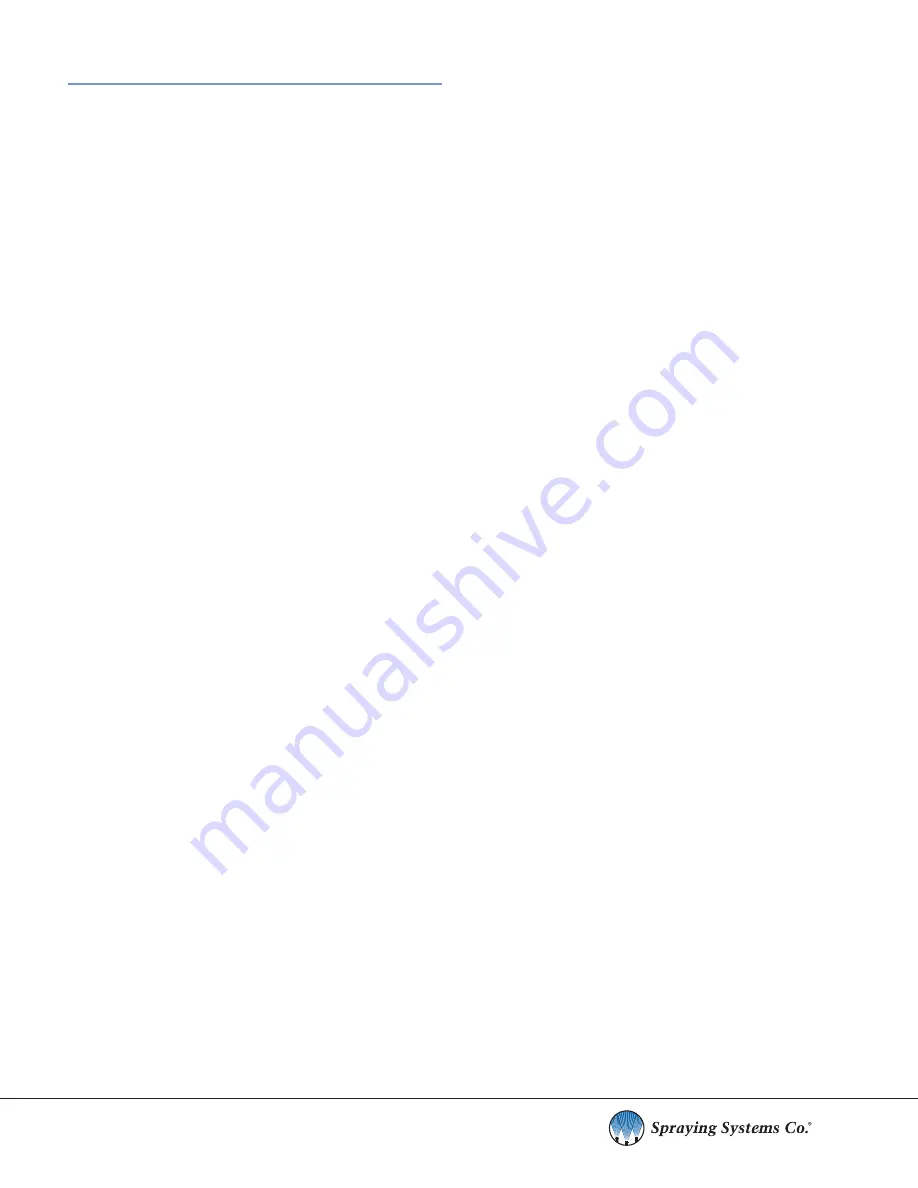
7
spray.com | 1.800.95.SPRAY | Intl. Tel: 1.630.665.5000
PREVENTATIVE MAINTENANCE
TankJet
®
360 series has been designed to operate under a wide
variety of conditions and to provide long-term reliability with a
minimum amount of servicing . All wear parts are engineered for quick
inspection and simple replacement . Servicing can be accomplished in
the field, eliminating the need to send machine elsewhere for repair
or maintenance .
Each cleaning application is unique, and therefore affects the seals,
o-rings, cups and bearings in a different way . A good preventative
maintenance program tailored for your specific tank cleaning machines
will help to eliminate the possibility of failure during a cleaning cycle,
or the need to replace major cast parts later from excessive wear . The
expense of periodic inspection and subsequent replacement of wear
parts on a regular basis is less costly than waiting until the machine
fails to replace parts . The added advantage to PM is that you have
control over when a machine is to be serviced; either between batches
or during the off season, instead of during a cleaning cycle when you
need reliability the most . Check with your sales representative for
advice on establishing a PM program at your facility .
CLEANING SOLUTION FILTRATION
It is recommended that a strainer be placed in line with the pump to
filter out small particles which could lodge inside the tank cleaning
machine decreasing its efficiency . This is very important where
recirculation of the cleaning solution is being employed . The mesh and
wire size of the strainer will vary depending on the type of cleaning
and particle size . Be certain that the water supply system has been
flushed out to remove any solid particles before attaching TankJet
360 . Following each use of the TankJet 360, we recommend a clean
water rinse to thoroughly remove any cleaning solution (recirculated
or new) residue which could affect the seals and o-rings during non
operational storage .
