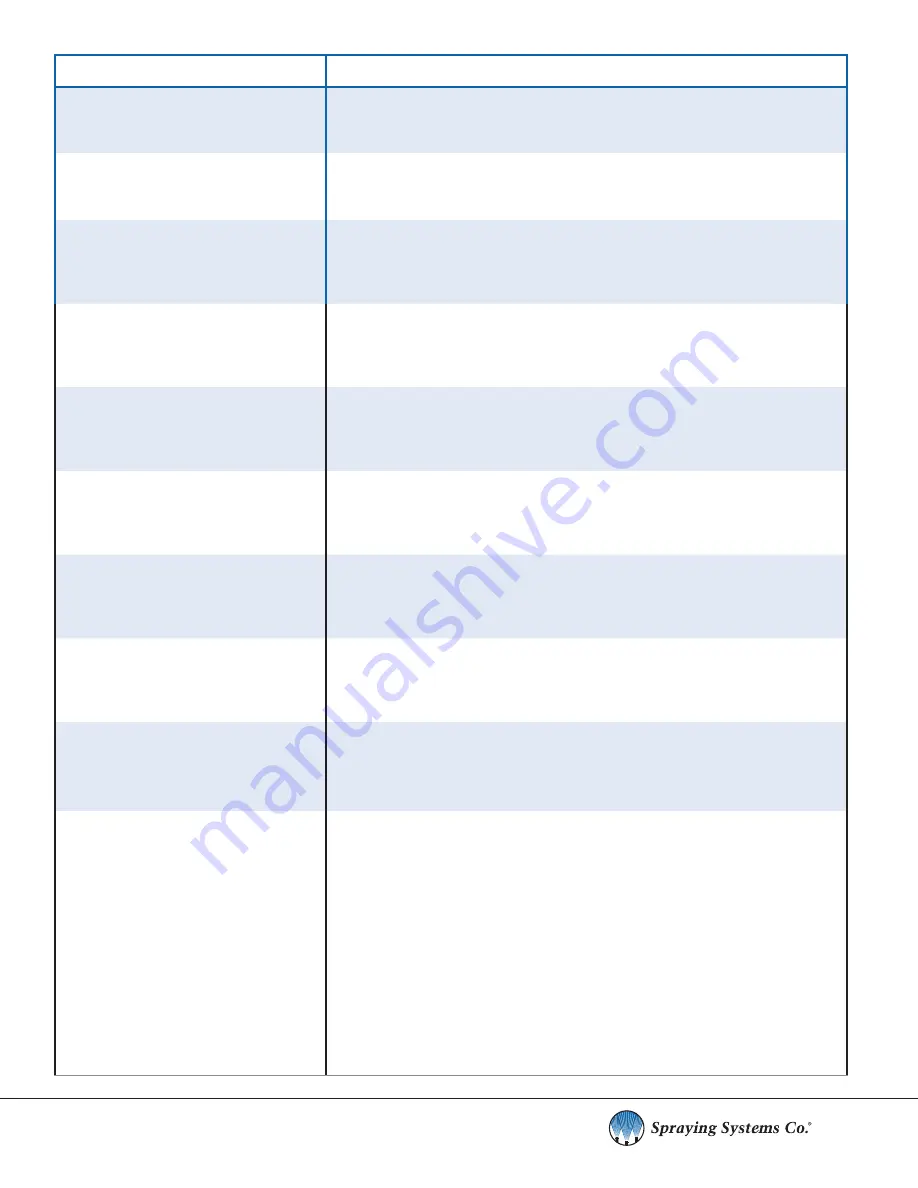
13
spray.com | 1.800.95.SPRAY | Intl. Tel: 1.630.665.5000
PROBLEM
SOLUTION
Machine configuration & cycle time
(Inadequate cleaning)
Verify that the rotor/stator combination, nozzle size & gear ratio are configured properly
for the type of cleaning required . Contact your local distributor or representative for further
recommendations .
Cleaning solution composition &
temperature (Cleaning and wear
problems)
Check to see that the proper concentration and type of chemicals is being used for the material
being cleaned, and that the solution is heated to the proper temperature .
Loose rotor nut
Check to see that the rotor retaining nut (59) is properly tightened on the rotor shaft . If the rotor
nut is loose, the rotor may be rotating on the shaft, instead of rotating the rotor shaft through
the geartrain . Tighten the rotor nut as described in the Rotor Installation . Torque setting should
be 100 in/lbs .
