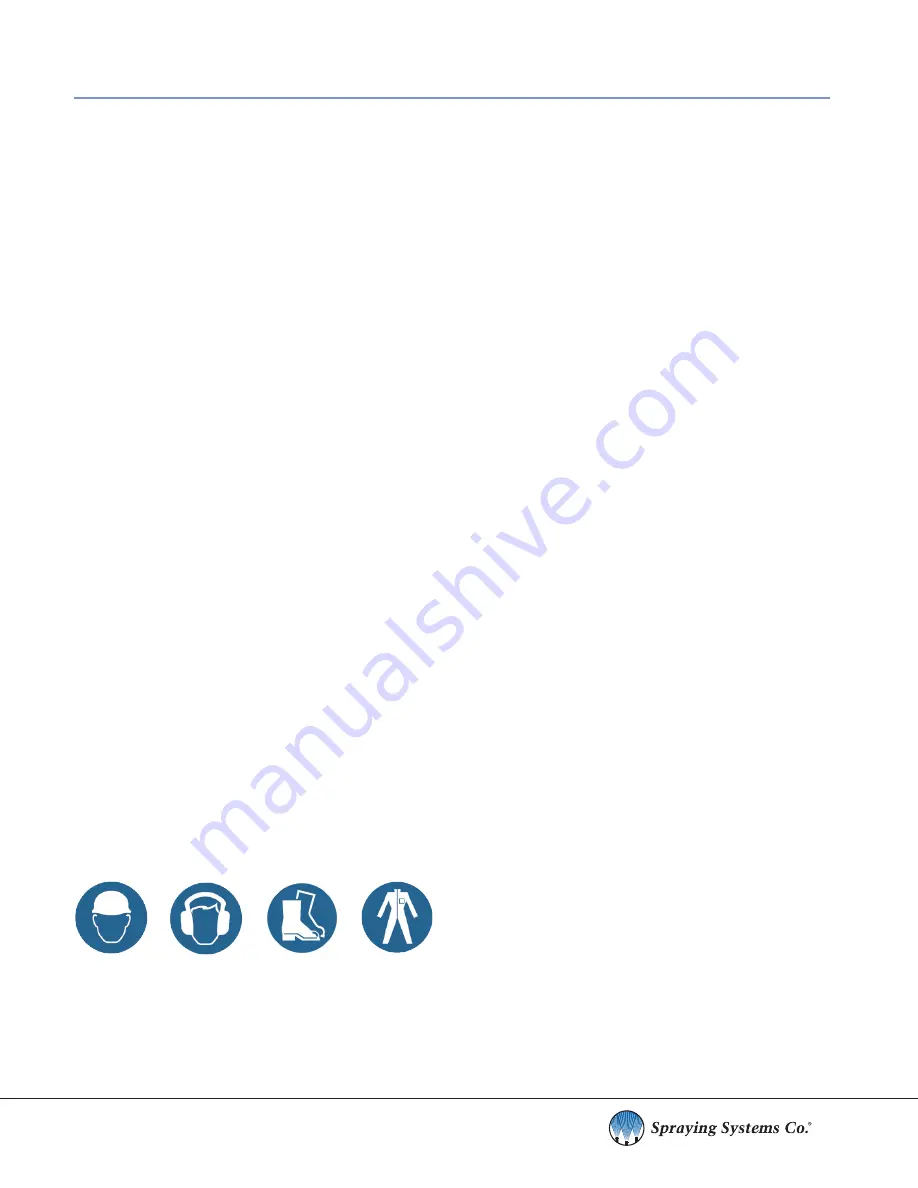
3
spray.com | 1.800.95.SPRAY | Intl. Tel: 1.630.665.5000
READ THE FOLLOWING INSTRUCTIONS:
WARNING:
All safety related and operating instructions should
be read before the nozzle is operated. Follow all operating
instructions. Failure to do so could result in serious injury.
• WARNING:
It is important to recognize proper safety
precautions when using a pressurized spray system. Fluids
under pressure can penetrate skin and cause severe injury.
• WARNING:
When dealing with pressure applications, the
system pressure should never exceed the lowest rated
component. Always know your system and all component
capabilities, maximum pressures and flow rates.
