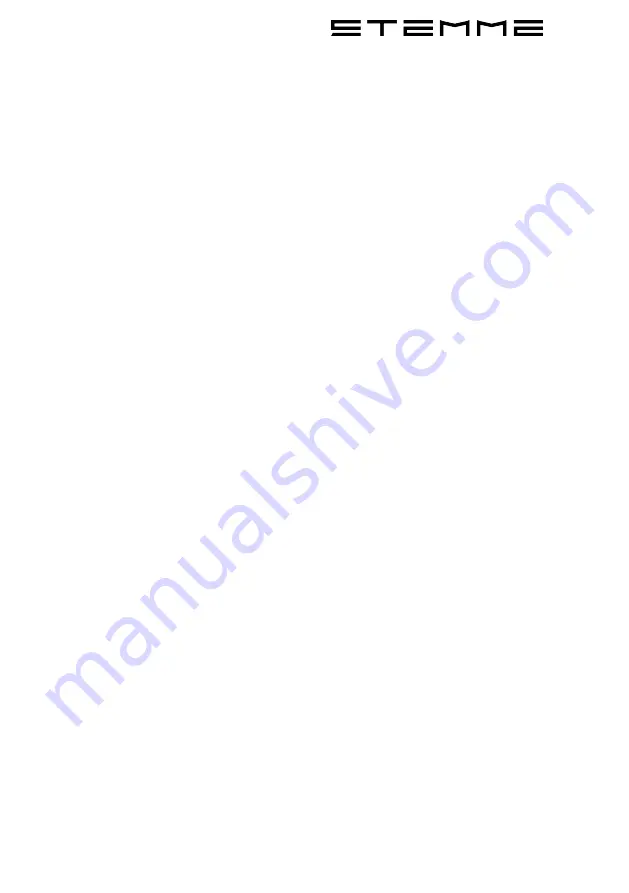
FLIGHT MANUAL TSA-M, VARIANT S6
Doc.-No.:P400-006.000 E
Page: 4-28
Revision: ---
Date of Issue: 07. October 2008
Agency approved
Date of Rev.: --.--.----
4.7.4.2 Glideslope-Control with Low Engine-Power
1. Approach-speed
60 kts / 110 km/h
(recommended
for MTOM)
keep constant until beginning of flare
2. Trim
SET according to approach-speed
3. Flaps
SET to „TO / LDG 1„
4. Cowl-flaps
fully OPEN
5. Auxiliary-fuel-pump
ON
6. Propeller-switch
AUTO
7. Propeller-RPM
SET propeller-RPM to
2100 RPM
8. All caution-lights and warning-
lights
OFF (only green indication-lights
may be ON)
9. Air-brakes
UNLOCK, and extend partially.
LOCK in partially extended
„CENTER“-position (intended for low
engine-power landing).
10. Throttle
OPERATE as required for
glideslope-control
11. Flare and touch-down
Set THROTTLE to IDLE at
beginning of flare. Flare carefully
with the elevator. Let the A/C touch-
down on the main-gear.
12. Wheel-brake
ACTIVATE as necessary after
touch-down.
4.7.4.3 Go-Around (with or without Touch-Down)
According to the selected approach-procedure - glideslope-control with air-
brakes (==> sect. 4.7.4.1) or with low engine-power (sect. 4.7.4.2) – different
procedures for a go-around are recommended.
The main-principle during a go-around is: First operate the lever with
which the glideslope is controlled.
After approach with air-brakes extended:
1. Air-brakes
carefully RETRACT and LOCK