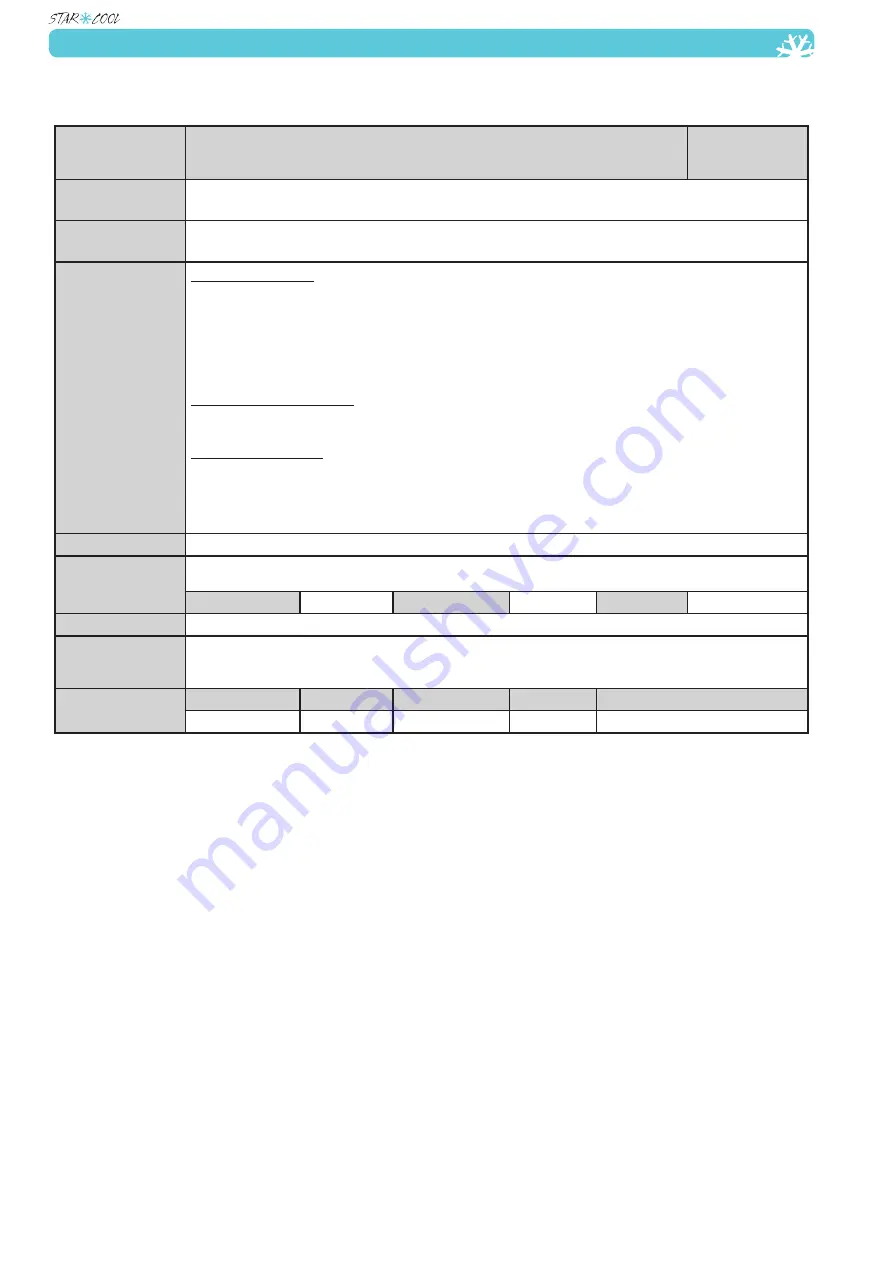
Operating and service manual
132 of 222 pages
Operation Alarms (AL 6XX)
600
No control sensors
Fatal
Alarm
Description
Supply Air Sensor 1, Supply Air Sensor 2, Return Air Sensor and Evaporator
Sensor are all malfunctioning.
Cause
Alarm indicates that all control-relevant sensors are defective or unreliable. See
also
Temperature control
and
Expansion valve control
p.18
Trouble
shooting
Possible causes:
•
Supply Air Sensor 1, Supply Air Sensor 2, Return Air Sensor and
Evaporator Sensor are all malfunctioning.
•
X1 cable is defect.
•
Controller PCB defective.
Accompanied alarms:
•
AL 100 to AL 108.
Trouble shooting:
1) Verify all other sensor alarms AL 100 to AL 3XX and try to remove these
alarms.
2) If this alarm remains active, replace main controller.
Criteria
No valid control sensor values
Controller
action
Unit stops
Log
X
Alarm
X
Alarm light
Quick flash
Consequence
Unit stop
Elimination
When one of the control sensor values enters into the valid area, it is again possible to
control container temperature. For reliability reasons at least one of the control sensor
values must be valid for 30 sec. before sensor may be used as control reference again.
Log data
Parm 1
Parm 2
Parm 3
Parm 4
Parm 5
Active/Inactive