• WARNING:
Before performing any maintenance, make sure
all liquid supply lines to the machine are shut off and /or
disconnected and chemical/fluid are drained.
• WARNING:
The use of any chemicals requires careful
control of all worker hygiene.
• WARNING:
Spraying Systems Co. does not manufacture
or supply any of the chemical components used in this
equipment and is not responsible for their effects. Because
of the large number of chemicals that could be used and
their different chemical reactions, the buyer and user of this
equipment should determine compatibility of the materials
used and any of the potential hazards involved.
• WARNING:
Spraying Systems Co. strongly recommends the
use of appropriate safety equipment when working with
potentially hazardous chemicals.
• WARNING:
Before use be sure appropriate connections are
secure and made to withstand weight and reaction forces
of the operating unit.
This equipment includes but is not limited to:
• Protective hat
• Safety glasses or face shield
• Chemical-resistant gloves and apron
• Long sleeve shirt and long pants
NOTE: Always remember to carefully read the chemical
manufacturer’s label and follow all directions.
• WARNING:
DO NOT USE TO SPRAY FLAMMABLE LIQUIDS-
-SUCH USE COULD RESULT IN FIRE OR EXPLOSION
CAUSING BODILY INJURY OR DEATH.
• WARNING:
It is important to operate equipment within
the temperature range of all components. Also insure that
appropriate time lapses or proper safety equipment is used
when handling components after they’re exposed to high
temperatures.
• WARNING:
Never operate tank cleaning equipment in the
open due to the potential of bodily injury.
• WARNING:
Remove equipment from the tank before
attempting any repairs.
• WARNING:
If walking on top of a tank is deemed safe and
is necessary, use proper safety precautions to protect
individuals as well as the equipment.
• WARNING:
Do not put any part of your body in the tank
during operation of the tank cleaner. This is NOT a safe
procedure for verification of operation.
• WARNING:
Proper hoisting procedures should be used
when installing and removing all equipment.
• WARNING:
To insure the safety of the equipment as well as
the individuals using them, only use Spraying Systems Co.
components.
• WARNING:
When packaging and transporting use
structurally sound boxes or crates that can handle the
weight of the equipment.
• WARNING:
Tank cleaners should be flushed out with clean
water before they’re stored or shipped to minimize health
hazards or cross contamination.
• WARNING:
Do not use any equipment outside the intended
purposes of the product. Misuse can result in personal
injury or product damage.
The container being cleaned should be sealed as best as possible
while the TankJet model is running its cycle . The combination of
temperature, cleaning solution, spray impact and the potential toxic
materials being cleaned can cause a hazard to anyone in the path of
the spray .
NOTE: Due to the possible build up of electrical charge caused by
the nature of the machine it’s vital to avoid applications involving
combustible fluids and materials.
GENERAL SAFETY INSTRUCTIONS
Summary of Contents for TankJet 360 Series
Page 1: ...MI TJ360 TJ180 spray com TankJet 360 Series Tank Cleaners USER GUIDE TJ180 TJ360...
Page 15: ...15 spray com 1 800 95 SPRAY Intl Tel 1 630 665 5000 PRODUCT VIEWS...
Page 16: ...16 spray com 1 800 95 SPRAY Intl Tel 1 630 665 5000...
Page 17: ...17 spray com 1 800 95 SPRAY Intl Tel 1 630 665 5000...
Page 18: ...18 spray com 1 800 95 SPRAY Intl Tel 1 630 665 5000...
Page 19: ...19 spray com 1 800 95 SPRAY Intl Tel 1 630 665 5000...
Page 24: ...24 spray com 1 800 95 SPRAY Intl Tel 1 630 665 5000 EXPLODED VIEW AND PARTS LIST...
Page 25: ...25 spray com 1 800 95 SPRAY Intl Tel 1 630 665 5000...
Page 26: ...26 spray com 1 800 95 SPRAY Intl Tel 1 630 665 5000...
Page 27: ...27 spray com 1 800 95 SPRAY Intl Tel 1 630 665 5000...
Page 28: ...28 spray com 1 800 95 SPRAY Intl Tel 1 630 665 5000 5...
Page 29: ...29 spray com 1 800 95 SPRAY Intl Tel 1 630 665 5000...
Page 31: ...31...