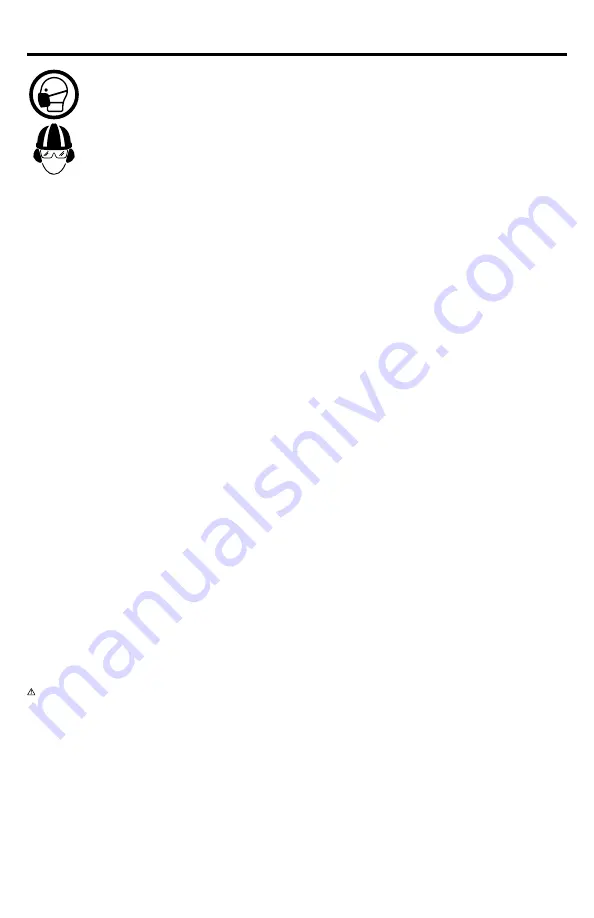
ENGLISH • 15
Hearing, eye and respiratory protection
must be worn.
2. OPERATION
f
To avoid overheating of the electric motor,
this compressor is designed for intermittent
operation as indicated on the technical
dataplate (for example, S3-25 means 2.5 min
ON, 7.5 min OFF). In the case of overheating, the
thermal cutout of the motor trips, automatically cutting
off the power when the temperature is too high. The
motor restarts automatically when normal temperature
conditions are restored.
f
To facilitate restart of the compressor, in addition to
the operations indicated, it is important to return the
button of the pressure switch to the OFF position
and then to ON again (Fig. 1 - 2).
f
Single-phase versions are fitted with a pressure
switch equipped with a delayed closing air discharge
valve which facilitates start-up of the motor.
Therefore venting of air from this valve for a few
seconds with the receiver empty is normal.
f
All the compressors are fitted with a safety valve that
is tripped in the case of malfunctioning of the pressure
switch in order to assure machine safety.
f
The red notch on the pressure gauge refers to the
maximum operating pressure of the tank. It does not
refer to the adjusted pressure.
f
When fitting a tool, the flow of air in output must be
switched off.
f
When using compressed air, you must know and
comply with the safety precautions to be adopted
for each type of application (inflation, pneumatic tools,
painting, washing with water-based detergents only, etc.).
Assemble
¡Important! You must fully assemblethe appliance
before using it for the first time.
Fitting the wheels
Fit the supplied wheel kit as shown in Fig. 3.
Assembly by sequence: a, b, c, d, e.
Fitting the rubber foot
Fit the supplied rubber stopper as shown in Fig. 4.
Fitting the air filter
Remove the shipping plug with a screwdriver or similar and
screw the air filter securely to the equipment (Fig. 5).
Fitting the transport handle
Screw the transport handle to the compressor as shown
in Fig. 15.
3. VOLTAGE
The compressor is equipped with a mains cable with
shock-proof plug. This can be connected to any shock-
proof socket which is protected by a 16 A fuse. Before
you use the machine, make sure that the mains voltage
complies with the specifications on the rating plate. Long
supply cables, extensions, cable reels etc. cause a drop in
voltage and can impede motor start-up. In the case of low
temperatures below +5°C, motor start-up is jeopardized as
a result of stiffness.
4. START-UP AND USED
f
Check for correspondence between the compressor
plate data with the actual specifications of the
electrical system. A variation of ± 10% with respect
of the rated value is allowed.
f
Insert the plug of the power cable in a suitable
socket
(Fig. 6), checking that the button of the
pressure switch located on the compressor is in
the
OFF «O» position.
f
Check the oil level by means of the oil dipstick
(Figs. 7), and if necessary top up.
f
At this point, the compressor is ready for use.
f
Operating on the switch of the pressure switch
(Fig. 1), the compressor starts, pumping air into
the receiver through the delivery pipe.
f
When the upper calibration value (set by the
manufacturer) has been reached, the compressor
stops, venting the excess air present in the head and
in the delivery pipe through a valve located under the
pressure switch.
This facilitates subsequent restart due to the absence
of pressure in the head. When air is used,
the compressor restarts automatically when the lower
calibration value is reached (2 bar between upper and
lower). The pressure in the receiver can be checked
on the gauge provided (Fig. 8).
f
The compressor continues to operate according to
this automatic cycle until the switch of the pressure
switch is turned.
f
Always wait at least 10 seconds from when the
compressor has been switched off before restarting this.
f
All compressors are fitted with a pressure reducer.
Operating on the knob with the tap open (turning
it in a clockwise direction to increase the pressure
and in a counterclockwise direction to reduce this,
Fig. 9a), air pressure can be regulated so as to
optimize use of pneumatic tools. After setting the
value required, the ring-nut underneath must be
tightened to fasten the knob (Fig. 9b).
f
The value set can be checked on the gauge.
Summary of Contents for STC24
Page 2: ...3a 4a 4b 1a ON 2a OFF 1b ON 2b OFF 3b a c b e d...
Page 3: ...6 7b 7a 8b 8a 5b 4c 5a...
Page 4: ...9a 9b 10 11a 12 11b...
Page 5: ...14a 13a 13b 13c 14b 15...