GEARBOX LUBRICATION
Oil level inside the gearbox should be checked regularly; the specific
time period to be determined by the type of service the machine is
in . The more severe the service, the more often it is recommended to
check the oil level . To inspect oil level, turn machine upside down and
remove the gearbox cover . The oil level should just cover the lower
(22) gearset on the (18) final drive shaft (about 1" below the machined
end of the gearbox) . All lubricated machines are supplied with the
following type of oil:
OIL TYPE: Food Grade U.S.D.A. Acceptable H-1
QTY. 14 oz. (414 ml.) S.A.E. – 90
Oil Alternatives:
For non-food industry applications, H-2 lubricants
can be used such as Keystone Keygear 90, KLC-20/50 or KSL-365 .
Lightweight gear oils (50-90) are also suitable . It should be noted that
heavy weight (140) gear oils or greases will alter the performance of
the machine regarding cycle times . If upon inspection of the gearbox
there is cleaning solution mixed into the gear oil, then it is advisable to
inspect the rotor shaft seals (31), final shaft seal (38) and the gearbox
cover o-ring (34) . Replace seals and o-rings as necessary .
SEALS AND O-RINGS
All of the standard TankJet 360 series are shipped with o-rings
constructed of a Flourocarbon Elastomer (Viton) compound . This
compound is suitable for a broad range of temperatures and chemical
resistance . Other materials are available . The type of cleaning
application and chemicals used will in large part determine the length
of service for o-rings . Upon inspection, if an o-ring has any cracks,
worn sections or is swollen in size, then replacement is recommended .
The spring energized seals (part #’s 35, 36, 37 and 38) have a PTFE
alloy jacket which increases the longevity and sealing capabilities .
Once the seals have worn thru the jacket to the spring, they are no
longer providing a proper seal . Particles in the cleaning solution are
then able to lodge in the machine, decreasing its efficiency, and
perhaps stopping it altogether . Prolonged use with worn out seals can
damage the castings the seals were meant to protect .
A regularly scheduled inspection program is recommended for the
main bearing seals (35 and 36) . Inspection is easily accomplished by
removing the nameplate (6) and the nozzle housing assembly (5) . If
these seals are worn, or need to be cleaned of deposits, then the tee-
housing seals will also need attention .
INSPECTION OF WEAR PARTS
All of the bearing clearances in TankJet 360 series have been
designed to provide the best possible support for the adjacent parts,
while maintaining reliability between servicing . Most of the bearing
clearances are very close when the machine is assembled at the
factory . This allows for longer periods of operation before overall
machine performance is altered due to bearing wear . In many cases,
the bearings can wear down 25% and the machine will continue
to operate properly . It should be noted that while the machine may
continue to operate with worn bearings, it is recommended that
bearings be changed at the first evidence of wear to protect the
long term performance and reliability of the unit . In severe service
(high pressure and/ or chemical concentration), the period between
servicing will be shortened . Several parts in TankJet 360 have been
designed as replaceable wear parts . These parts are easily replaced
in the field at a reasonable cost, with a minimum of down time or
labor costs .
Main Bearing:
After removal, inspect the bearings; they may have
grooves on the O .D . from particles or deposits that may have lodged
between the bearing and cup during machine operation .
Also, if the clearance between the bearing O .D . and the cup I .D . is
loose compared to when new, it may be time to change the bearings .
The normal clearances between cups and bearings are held to close
tolerances to maintain proper mesh of the bevel gears (10 and 11),
and to allow the maximum amount of wear on the bearings before
they need to be replaced .
Like any other type of bearing, if allowed to wear beyond normal limits
or if used in severe service without any maintenance, the bearings may
fail, which could alter the performance of the machine . Refer to page
8 – Nozzle Housing Assembly Removal . Subsequently, if the nozzle
housing bearings need replacement, then the tee housing bearings
will also need to be changed . Refer to page 10 – Tee Housing .
Cups:
After extended use, the cups may show signs of wear from one
of the seals (36 or 35) that has worn thru the jacket into the spring .
Rotation of the nozzle housing or tee housing against the static seal
can wear a groove into the cup . This groove will prevent proper
sealing when a new seal has been installed . Replacement of the cup
is recommended whenever visual grooves or wear marks are evident .
(See
Disassembly Procedure
for removal) .
Cups will also wear out from rotation against the bearings; however,
often times the bearings can be changed two or three times before
Summary of Contents for TankJet 360 Series
Page 1: ...MI TJ360 TJ180 spray com TankJet 360 Series Tank Cleaners USER GUIDE TJ180 TJ360...
Page 15: ...15 spray com 1 800 95 SPRAY Intl Tel 1 630 665 5000 PRODUCT VIEWS...
Page 16: ...16 spray com 1 800 95 SPRAY Intl Tel 1 630 665 5000...
Page 17: ...17 spray com 1 800 95 SPRAY Intl Tel 1 630 665 5000...
Page 18: ...18 spray com 1 800 95 SPRAY Intl Tel 1 630 665 5000...
Page 19: ...19 spray com 1 800 95 SPRAY Intl Tel 1 630 665 5000...
Page 24: ...24 spray com 1 800 95 SPRAY Intl Tel 1 630 665 5000 EXPLODED VIEW AND PARTS LIST...
Page 25: ...25 spray com 1 800 95 SPRAY Intl Tel 1 630 665 5000...
Page 26: ...26 spray com 1 800 95 SPRAY Intl Tel 1 630 665 5000...
Page 27: ...27 spray com 1 800 95 SPRAY Intl Tel 1 630 665 5000...
Page 28: ...28 spray com 1 800 95 SPRAY Intl Tel 1 630 665 5000 5...
Page 29: ...29 spray com 1 800 95 SPRAY Intl Tel 1 630 665 5000...
Page 31: ...31...