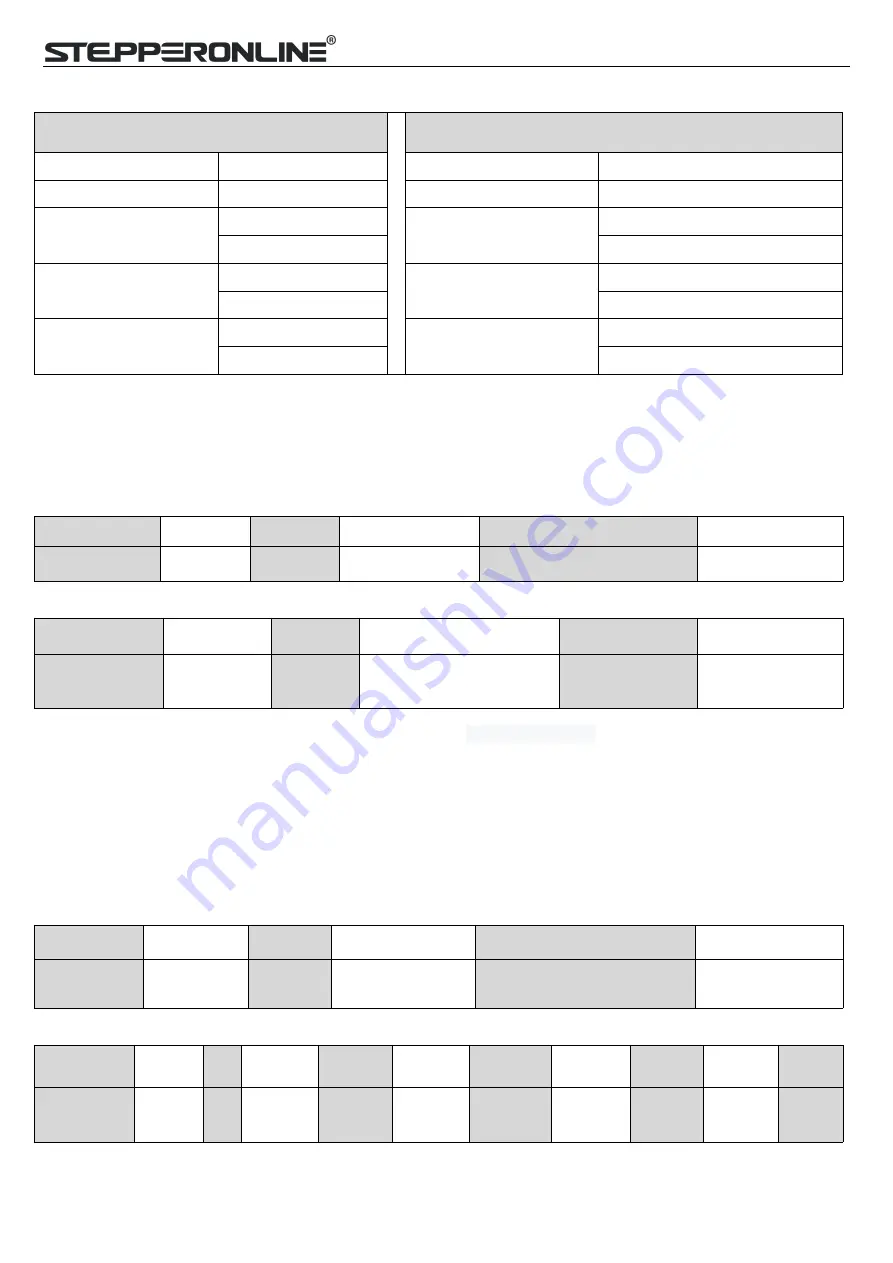
Modbus RS485 Stepper Drive User Manual
15
4.2.1 Read Holding Registers FC= 03
Read Holding Registers Query (Master to
Slave)
Read Holding Registers Response (Slave to Master)
Slave ID
00 - 1F
Slaver ID
00 - 1F
FC
03
FC
03
Address of beginning
register to be read
High
Number of data bytes in
message
High
Low
Low
Total
number
of
registers to be read
High
Data from registers (2
bytes per register)
High
Low
Low
CRC
Low
CRC
Low
High
High
Example A: Read the value of a single register--peak current
Send message: 01 03 01 91 00 01 D3 1B
Receive message: 01 03 02 00 0A 38 43
Details as following:
Master->slave data:
Message:
01
03
01 91
00 01
D3 1B
Description:
Slave ID
FC
Register address Number of registers read
CRC
Slave->master data:
Message:
01
03
02
00 0A
38 43
Description:
Slave ID
FC
Number of bytes returned
Value of 0x01 91
CRC
Note: 0x0191-- output peak current, 000A(Hexadecimal)=10(decimal, unit: 0.1A), it means the current 1A.
Example B: Read multiple register values
Send message: 01 03 01 BC 00 06 05 D0
Receive message: 01 03 0C 00 00 00 02 00 00 00 01 00 00 00 04 B6 13
Details as following:
Master->slave data:
Message
01
03
01 BC
00 06
05 D0
Description
Slave ID
FC
Register address
Number of registers read
CRC
Slave>master data:
Message
01
03 0C
00 00
00 02
00 00
00 01
00 00
00 04
9D B3
Description
Slave
ID
FC
Number
of bytes
returned
Value of
0x01BC
Address
0x01BD
Value of
0x01BE
Value of
0x01BF
Value of
0x01C0
Value of
0x01C1 CRC