Rotor shaft difficult to turn
• Misalignment of the carbide rotor shaft bearings (46, 47) can prevent smooth rotation .
Rotate rotor shaft bearing with Tool # T-5, then check the alignment once again .
• Foreign material jammed in geartrain . Remove gearbox cover (2) for inspection . Remove
foreign material, reassemble geartrain and install gearbox cover (2) as described .
Rotot shaft turns, but the tee housing does
not
This is an indication of possible geartrain malfunction . If the rotor shaft pinion gear or any of
the gearsets (23) are worn out, then the tee housing will not rotate . Remove gearbox cover (2)
for inspection, replace worn gears as necessary .
Deposits, scale, foreign material in the tee
housing bearings
• Inspect the seals (35) for signs of wear . If they are worn out, they will allow particles
in the cleaning solution in between the cups and bearings, which will alter the
performance of the machine . Replace bearings, cups and seals as necessary .
• Install an inline strainer to filter out sediment in the cleaning solution .
Erratic rotation of tee-housing
If you are able to observe the machine in operation and notice the tee housing rotating, then
stopping briefly, then rotating again, this could be due to improperly installed ring gear . The ring
gear notch (see photo # 4, page 16) must be locked into the tee housing tab (photo # 3, page 16) .
Clogged stator or rotor
Remove stator retaining ring (39) and lift out stator (8) . Remove any foreign objects from
the stator or rotor that could be altering the normal flow of cleaning solution .
Excessive water leakage
In the CIP version of TankJet® 360 series, some water leakage at the gap between the tee
housing & gearbox and at the gap between the nozzle housing & tee housing is normal . There
are two small holes in the tee housing that rinse the bevel gears, ring gear and the inside
of several of the castings to prevent a buildup of deposits or sediment that could promote
bacteriological growth .
Worn tee-housing seals
If TankJet 360 series is allowed to operate for a prolonged period of time after the seals have
worn out, foreign particles will lodge between the inlet stem and the tee housing bearings and
cups and cause abrasive wear on these parts . Corrosive chemicals can also have an effect on
the sealing effectiveness . If the grooves or corrosion is severe, even new seals will not seal
completely due to the uneven sealing surface .
Excessive water leakage at the top and bottom of the tee housing indicates a sealing problem
which can be caused by:
• Seals worn out; no longer functioning properly . Replace worn seals .
• Seals improperly installed . The spring side of the seal (the open section of the seal)
faces the ports on the inlet stem .
• Inlet Stem (3) casting or tee housing cups (32) have wear grooves which prevent the
seals from sealing . Replace the cups . Reassemble the machine and then check for
excessive leakage . If there is still excessive leakage after installing new cups and
seals, the inlet stem may have to be replaced .
Summary of Contents for TankJet 360 Series
Page 1: ...MI TJ360 TJ180 spray com TankJet 360 Series Tank Cleaners USER GUIDE TJ180 TJ360...
Page 15: ...15 spray com 1 800 95 SPRAY Intl Tel 1 630 665 5000 PRODUCT VIEWS...
Page 16: ...16 spray com 1 800 95 SPRAY Intl Tel 1 630 665 5000...
Page 17: ...17 spray com 1 800 95 SPRAY Intl Tel 1 630 665 5000...
Page 18: ...18 spray com 1 800 95 SPRAY Intl Tel 1 630 665 5000...
Page 19: ...19 spray com 1 800 95 SPRAY Intl Tel 1 630 665 5000...
Page 24: ...24 spray com 1 800 95 SPRAY Intl Tel 1 630 665 5000 EXPLODED VIEW AND PARTS LIST...
Page 25: ...25 spray com 1 800 95 SPRAY Intl Tel 1 630 665 5000...
Page 26: ...26 spray com 1 800 95 SPRAY Intl Tel 1 630 665 5000...
Page 27: ...27 spray com 1 800 95 SPRAY Intl Tel 1 630 665 5000...
Page 28: ...28 spray com 1 800 95 SPRAY Intl Tel 1 630 665 5000 5...
Page 29: ...29 spray com 1 800 95 SPRAY Intl Tel 1 630 665 5000...
Page 31: ...31...