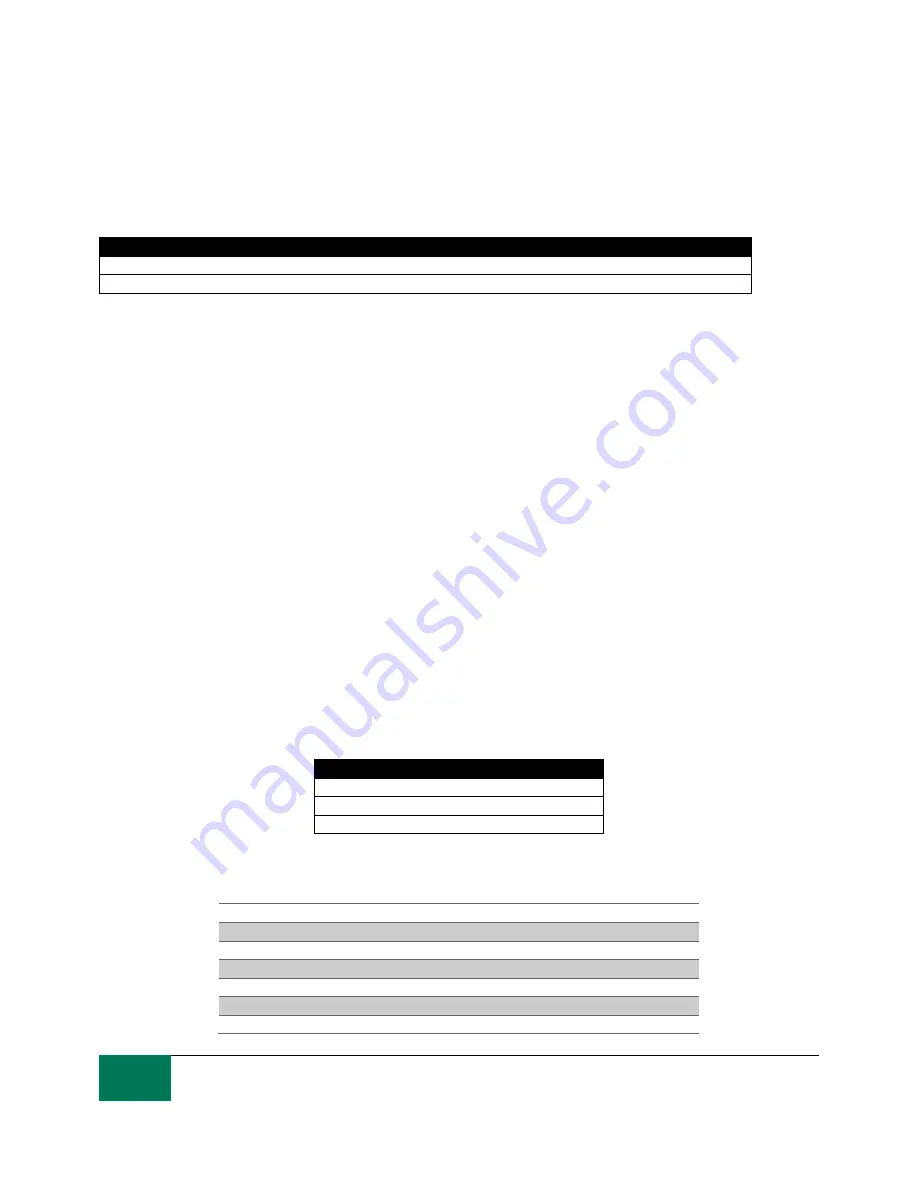
40
As a policy of continual improvement, STAUFF reserves the right to alter the specification without prior notice.
201.031
Date of Issue: 06 November 2018
This is used when controlling tests from a PLC using switched outputs. The PLC gives a start signal,
then monitors the “Test Complete” output. If the test has failed it can detect this with the ”not clean”
signal.
“Continuous testing”’ should not be selected for this mode.
Alarm Mode 6: Testing Not-Clean
Output 1
Output 2
Turns on When
Testing
>Lower
Intended Function
Test in progress Signal
“Not Clean” Signal
This is similar to mode 5 above. The difference is that output 1 is active during the test and turns off at
test end.
“Continuous testing”’ should not be selected for this mode.
Alarm Mode 7… Customer Requested Modes
Other alarm modes will be defined as and when customers request them.
6.4 Standard Communication Protocols
6.4.1 Modbus
The LPM can be controlled via commands on its serial (RS485) interface, using the Modbus RTU
protocol. It is possible to control every aspect and setting of the LPM, as is done by the Stauff LASPAC-
View control software. All results and counts are available in all supported formats. We suggest using
LASPAC-View to initially configure the LPM and check it is performing correctly, and then the customer-
written software only has to read the test results. This could be used to integrate the LPM measurements
with a general machine control, vehicle control or factory monitoring system.
Customers wishing to implement their own Modbus controller software will need to refer to the rest of this
section with further details in section 11.1 and 11.2.
The simplest arrangement is to configure the LPM to test continuously, with a set interval between tests.
For example; a Test Duration of 2 minutes and a Test Interval of 10 minutes.
The Start Testing Automatically selection can be used so that the unit does not require a start signal.
Then, the most recent test results can be read from the appropriate Modbus Registers.
Register
Function
56
4μm Result Code
57
6μm Result Code
58
14μm Result Code
6.4.1.1 Set Up
Protocol Type
RTU (not ASCII)
Data Bits
8
Stop Bits
1
Parity
Required, Even or none
Baud
Auto-sensing 1200-115200
Signaling
RS485
Node Address
4 (or user set)
Figure 6.29 Settings