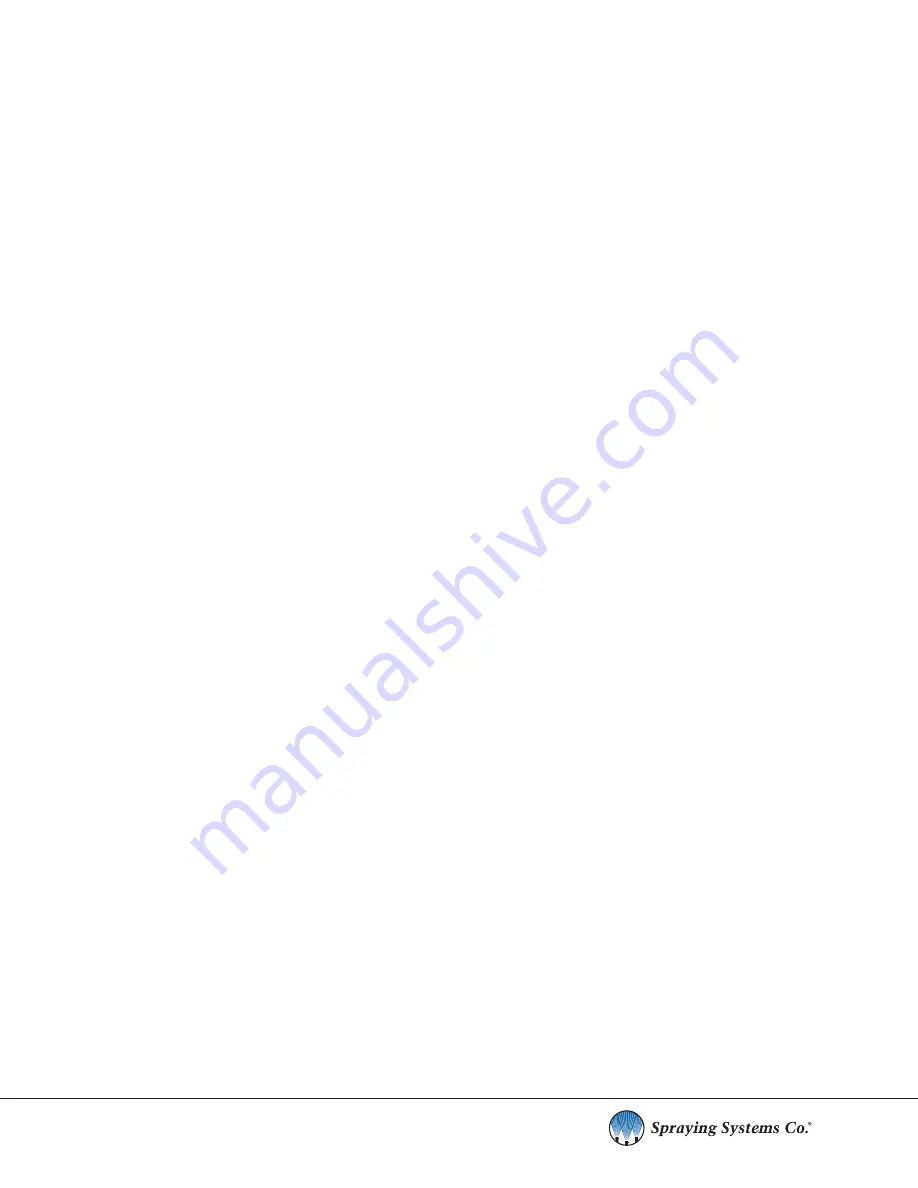
9
spray.com | 1.800.95.SPRAY | Intl. Tel: 1.630.665.5000
gearbox (1) . When draining oil, be careful not to lose the 2 carbide
thrust washers (23) .
√ visually inspect the gearbox cover o-ring (54) for swelling
or cracking .
√ inspect the idler shaft lower bearing (28) and the final
shaft lower bearing (30) for wear on the flange surface
thickness and the I .D .
√ inspect the rotor shaft thrust bearing (26) for wear on
the flange surface . If the flange thickness has worn
down 50% to 1/32", then it must be replaced . Likewise
if the I .D . has worn and the end of the rotor shaft has
excessive side to side movement, then replacement is
recommended .
Removal of 26, 28 and 30 Bearings:
Using a ¼ - 28 or ¼ - 20 tap;
insert into I .D . and screw down with tap wrench until bearing is forced
up out of gearbox cover bore . Once the tap is bottomed out, use pliers
to finish removing 26 . If the tap does not force the bearing up after
bottoming out in the casting bore, change to the next size of tap (5/16
- 18 or 5/16 - 24) .
28 and 30:
Using a 5/16 - 18 or 5/16 - 24 tap; insert into I .D . and screw
down with tap wrench until bearing is forced up out of gearbox cover
bore . Once the tap is bottomed out, use pliers to finish removal . If the
tap does not force the bearing up after bottoming out in the gearbox
cover casting bore, change to next size of tap (3/8 - 16 or 3/8 - 24) .
GEARTRAIN REMOVAL
NOTE: the rotor must be removed prior to removal of the geartrain.
Remove the rotor shaft assembly (26) and the rotor shaft spacer (42).
Next, remove the idler gear shaft (17) and the 3 gearsets (23). The
remaining final drive gear shaft assembly (18) and the 2 gearsets
(23) can now be removed. A medium length screwdriver with the tip
bent at 90 degrees can assist by prying up on the final shaft bearing
retainer (15) while pulling on the final shaft (18) with your fingers.
