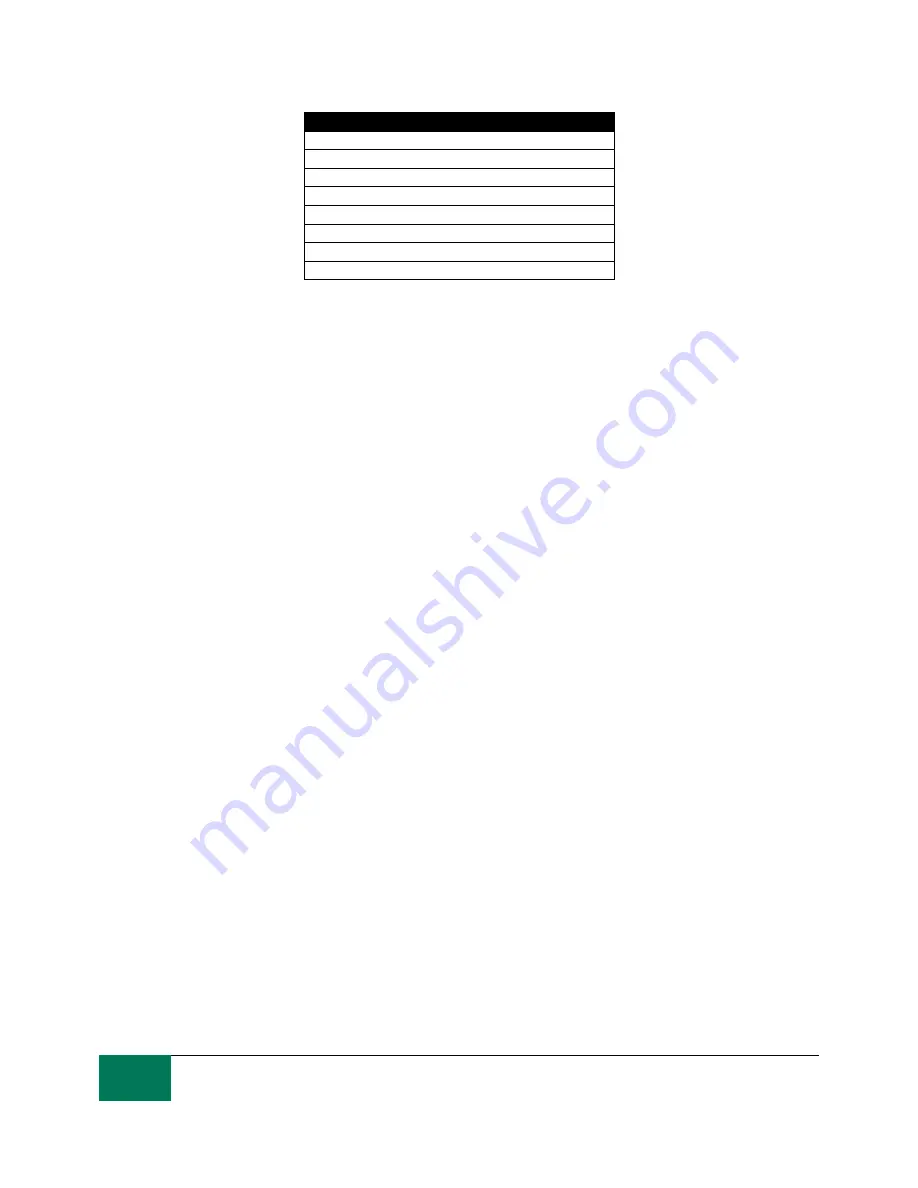
44
As a policy of continual improvement, STAUFF reserves the right to alter the specification without prior notice.
201.031
Date of Issue: 06 November 2018
Number
Function
Comment
40-41
≥4µm (c)
42-43
≥6µm (c)
≥5µm (NAS)
44-45
≥14µm (c)
≥15µm (NAS)
46-47
≥21µm (c)
≥25µm (NAS)
48-49
≥25µm (c)
50-51
≥38µm (c)
≥50µm (NAS)
52-53
≥50µm (c)
54-55
≥70µm (c)
≥100µm (NAS)
Table 6D Particle Count Registers
6.4.1.5 Alarms
6.4.1.5.1 Alarm Mode
The LPM includes two relay outputs that can optionally be used for signaling the state of the unit. These
are normally used in “stand-alone” applications where the Modbus interface is not used (since a Modbus
controller / PLC already has all the exact results available in digital form and can work with these
directly.)
There are a number of preset “modes” that determine the exact function of the relays. Refer to the alarm
mode section for more details (6.3.3.9.2).
These modes are normally set at installation time using our PC software package LASPAC-View. But it
is also possible to use Modbus to set the operating mode of these relays, by writing the corresponding
integer to the alarm mode register 26.
6.4.1.5.2 Alarm Limits
Settable Upper and Lower limits for particulate contamination are provided.
These are two groups of
8 registers representing the “Upper Limit” and “Lower Limit” for particulate
contamination. These are 64-71 and 72-79 respectively.
These are expressed in terms of the result codes using the same format as in 6.4.1.2. An additional
special value of 0x8000 (hexadecimal representation) is used to signify
a “don’t care” setting for that limit
code.
6.4.2 CAN-bus
The LPM supports the major CAN-bus basic message format standards CAN 2.0A (11 bit identifiers) and
CAN2.0B (29 bit identifiers).
J1939 and CanOpen are higher level protocols built on these basic standards. J1939 uses CAN2.0A,
and CanOpen uses CAN2.0B. The LPM does not implement either of these protocols. Instead it defines
a few CAN-bus messages to communicate data. However the message identifiers have been chosen so
as to allow operation with both J1939 and CanOpen. Generally it should be possible to use the LPM with
either, as well as other CAN-bus systems.
6.4.2.1 Installation
Perform a general installation and check of the LPM as detailed in section 6 earlier.
Perform a one-off general configuration check of the LPM using a PC running LASPAC-View e.g.
set it to test continuously and automatically start testing on power up. This procedure is described
earlier in section 6. You will need a suitable RS485 interface, such as the LPM-USB Interface.