow tank to drain and replace tank cover.
9.
Close drain valve.
10. Repeat procedure for each tank.
11. Re-energize washer utilities.
•
Side tank with guaranteed temperature (option):
Partially drain side tank using Manual Control mode as follows:
1.
Press
MANUAL
touch pad to access Manual Control mode.
2.
Press
DRAIN
touch pad function.
3.
A menu screen appears listing chamber sump and other washer
tanks which may be drained using this function.
4.
Press
COOLDOWN
touch pad to begin draining cooldown
(drain discharge) tank.
5.
Allow tank to partially drain, then press
COOLDOWN
touch pad
to stop cooldown tank draining.
6.
Lock disconnect switch in
OFF
position and close building sup-
ply valves.
7.
Lift off cover and flush out tank spraying inside of tank with a
hose.
8.
Replace tank cover and re-energize washer utilities.
9.
Resume draining side tank.
10. When draining is complete, screen returns to drain menu.
11. Press
X
touch pad to return screen to manual function menu.
12. Press
X
touch pad to return to Mode Selection screen.
WARNING – ELECTRIC SHOCK
HAZARD: Disconnect all utili-
ties to washer before servic-
ing. Do not service washer
unless all utilities have been
properly locked out. Always
follow local occupational
health and safety regulations,
as well as electric and plumb-
ing codes.
WARNING – CHEMICAL BURN
AND/OR EYE INJURY HAZ-
ARD: Washer detergents are
caustic and can cause
adverse effects to exposed
tissues. Do not get in eyes, on
skin or attempt to swallow.
Read and follow precautions
and instructions on detergent
label and in Material Safety
Data Sheet (MSDS) prior to
handling detergent, refilling
detergent container, or servic-
ing detergent injection pump
or lines. Wear appropriate
Personal Protective Equip-
ment (PPE) whenever han-
dling detergent or servicing
detergent injection pump and
lines.
WARNING – BURN HAZARD:
• Allow unit to cool down
before performing any ser-
vice on mechanical compo-
nents and on piping.
Components and piping
become very hot during
operation.
• Pipes may be extremely
hot.
Summary of Contents for Basil 4700
Page 1: ...MAINTENANCE MANUAL Basil 4700 Cage and Rack Washer 2008 10 15 P764333 097 ...
Page 3: ...OPERATOR MANUAL Basil 4700 Cage and Rack Washer 2008 08 14 P920509 645 ...
Page 172: ...2 764333 099 Figure 1 Basil 4700 Cage and Rack Washer Inside Washer Inside Inside Washer ...
Page 174: ...4 764333 099 Figure 2 Cabinet Assembly Left Side Control Shown ...
Page 176: ...6 764333 099 Figure 3 Sump and Floor Grating Assembly ...
Page 178: ...8 764333 099 Figure 4 Door Assembly ...
Page 180: ...10 764333 099 Figure 5 Double Door Interlock System ...
Page 182: ...12 764333 099 Figure 6 Interior Light ...
Page 184: ...14 764333 099 Figure 7 Safety Emergency Stop Cable Assembly ...
Page 186: ...16 764333 099 Figure 8 Spray Header Assembly ...
Page 188: ...18 764333 099 Figure 9 Cable and Roller Assembly DETAIL A DETAIL B See Detail A See Detail B ...
Page 192: ...22 764333 099 Figure 11 Automatic Water Rack Flush System For Two Racks Option ...
Page 194: ...24 764333 099 Figure 12 Damper 1 ...
Page 196: ...26 764333 099 Figure 13 Exhaust Fan ...
Page 198: ...28 764333 099 Figure 14 Hot Water Line Components 6 5 4 10 10 7 8 9 7 ...
Page 200: ...30 764333 099 Figure 15 Cold Water Line Components ...
Page 202: ...32 764333 099 Figure 16 Recirculation Piping ...
Page 204: ...34 764333 099 Figure 17 Steam Line Components ...
Page 206: ...36 764333 099 Figure 18 Final Rinse System Assembly ...
Page 210: ...40 764333 099 Figure 20 Pneumatic Block ...
Page 212: ...42 764333 099 Figure 21 Peristaltic Chemical Injection Pumps ...
Page 214: ...44 764333 099 Figure 22 Solution Tank 25 ...
Page 216: ...46 764333 099 Figure 23 Tank Support Frame ...
Page 218: ...48 764333 099 Figure 24 Guaranteed Cooldown Tank ...
Page 220: ...50 764333 099 Figure 25a Electrical Box and Control Column Assembly ...
Page 226: ...56 764333 099 Figure 26 Control Panel See Detail A DETAIL A ...
Page 228: ...58 764333 099 Figure 27 Seismic Tie Down Anchorage Option ...
Page 230: ...60 764333 099 Figure 28 Bottle Washing Cart WA02 010 ...
Page 232: ...62 764333 099 Figure 29 Bottle Washing Cart WA02 020 ...
Page 234: ...64 764333 099 Figure 30 Pan Cart WA02 030 Accessory ...
Page 236: ...66 764333 099 Figure 31 Universal Cage and Pan Wash Cart WA03 100 7 ...
Page 238: ...68 764333 099 Figure 32 Universal Cage Wash Cart WA02 040 ...
Page 240: ...70 764333 099 Figure 33 Cart Tilt Ramp WA02 050 ...
Page 242: ...72 764333 099 Figure 34 Floor Ramp for Floor Mounted Units WA02 060 ...
Page 244: ......
Page 245: ......
Page 246: ......
Page 247: ......
Page 248: ......
Page 249: ......
Page 250: ......
Page 251: ......
Page 252: ......
Page 253: ......
Page 254: ......
Page 255: ......
Page 256: ......
Page 257: ......
Page 258: ......
Page 259: ......
Page 260: ......
Page 261: ......
Page 262: ......
Page 263: ......
Page 264: ......
Page 265: ......