NOTE: Do not use pliers or vise grips to pull on the final drive shaft, as
the shaft may be damaged.
√ inspect the gearsets for wear on the teeth . Replace
gearsets when teeth are worn down by approximately
20-25% .
NOTE: The lower idler gearsets (26) with the thrust washer and
the rotor shaft pinion gear (16) will wear faster than the rest of the
gearsets due to rotation speed. Compare gearsets to get an idea of
the wear on the teeth.
√ inspect the idler and final shafts for wear; look for obvious
grooves or highly polished areas . Replace as necessary .
√ inspect the gearset bearings by testing them on the
idler or final shafts; if there is excessive side to side
motion, then replacement of the gearset bearings is
recommended .
NOTE: The idler gear bearing is not a replaceable spare part where
oilite bearings are concerned (normally lubricated gearboxes only).
√ inspect the rotor shaft assembly: check the pinion gear
(16) for wear on the teeth . Inspect the chromium oxide
coated surface for wear from the carbide bearings . If
there are grooves or cracking evident, the rotor shaft
assembly (21) may need to be replaced .
Final Drive Gear Shaft Disassembly:
Replacing upper final shaft
bearing (29): Using an arbor press; press the final shaft assembly (18)
out of the bore of the final drive gear (25) . Support the final drive gear
and press on the final shaft . Remove the final shaft bearing retainer
(15) .
√ inspect the o-ring (51) for cracks or swelling; replace as
necessary .
√ inspect the final drive bearing (29); the I .D . should spin
freely on the larger diameter of the final shaft and pinion
(18) with minimum of side to side motion . Replace the
bearing if the flange thickness is less than 1/32" or if
there is excessive side to side movement of the final
shaft .
Remove the final shaft upper bearing (29) and final shaft seal (38),
using tool #T-7 from the tool kit . Support final shaft bearing retainer
(15) in an arbor press, and press out bearing and seal . The seal will be
damaged in the process and should be discarded and replaced .
GEARBOX DISASSEMBLY
Remove 3 gearbox bolts (40) with a 3/8" deep socket . Remove the
three lockwashers (41) . The gearbox (1) can now be removed from the
inlet stem (3) . If the gearbox (1) does not come off easily, there may be
deposits or scale built up between the inlet stem (3) and the gearbox
(1) . Insert a medium screwdriver between the gearbox and the tee
housing (4) to pry the gearbox loose from the inlet stem .
√ inspect the gearbox stem o-ring (53) for cracks or
swelling, replace as necessary .
Remove the upper rotor shaft bearing (47) or (47) with pliers .
√ inspect the upper rotor shaft bearing (47) for cracks in the
carbide insert, or for obvious wear marks . Check the fit
of the upper rotor shaft bearing (47) over a rotor shaft for
proper bearing clearance .
√ check for wear on the 52 spring seal (lubricated gearboxes
with 47) and replace if worn .
√ inspect the upper idler shaft bearing (27) for excessive
side to side play .
Bearing 27 Removal:
Using a 5/16 - 18 or 5/16 - 24 tap; insert into
I .D . and screw down with tap wrench until bearing is forced up out
of the gearbox bore . If the tap does not force the bearing up after
bottoming out in the casting bore, change to the next size of tap (3/8
- 16 or 3/8 - 24) .
Bearing 46, 14 and 45 Removal:
Remove the lower rotor shaft
bearing (46) and the rotor shaft seal housing (14) from the gearbox
by using tool # T-4 . With gearbox upright, insert T-4 through bore that
housed the upper rotor shaft bearing (47), and either strike T-4 with a
hammer, or use an arbor press . The seal housing spacer (45) protects
the rotor shaft seals (52) from being damaged during disassembly .
TEE HOUSING AND INLET STEM
Remove ring gear retaining ring (20) with a small screwdriver . Lift out
ring gear (12) and bevel gear (10) with your fingers . The tee housing
can now be lifted off of the inlet stem (3) .
√ check the seals (35) to be sure the jacket has not worn
down thru to the spring .
√ examine the bearings (35) for wear . They should be free
Summary of Contents for TankJet 360 Series
Page 1: ...MI TJ360 TJ180 spray com TankJet 360 Series Tank Cleaners USER GUIDE TJ180 TJ360...
Page 15: ...15 spray com 1 800 95 SPRAY Intl Tel 1 630 665 5000 PRODUCT VIEWS...
Page 16: ...16 spray com 1 800 95 SPRAY Intl Tel 1 630 665 5000...
Page 17: ...17 spray com 1 800 95 SPRAY Intl Tel 1 630 665 5000...
Page 18: ...18 spray com 1 800 95 SPRAY Intl Tel 1 630 665 5000...
Page 19: ...19 spray com 1 800 95 SPRAY Intl Tel 1 630 665 5000...
Page 24: ...24 spray com 1 800 95 SPRAY Intl Tel 1 630 665 5000 EXPLODED VIEW AND PARTS LIST...
Page 25: ...25 spray com 1 800 95 SPRAY Intl Tel 1 630 665 5000...
Page 26: ...26 spray com 1 800 95 SPRAY Intl Tel 1 630 665 5000...
Page 27: ...27 spray com 1 800 95 SPRAY Intl Tel 1 630 665 5000...
Page 28: ...28 spray com 1 800 95 SPRAY Intl Tel 1 630 665 5000 5...
Page 29: ...29 spray com 1 800 95 SPRAY Intl Tel 1 630 665 5000...
Page 31: ...31...