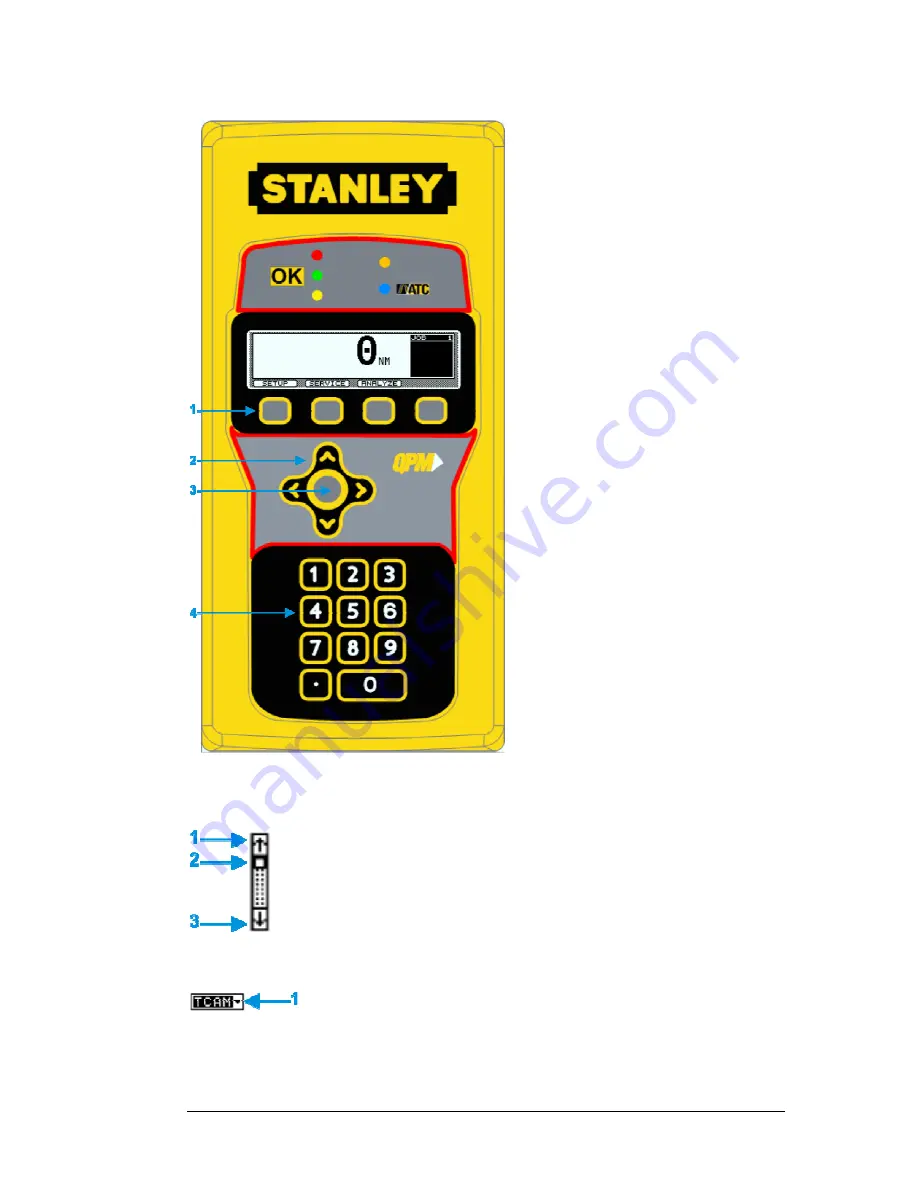
User Manual
8
2.4
QA Theta Controller Navigation and Programming
The Theta controller’s three navigation and
input areas facilitate menu navigation,
selection and data input:
•
Menu buttons
•
Arrows and Toggle button
•
Keypad
Labels for the four interactive menu
buttons [
1
] change with menu selection. If
the label is blank, the button has no
function for the current display.
The up/down arrows [
2
] navigate menu
and character selections; the left/right
arrows enable backspace and space, as well
as navigate between tabs. The toggle
button [
3
] switches between modes and
selects/accepts choices (synonymous with
OK
menu button).
The numeric keypad [
4
] facilitates data
input and menu selection (where
applicable) and job/step selection when
enabled.
2.5
Display
2.5.1
Scroll Bar
A scroll bar appears when more items are available than space within the
display allows. The up arrow [
1
] and down arrow [
3
] direct scrolling. The
black/white scroll bar [
2
] indicates which list items are currently displayed. No
scroll bar means all items are currently displayed.
To navigate between menu items, use the up/down arrows or, if available, use
the keypad to identify the corresponding menu item number.
2.5.2
Dropdown
A dropdown [
1
] arrow appears to the right of menu items with multiple
choices. To view choices, highlight the menu item using the up/down
arrows then use the toggle button to expand the dropdown. Use up/down
arrows to scroll and the toggle or interactive menu button to select/accept.