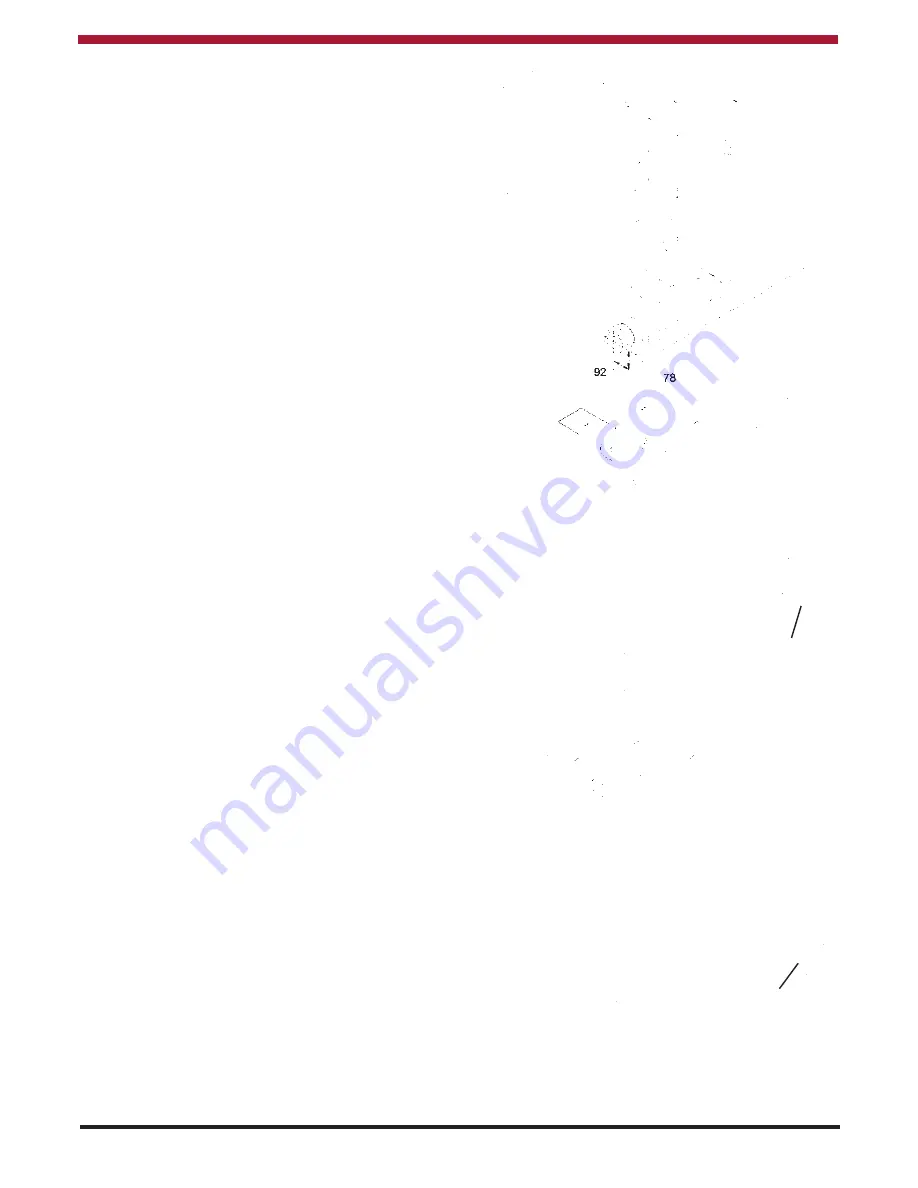
13
12. Where such an installation exists, a test for
spillage should be made with the fan or fans
and other burning appliances in operation at full
rate (i.e. extraction fans, tumble dryers) with all
external doors and windows closed.
13. If spillage occurs following the above operation,
an additional air vent of sufficient size to prevent
this occurrence should be installed.
OUTSIDE AIR CONNECTION
If this option is used additional air as indicated in BS
5410 is not required.
1.
This appliance may be connected direct to the
outside of the house for its combustion air
supply.
2.
Remove the blanking plate located at the back
right hand corner and remove the primary air
grill located at the front right hand corner. Fix
the blanking plate over the front primary air
inlet. (See fig. 14)
3.
Connect the optional 125mm (5”) spigot to the
base. (See fig. 14a).
4.
To connect this appliance to an outside air
supply use either 125mm (5”) rigid or flexible
stainless steel pipes or non-combustible
corrosion-resistant materials not more than
965mm (38”) in length and having no sharp
bends or corners other than the down turn at the
terminus.
5.
Air inlets traversing cavity walls should include
a continuous duct across the cavity. The duct
should be installed in such a manner as not to
impair the weather resistance of the cavity.
6.
Joints between air vents and outside walls
should be sealed to prevent ingress of moisture.
HEATING
PIPE FITTINGS
Materials used for insulation work should be fire
resistant. Standards should conform to all
appropriate regulations in force at the time and
place of installation.
1.1 Ferrous Materials
BS 1387 Steel tubes.
BS 1740 Steel pipe fittings.
BS 4127 Stainless steel tubes.
BS 6956 Jointing Materials.
1.2 Non-Ferrous Materials
EN 29453 Soft Solder Alloys.
BS 864 Compression tube fittings.
BS 2871 & BS EN 1057 Copper & Copper
Alloys.
Fig.14
Fig.14a
Fig.13
Air Inlet
Blanking Plate
Outside Air Spigot
(Not Supplied)